2025 Yazar: Howard Calhoun | [email protected]. Son düzenleme: 2025-01-24 13:26
Metroloji, birliklerini sağlamanın yanı sıra gerekli doğruluğu elde etmenin yollarının yanı sıra ölçümler, araçlar ve yöntemler bilimidir. Konusu, belirli bir güvenilirlik ve doğrulukla nesnelerin parametreleri hakkında nicel bilgilerin seçimidir. Metroloji için düzenleyici çerçeve standartlardır. Bu yazıda, bu bilimin bir alt bölümü olan toleranslar ve inişler sistemini ele alacağız.
Parçaların değiştirilebilirlik kavramı
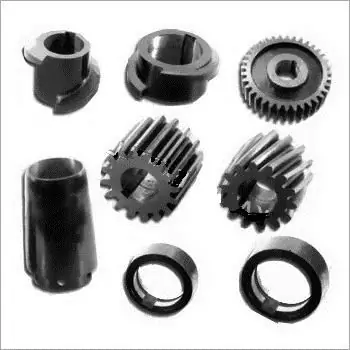
Modern fabrikalarda, traktörler, arabalar, takım tezgahları ve diğer makineler, birim veya onlarca değil, yüzlerce hatta binlerce üretilir. Bu tür üretim hacimleri ile, üretilen her parçanın veya montajın, ek çilingir ayarları olmaksızın montaj sırasında tam olarak yerine oturması çok önemlidir. Sonuçta, bu tür işlemler oldukça zahmetli, pahalı ve çok zaman alıyor, bu da seri üretimde kabul edilemez. Montaja giren parçaların değiştirilmeye izin vermesi de aynı derecede önemlidir.tüm bitmiş ünitenin işleyişine herhangi bir zarar vermeden onlarla diğer ortak amaçlara. Parçaların, düzeneklerin ve mekanizmaların bu şekilde değiştirilebilirliğine birleştirme denir. Bu, makine mühendisliğinde çok önemli bir noktadır, sadece parça tasarlama ve üretme maliyetinden değil, aynı zamanda üretim süresinden de tasarruf etmenizi sağlar, ayrıca çalışması sonucunda ürünün onarımını kolaylaştırır. Değiştirilebilirlik, bileşenlerin ve mekanizmaların önceden seçim yapılmadan ürünlerdeki yerlerini alma ve ana işlevlerini spesifikasyonlara uygun olarak gerçekleştirme özelliğidir.
Eşleşen Parçalar
Birbirine sabit veya hareketli şekilde bağlı iki parçaya çiftleşme denir. Ve bu eklemlemenin gerçekleştirildiği değere genellikle çiftleşme boyutu denir. Bir örnek, kasnaktaki deliğin çapı ve buna karşılık gelen mil çapıdır. Bağlantının gerçekleşmediği değere genellikle serbest boyut denir. Örneğin, kasnağın dış çapı. Değiştirilebilirliği sağlamak için parçaların eşleşen boyutları her zaman doğru olmalıdır. Bununla birlikte, bu tür işlemler çok karmaşıktır ve çoğu zaman pratik değildir. Bu nedenle, teknolojide, sözde yaklaşık doğrulukla çalışırken değiştirilebilir parçalar elde etmek için bir yöntem kullanılır. Farklı çalışma koşulları için, düğümlerin ve parçaların, bu parçaların ünitede kusursuz çalışmasının mümkün olduğu, boyutlarının izin verilen sapmalarını belirlemesi gerçeğinde yatmaktadır. Çeşitli çalışma koşulları için hesaplanan bu tür ofsetler, belirli birbelirli bir şema, adı "birleşik bir toleranslar ve iniş sistemi" dir.
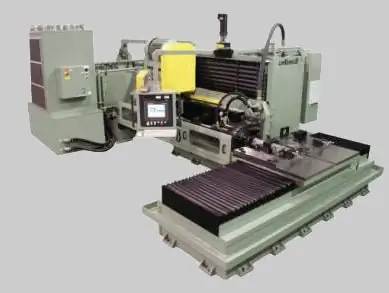
Tolerans kavramı. Miktar özellikleri
Çizimde sağlanan ve sapmaların sayıldığı parçanın hesaplanmış verilerine genellikle nominal boyut denir. Genellikle bu değer tam milimetre olarak ifade edilir. İşleme sırasında fiilen elde edilen parçanın boyutuna gerçek boyut denir. Bu parametrenin arasında dalgalandığı değerlere genellikle limit denir. Bunlardan maksimum parametre en büyük boyut sınırıdır ve minimum parametre en küçüğüdür. Sapmalar, bir parçanın nominal ve sınır değeri arasındaki farktır. Çizimlerde, bu parametre genellikle sayısal biçimde nominal boyutta gösterilir (üst değer yukarıda, alt değer aşağıda belirtilmiştir).
Giriş örneği
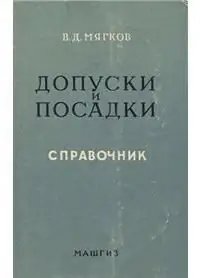
Çizim 40+0, 15-0, 1 değerini gösteriyorsa, bu, kısım 40 mm, en büyük sınır +0.15, en küçüğü -0.1. Nominal ve maksimum sınır değeri arasındaki farka üst sapma ve minimum - alt arasındaki fark denir. Buradan gerçek değerler kolayca belirlenir. Bu örnekten, en büyük sınır değerinin 40+0, 15=40.15 mm ve en küçüğünün: 40-0, 1=39.9 mm olacağı sonucu çıkar. En küçük ve en büyük limit boyutları arasındaki farka tolerans denir. Şu şekilde hesaplanır: 40, 15-39, 9=0.25mm.
Boşluklar ve sıkılık
Bir düşünelimtoleransların ve uyumların önemli olduğu özel bir örnek. 40-0, 1 boyutlarındaki bir mile sığdırmak için 40+0, 1 delikli bir parçaya ihtiyacımız olduğunu varsayalım. -0, 2. Tüm seçenekler için çapın delikten daha az olması koşulundan görülebilir, bu da böyle bir bağlantıyla mutlaka bir boşluk olacağı anlamına gelir. Böyle bir iniş genellikle hareketli olarak adlandırılır, çünkü şaft delikte serbestçe dönecektir. Parça boyutu 40+0, 2+0, 15 ise, her koşulda delik çapından daha büyük olacaktır. Bu durumda mil içeri bastırılmalıdır ve bağlantıda bir çakışma olacaktır.
Sonuçlar
Yukarıdaki örneklere dayanarak aşağıdaki sonuçlar çıkarılabilir:
- Boşluk, milin gerçek boyutları ile delik birinciden daha büyük olduğunda, delik arasındaki farktır. Bu bağlantı ile parçalar serbest dönüşe sahiptir.
- Ön yük genellikle deliğin gerçek boyutları ile mil arasındaki fark olarak adlandırılır, ikincisi birinciden daha büyük olduğunda. Bu bağlantı ile parçalar içeri bastırılır.
Uyar ve doğruluk sınıfları
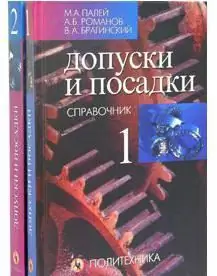
İnişler genellikle sabit (sıcak, basma, kolay basma, sağır, sıkı, yoğun, gergin) ve hareketli (kayma, koşma, hareket, kolay koşma, geniş koşma) olarak ayrılır. Makine mühendisliği ve enstrümantasyonda, toleransları ve inişleri düzenleyen belirli kurallar vardır. GOST, belirtilen boyutsal sapmaları kullanan montajların imalatında belirli doğruluk sınıfları sağlar. UygulamadanYol ve tarım makinelerinin detaylarının işleyişine zarar vermeden torna, ölçü aletleri ve otomobillere göre daha az hassasiyetle üretilebildiği bilinmektedir. Bu bağlamda, makine mühendisliğindeki toleranslar ve uyumlar on farklı doğruluk sınıfına sahiptir. Bunlardan en doğru olanı ilk beşidir: 1, 2, 2a, 3, 3a; sonraki ikisi orta doğrulukla ilgilidir: 4 ve 5; ve son üçü kaba: 7, 8 ve 9.
Parçanın hangi doğruluk sınıfında yapılması gerektiğini bulmak için çizimde, uyumu gösteren harfin yanına bu parametreyi gösteren bir sayı koyun. Örneğin, C4'ü işaretlemek, türün kaydığı anlamına gelir, sınıf 4; X3 - koşu tipi, 3. sınıf. İkinci sınıfın tüm inişleri için, en yaygın olduğu için dijital bir atama yapılmaz. Bu parametre hakkında detaylı bilgiyi iki ciltlik "Toleranslar ve Uyumlar" (Myagkov V. D., 1982 baskısı) referans kitabından alabilirsiniz.
Şaft ve delik sistemi
Tolerans ve geçmeler genellikle iki sistem olarak kabul edilir: delikler ve miller. Bunlardan ilki, aynı doğruluk derecesine ve sınıfa sahip tüm tiplerin aynı nominal çapa atıfta bulunmasıyla karakterize edilir. Delikler, sabit limit sapma değerlerine sahiptir. Böyle bir sistemde, şaftın maksimum sapmasının değiştirilmesi sonucunda çeşitli inişler elde edilir.
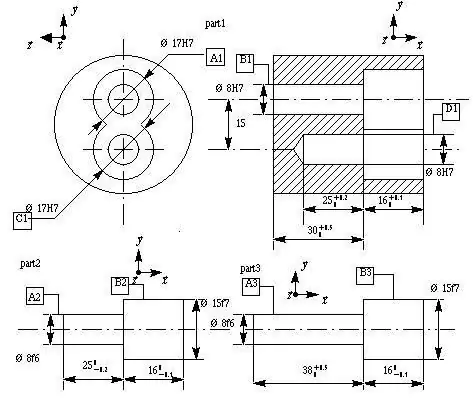
İkincisi, aynı doğruluk derecesine ve sınıfa sahip tüm tiplerin aynı nominal çapa atıfta bulunmasıyla karakterize edilir. Milin sabit limit değerleri vardırsapmalar. Deliklerin maksimum sapma değerlerinin değiştirilmesi sonucunda çeşitli inişler yapılır. Delik sisteminin çizimlerinde, A harfini ve şaftı - B harfini belirtmek gelenekseldir. Harfin yanına doğruluk sınıfının işareti yerleştirilir.
Sembol örnekleri
Çizimde "30A3" belirtilirse, söz konusu parçanın üçüncü doğruluk sınıfında bir delik sistemi ile işlenmesi gerektiği anlamına gelir, "30A" belirtilirse, aynı sistemin kullanılması anlamına gelir, ancak ikinci sınıf. Tolerans ve uyum mil prensibine göre yapılırsa istenilen tip nominal ölçüde belirtilir. Örneğin, "30B3" adlı bir parça, üçüncü doğruluk sınıfının şaft sisteminin işlenmesine karşılık gelir.
M. A. Paley (“Toleranslar ve Uyumlar”) adlı kitabında, makine mühendisliğinde bir şafttan daha sık bir delik ilkesinin kullanıldığını açıklıyor. Bunun nedeni daha az ekipman ve alet gerektirmesidir. Örneğin, bu sisteme göre belirli bir nominal çaptaki bir deliği işlemek için, bu sınıftaki tüm yuvalar için sadece bir rayba ve çapı değiştirmek için bir limit tapası gereklidir. Bir şaft sistemiyle, her birinin aynı sınıfa girmesini sağlamak için ayrı bir rayba ve ayrı bir tapa gerekir.
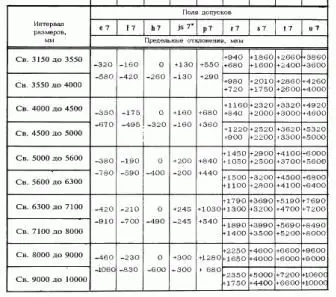
Toleranslar ve uyumlar: sapma tablosu
Doğruluk sınıflarını belirlemek ve seçmek için özel referans literatürü kullanmak gelenekseldir. Bu nedenle, toleranslar ve uyumlar (bu makalede bir örnek içeren bir tablo verilmiştir) kural olarak çok küçük değerlerdir. İçinfazladan sıfır yazmamak için literatürde mikron (milimetrenin binde biri) olarak belirtilirler. Bir mikron 0,001 mm'ye karşılık gelir. Genellikle, nominal çaplar böyle bir tablonun ilk sütununda gösterilir ve ikincisinde deliğin sapmaları gösterilir. Grafiklerin geri kalanı, karşılık gelen sapmaları ile farklı boyutlarda inişler verir. Böyle bir değerin yanındaki artı işareti nominal boyuta eklenmesi gerektiğini, eksi işareti ise çıkarılması gerektiğini belirtir.
İplikler
Dişli bağlantıların toleransı ve oturması, dişlerin yalnızca profilin yanlarında birleştirildiği gerçeğini hesaba katmalıdır, yalnızca buhar geçirmez tipler bir istisna olabilir. Bu nedenle, sapmaların doğasını belirleyen ana parametre ortalama çaptır. Dış ve iç çaplar için tolerans ve geçmeler, ipliğin olukları ve üst kısımları boyunca sıkışma olasılığını tamamen ortadan kaldıracak şekilde ayarlanmıştır. Dış boyutu küçültme ve iç boyutu artırma hataları makyaj işlemini etkilemeyecektir. Ancak diş hatvesi ve profil açısındaki sapmalar, bağlantı elemanının sıkışmasına neden olur.
Boşluk diş toleransları
Tolerans ve boşluk uyumu en yaygın olanlarıdır. Bu tür bağlantılarda, ortalama çapın nominal değeri, somun dişinin en büyük ortalama değerine eşittir. Sapmalar genellikle diş eksenine dik olan profil çizgisinden sayılır. Bu, GOST 16093-81 tarafından belirlenir. Somun ve cıvataların diş çapı toleransları, belirtilen doğruluk derecesine göre atanır (bir sayı ile gösterilir). Kabul edilmişbu parametre için bir sonraki değer dizisi: q1=4, 6, 8; d2=4, 6, 7, 8; D1=4, 6, 7, 8; D2=4, 5, 6, 7. Onlar için toleranslar ayarlanmamıştır. Diş çapı alanlarının nominal profil değerine göre yerleştirilmesi, ana sapmaların belirlenmesine yardımcı olur: cıvataların dış değerleri için üst olanlar ve somunların iç değerleri için alt olanlar. Bu parametreler doğrudan doğruluk ve bağlantı adımına bağlıdır.
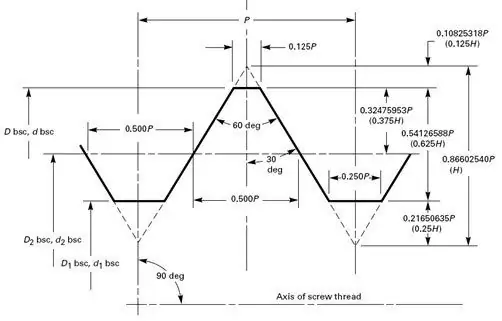
Toleranslar, uyumlar ve teknik ölçümler
Belirtilen parametrelere sahip parçaların ve mekanizmaların üretimi ve işlenmesi için tornacının çeşitli ölçüm aletleri kullanması gerekir. Genellikle kaba ölçüler ve ürünlerin ölçülerinin kontrolü için cetvel, kumpas ve iç mastarlar kullanılır. Daha doğru ölçümler için - kumpaslar, mikrometreler, göstergeler vb. Herkes cetvelin ne olduğunu bilir, bu yüzden üzerinde durmayacağız.
Pergel, iş parçalarının dış boyutlarını ölçmek için basit bir araçtır. Aynı eksen üzerinde sabitlenmiş bir çift döner kavisli bacaktan oluşur. Yaylı tip kumpas da vardır, vida ve somun ile istenilen ölçüye ayarlanır. Böyle bir araç, belirtilen değeri koruduğu için basit bir araçtan biraz daha uygundur.
Pergel, dahili ölçümler yapmak için tasarlanmıştır. Düzenli ve yaylı bir türü vardır. Bu aletin cihazı bir kumpasa benzer. Cihaz doğruluğu 0,25 mm'dir.
Bir kumpas daha hassas bir cihazdır. Hem dış hem de iç yüzeyleri ölçebilirler.işlenmiş parçalar Torna tezgahı üzerinde çalışırken, bir oluğun veya çıkıntının derinliğini ölçmek için bir kumpas kullanır. Bu ölçüm aleti, dereceli ve çeneli bir şafttan ve ikinci bir çift çeneli bir çerçeveden oluşur. Bir vida yardımıyla çerçeve gerekli pozisyonda çubuğa sabitlenir. Ölçüm doğruluğu 0,02 mm'dir.
Derinlik ölçer - bu cihaz, olukların ve alt oyukların derinliğini ölçmek için tasarlanmıştır. Ek olarak, alet, şaftın uzunluğu boyunca çıkıntıların doğru konumunu belirlemenizi sağlar. Bu cihazın cihazı kumpasa benzer.
Mikrometreler, iş parçasının çapını, kalınlığını ve uzunluğunu doğru bir şekilde belirlemek için kullanılır. 0,01 mm hassasiyetle okumalar verirler. Ölçülen nesne mikrometre vidası ile sabit topuk arasına yerleştirilir, tambur döndürülerek ayar yapılır.
İç ölçüler, iç yüzeylerin doğru ölçümleri için kullanılır. Sabit ve kayar cihazları vardır. Bu aletler, ölçüm bilyeli uçlu çubuklardır. Aralarındaki mesafe, belirlenen deliğin çapına karşılık gelir. İç mastar için ölçüm limitleri 54-63 mm'dir, ek bir kafa ile 1500 mm'ye kadar çaplar belirlenebilir.
Önerilen:
Makine mühendisliğinde teknolojik süreçler. Otomatik proses kontrol sistemleri
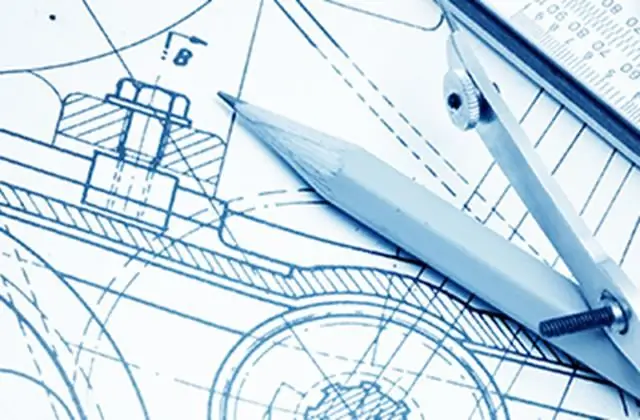
Teknolojik süreç, herhangi bir üretim işleminin temelidir. Eylemi, üretilen ürünün şeklini, boyutunu ve özelliklerini değiştirmeyi amaçlayan belirli bir sırayla gerçekleştirilen bir dizi prosedürü içerir. Teknolojik süreçlerin ana örnekleri mekanik, termal, sıkıştırma işlemlerinin yanı sıra montaj, paketleme, basınç işlemi ve çok daha fazlasıdır
Endüstriyel makine ve mekanizma üretimi

Herhangi bir eyalette endüstriyel üretim iki gruba ayrılır. İlk grup - koşullu olarak A endeksi tarafından belirlenir - üretim araçlarının üretimine odaklanır. Bu formülasyon tüm ekonomi ders kitaplarında verilmektedir. Bu kavramı bir örnekle genişletirsek, o zaman bu sektörde aynı sanayi işletmelerinde kullanılan makineler, aletler ve diğer ekipmanlar üretilmektedir
Potasyum sülfat - klora tolerans göstermeyen bitkiler için gübre

Bugün, potasyum sülfat bahçecilikte bitkileri gübrelemek için aktif olarak kullanılmaktadır. Potasyum sülfat, tarımsal faaliyetlerde en çok yönlü ve yaygın olarak kullanılan maddedir
Makine mühendisliğinde kullanılan diş türleri
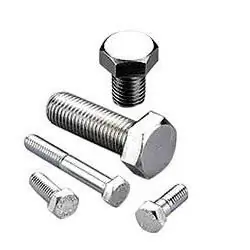
İplik, konik veya silindirik bir yüzeye uygulanan sabit aralıklı süslü bir spiraldir. İki tip bağlantı elemanını bağlamak için ana unsurdur. Bugüne kadar, genel makine yapımı uygulamaları için ana dış ve iç dişler metriktir
Uyum: nedir? Tanım, açıklama

Batı'nın ülkemize yönelik yaptırım politikasının zor koşullarında, uyum denetimi bankacılık sektörü yönetim sisteminin önemli araçlarından biri haline geliyor. Uyum nedir? Rus şirketlerinde uyum prosedürlerinden bahsederken yabancı iş ortakları nelere dikkat ediyor? Ve ne gibi faydalar sağlıyorlar? anlamaya çalışalım