2025 Yazar: Howard Calhoun | [email protected]. Son düzenleme: 2025-01-24 13:27
Metal, tüm modern uygarlığın temelidir. Bir yıl içinde, modern insanlık tek başına o kadar çok demir çıkarır ve işler ki, tüm dünya onu en az birkaç yüzyıl önce seçecektir. Ve bu ihtiyaç tamamen haklı, çünkü inşaat tek başına inanılmaz miktarda çelik alıyor. Şaşırtıcı olmayan bir şekilde, bu koşullar altında metal dökümü sürekli olarak geliştirilmektedir.
Biraz tarih
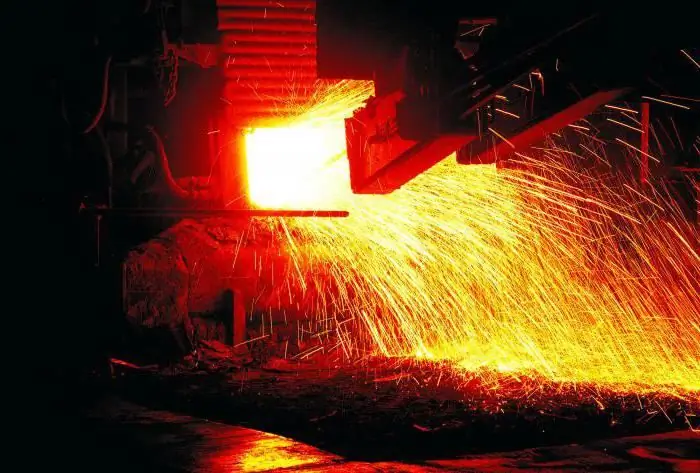
Demirin en önemli özelliğinin alması, katılaşması, kendisine "önerilen" şeklin eski zamanlarda bir kişi tarafından fark edilmesidir. Bugün neredeyse tüm bilim adamları, insanın metalle ilk tanışmasının meteorlar sayesinde gerçekleştiğini varsayıyor. Göktaşı demiri eriyebilirdi ve işlenmesi kolaydı, bu nedenle dökümün temelleri uzun zaman önce bazı yeni ortaya çıkan uygarlıklar tarafından incelendi.
Ülkemizde metal döküm yüzyıllardır saygın ve onurlu bir iş olmuştur, insanlar bu zanaata her zaman büyük saygı duymuşlardır. Rus ustalarının döküm becerisinin başyapıtları olan "Çar Topu" ve "Çar Çanı", biri hiç çalmasa ve ikincisi ateş etmese bile, yaygın olarak bilinir. Büyük Peter döneminde Ural tekerleriordu için güvenilir silah tedarikçisi olarak özel bir ün kazandı. Ancak, şu anda bile bu unvanı oldukça haklı olarak taşıyorlar. Ana metal döküm türlerine bakmadan önce, hammaddelerin gerekli özellikleri hakkında birkaç söz söylemek gerekir.
Döküm için metal ne olmalıdır
Dökümde kullanılacak metalin en önemli özelliği akışkanlığıdır. Erimiş haldeki alaşım, en küçük girintilerini doldururken bir potadan diğerine mümkün olduğunca kolay akmalıdır. Akışkanlık ne kadar yüksek olursa, bitmiş üründe duvarlar o kadar ince yapılabilir. Kötü yayılan metal ile çok daha zordur. Normal şartlar altında formdaki tüm boşlukları doldurduğundan çok daha erken kapmayı başarıyor. Metal alaşımları dökerken sanayicilerin karşılaştığı zorluk budur.
Dökme demirin dökümhanenin favori malzemesi haline gelmesi şaşırtıcı değil. Bunun nedeni, bu alaşımın mükemmel akışkanlığa sahip olması ve bu da onunla çalışmayı nispeten kolay hale getirmesidir. Çelik bu kadar akışkan olmaktan uzaktır ve bu nedenle kalıbı tamamen doldurmak için (boşluklar ve boşluklar olmaması için) çeşitli numaralara başvurmak gerekir.
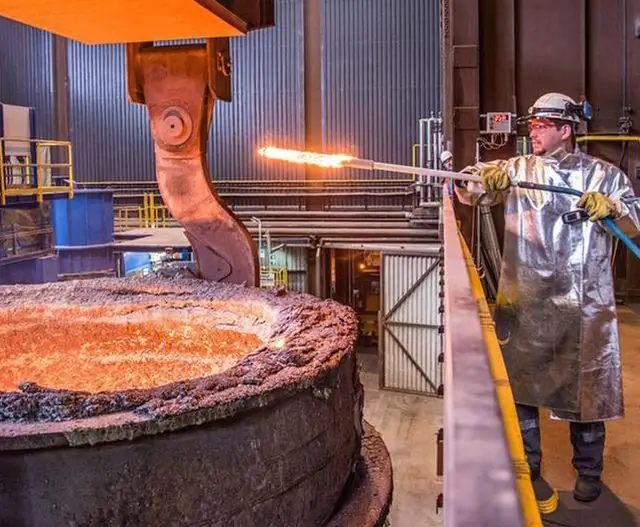
En basit durumda, evde metal dökümü gerektiğinde, hammaddeler eritilir ve küçük porsiyonlarda suya dökülür: özellikle bu şekilde, özellikle balık avı için platinler yapabilirsiniz. Ancak bu yöntem, silah endüstrisinde bile nispeten yaygın olarak kullanılmaktadır! Ana hatlarıyla bir soğutma kulesine benzeyen özel bir kulenin tepesinden, erimişmetal. Yapının yüksekliği, zaten soğumuş olan mükemmel şekilde oluşturulmuş bir damlacık zemine ulaşacak şekildedir. Endüstriyel ölçekte atış bu şekilde üretilir.
Toprak döküm yöntemi
En basit ve en eski yöntem, metali toprağa dökmektir. Ancak “basitliği” nispeten şartlı bir kavramdır, çünkü bu çalışma son derece özenli bir hazırlık gerektirir. Bu ne anlama geliyor?
Öncelikle maket dükkanında geleceğin dökümünün tam boyutlu ve en detaylı modeli yapılır. Ayrıca metal soğuduğunda çökeceği için boyutu elde edilmesi gereken üründen biraz daha büyük olmalıdır. Kural olarak, model iki yarıdan ayrılabilir yapılır.
Bu yapıldıktan sonra özel kalıp kumu hazırlanır. Gelecekteki ürünün iç boşlukları ve boşlukları olması gerekiyorsa, çubukların yanı sıra ek bir kalıplama bileşiği hazırlamak da gerekli olacaktır. Bitmiş kısımda “boş” olan alanları geçici olarak doldurmaları gerekir. Evde metal dökümü yapmakla ilgileniyorsanız, bu gerçeği aklınızda bulundurun, aksi takdirde zaten doldurulmuş bir şişe basınçla kolayca parçalanabilir ve bunun sonuçları en üzücü olabilir.
Döküm kumları neyden yapılır?
Temel, çeşitli derecelerde kum ve killerin yanı sıra bağlayıcılardır. Rollerini doğal ve sentetik yağlar, kurutma yağı, reçine, reçine ve hatta katran oynayabilir.
Sıradan görevi kalıp yapmak olan kalıpçıların zamanı geliyor. açıklarsandaha kolay, şu şekilde yapılır: bir tahta kutu alınır, kalıbın yarısı içine yerleştirilir (ayrıca çıkarılabilir) ve modelin duvarları ile kalıp arasındaki boşluklar bir kalıp bileşimi ile tıkanır.
Aynı şey ikinci yarı ile yapılır ve her iki parçayı da pimlerle sabitleyin. Döküldüğünde üstte olacak formun o kısmına iki özel koninin yerleştirildiğine dikkat etmek önemlidir. Bunlardan biri erimiş metali dökmek için kullanılır, ikincisi - genişleyen gazlardan çıkmak için.
Hazırlık aşamasının sonu
Ve şimdi operasyonun belki de en önemli kısmına gelme zamanı. Şişeler, kumun bütünlüğünün ihlalini önlemeye çalışarak çok dikkatli bir şekilde ayrılır. Bundan sonra, gelecek bölümün iki net ve ayrıntılı izi yerde kalıyor. Bundan sonra, özel bir boya ile kaplanır. Bu, erimiş metalin kum zemin ile doğrudan temas etmemesi için yapılır. Metal döküm teknolojisi buna izin vermemelidir, aksi takdirde bitmiş ürünün kalitesi önemli ölçüde bozulabilir.
Gerekirse, aynı zamanda eriyiği dökmek için gerekli olan ek bir geçit geçişi kesilir. Şişeler tekrar katlanır ve mümkün olduğunca sıkı bir şekilde bağlanır. Kum biraz kuruduktan sonra döküme başlayabilirsiniz.
Yayınlamaya başlayın
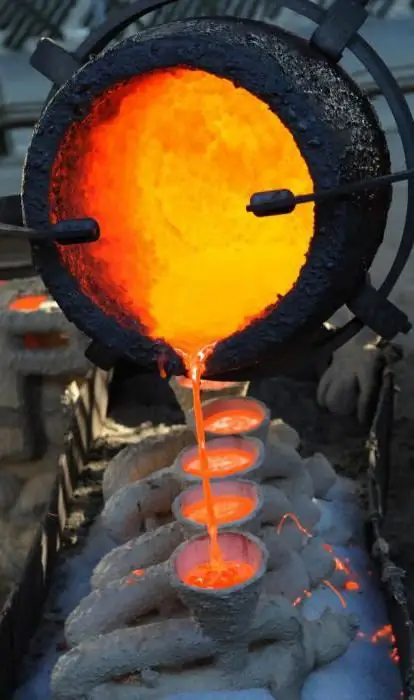
Önce kupolalarda yani özel fırınlarda, dökme demir boşluklar eritilir. Çelik döküm yapılması gerekiyorsa, hammaddeler yüksek fırınlarda, açık ocaklarda, inverter ve diğer fırınlarda eritilir. Getirmek içindemir dışı metallerin erime durumu, özel eritme cihazları kullanın.
Her şey, yayınlamaya başlayabilirsiniz. Sadece bir form varsa, eriyik ayrı ayrı bir kepçe ile içine dökülür. Diğer durumlarda, kural olarak, bir konveyör düzenlenir: ya boşlukları olan bir bant kepçenin altına girer ya da kepçe şişe sıralarının üzerinden geçer. Her şey yalnızca üretim organizasyonuna bağlıdır. Zamanı geldiğinde ve metal soğuduğunda kalıptan çıkarılır. Prensip olarak, bu yöntem evde metal dökümün gerekli olduğu durumlarda (örneğin bir dövme için) idealdir. Bu şartlar altında daha mükemmel bir şey zaten elde edilemez.
Kumlama veya taşlama makineleri, bitmiş üründeki kireci ve yapışan kalıp kumunu çıkarır. Bu arada, bu yöntem Büyük Vatanseverlik Savaşı sırasında tank üretiminde aktif olarak kullanıldı. Dökme kuleler bu şekilde üretildi ve bu işlemin basitliği ve üretilebilirliği, cephenin çok ihtiyaç duyduğu çok sayıda askeri aracın üretilmesini mümkün kıldı. Başka ne tür metal döküm var?
Kalıp döküm
Ama artık döküm ürünlerin üretimi için çok daha gelişmiş ve teknolojik olarak gelişmiş yöntemler kullanıyorlar. Örneğin, soğuk bir kalıpta metal döküm. Prensip olarak, bu yöntem birçok açıdan yukarıda açıklanana benzer, çünkü bu durumda döküm kalıpları da kullanılır. Sadece aynı zamanda metaldirler, bu da büyük ölçekli üretim sürecini büyük ölçüde basitleştirir.
Böylece, koniler ve çubuklar iki yarıya yerleştirilir (metal dökmek ve boşluklar oluşturmak için) vesonra bunları birbirine sıkıca sabitleyin. Her şey, işe başlayabilirsin. Bu yöntemin özelliği, burada erimiş metalin son derece hızlı bir şekilde katılaşması, kalıpların zorla soğutulma olasılığının olması ve bu nedenle serbest bırakma işleminin çok daha hızlı olmasıdır. Tek bir kalıpla, kalıpları ve kumları ayrı ayrı hazırlamak için çok fazla zaman harcamadan yüzlerce, hatta binlerce döküm alabilirsiniz.
Yöntemin bazı dezavantajları
Bu döküm yönteminin dezavantajı, yalnızca erimiş halde artan akışkanlık ile karakterize edilen metal türlerinin buna uygun olmasıdır. Örneğin, çelik için sadece basınçlı döküm uygundur (aşağıda bunun hakkında), çünkü bu malzeme hiç iyi akışkanlığa sahip değildir. Sıkıştırılmış havanın etkisi altında, en "sünek" çelik kaliteleri bile gerekli şekli çok daha iyi alır. Kötü olan şey, sıradan bir soğuk kalıbın bu tür aşırı üretim koşullarına dayanamaması ve parçalanmasıdır. Bu nedenle aşağıda tartışacağımız özel bir üretim yöntemi kullanmalısınız.
Enjeksiyon kalıplama
Metallerin basınçlı dökümü -basınç altında- nasıl yapılır? Yukarıda bazı hususları zaten ele aldık, ancak yine de bu konuyu daha ayrıntılı olarak açıklamak gerekiyor. Her şey oldukça basit. İlk olarak, çok aşamalı, karmaşık bir iç şekil olabilen kaliteli çelik kalitelerinden yapılmış bir döküm kalıbı gereklidir. İkinci olarak, yedi ila yedi yüz MP arasında dağıtım yapabilen pompalama ekipmanına ihtiyacımız var.
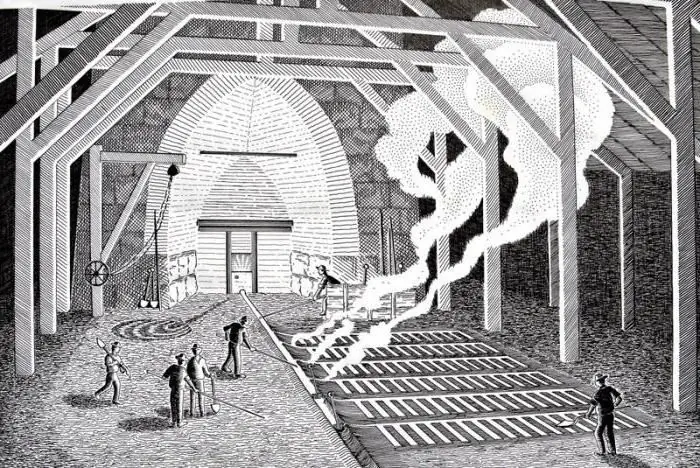
Ana avantajbu eritme yöntemi yüksek bir verimliliktir. Başka neler enjeksiyon kalıplama sağlar? Bu durumda çok daha az metal kullanılır ve bitmiş ürünün yüzey kalitesi çok iyidir. İkinci durum, karmaşık ve oldukça kasvetli bir temizleme ve öğütme prosedürünün reddedildiğini ima eder. Bitmiş ürünler ve parçalar üretmek için bu üretim yöntemi için en iyi malzemeler hangileridir?
En yaygın kullanılan alaşımlar alüminyum, çinko, bakır ve kalay-kurşun (demir dışı metallerin dökümü) bazlıdır. Erime sıcaklıkları nispeten düşüktür ve bu nedenle tüm sürecin çok yüksek bir üretilebilirliği elde edilir. Ek olarak, bu hammadde soğuduktan sonra nispeten küçük bir tortuya sahiptir. Bu da modern teknolojinin üretiminde son derece önemli olan çok küçük toleranslarla parçaların üretilmesinin mümkün olduğu anlamına geliyor.
Bu yöntemin karmaşıklığı, bitmiş ürünler kalıplardan ayrıldığında zarar görmeleridir. Ek olarak, bu yöntem yalnızca nispeten küçük duvar kalınlığına sahip parçaların üretimi için uygundur. Gerçek şu ki, kalın bir metal tabakası son derece düzensiz bir şekilde sertleşecek ve bu da kabukların ve oyukların oluşumunu önceden belirleyecektir.
Basınçlı döküm için kurulum çeşitleri
Metal ürünlerin dökümünün bu yönteminde kullanılan tüm makineler iki büyük gruba ayrılır: sıcak ve soğuk döküm odalı. "Sıcak" çeşitlilik çoğunlukla sadece çinko bazlı alaşımlar için kullanılabilir. Bu durumda, döküm odasının kendisi sıcak metale daldırılır. Baskı altındahava veya özel bir piston, döküm boşluğuna akar.
Kural olarak, güçlü bir enjeksiyon kuvveti gerekli değildir, 35-70 MPa'ya kadar basınç yeterlidir. Bu durumda, metal döküm için kalıplar, ürünün nihai maliyeti üzerinde en olumlu etkiye sahip olan çok daha basit ve daha ucuz olabilir. Soğuk döküm kalıplarında, erimiş metalin özellikle yüksek basınç altında döküm odasının derinliklerine "sürülmesi" gerekir. Aynı zamanda 700 MPa'ya ulaşabilir.
Enjeksiyonla kalıplanmış parçalar nerede kullanılır?
Onlar her yerdeler. Telefonlarda, bilgisayarlarda, kameralarda, çamaşır makinelerinde her yerde bu yöntemle elde edilen detaylar var. Özellikle havacılık ve hatta uzay endüstrileriyle doğrudan ilgili olanlar da dahil olmak üzere makine mühendisliği tarafından yaygın olarak kullanılmaktadır. Dökme parçaların kütlesi birkaç gramdan 50 kilograma (ve hatta daha yüksek) kadar değişebilir. Döküm yoluyla metallerin başka "işlenmesi" kullanılabilir mi? Evet ve daha birçok yol var.
Kayıp mum döküm
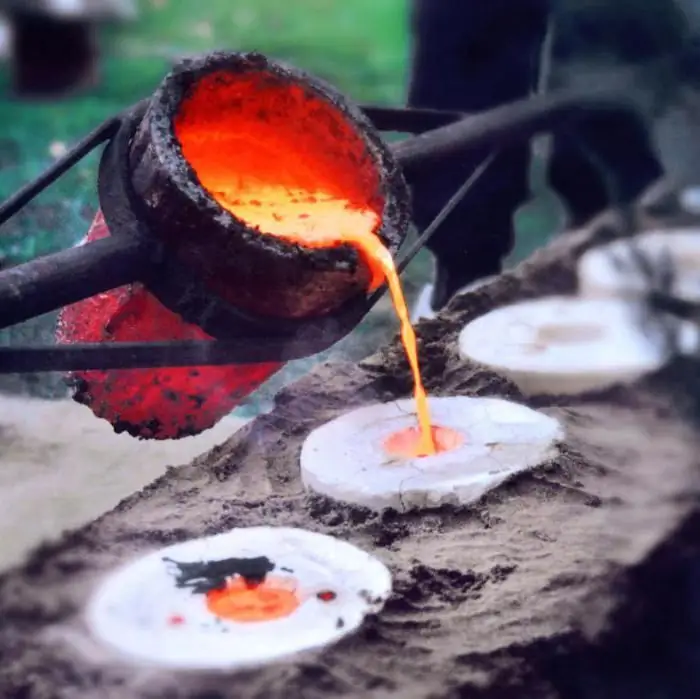
Düşündüğümüz ilk durumda olduğu gibi, eski zamanlardan beri insanlık, erimiş metali önceden hazırlanmış parafin veya balmumundan yapılmış bir modele dökme yöntemini biliyor. Şişeye basitçe yerleştirilir ve boşluklar kalıp kumu ile doldurulur. Eriyik mumu çözer ve ideal olarak birincil iş parçasının tüm hacmini doldurur. Bu yöntem iyidir çünkü modelin şişeden çıkarılmasına gerek yoktur. Ek olarak, bu döküm işlemi ile sadece mükemmel kalitede parçalar elde etmek mümkündür.metallerin otomatikleştirilmesi nispeten kolaydır.
Kabuk döküm
Döküm nispeten basitse ve bitmiş üründen "boşluk" mukavemeti gerekli değilse, kabuk kalıplara döküm yöntemi kullanılabilir. Çok eski zamanlardan beri yapılmışlardır ve temel olarak ince kuvars kumu ve reçinesi kullanılmıştır. Bugün, elbette, ikincisi olarak çeşitli sentetik bileşikler kullanılmaktadır.
Ardından, iki yarıdan oluşan katlanabilir metal modeller alınır ve yaklaşık 300 santigrat dereceye kadar ısıtılan bir yüzeye yerleştirilir. Daha sonra kalıplama karışımı (kum ve kuru reçineden) metal modellerin yüzeyini tamamen kaplayacak şekilde aynı yere dökülür. Isının etkisi altında reçine erir ve kumun kalınlığında oldukça güçlü bir “şişe” belirir.
Her şey biraz soğuyunca metal külçeler çıkarılabilir ve kum “kavurma” için fırına gönderilebilir. Bundan sonra, yeterince güçlü formlar elde edilir: iki yarısını birleştirerek içlerine erimiş metal dökülebilir. Başka hangi metal döküm yöntemleri var?
Santrifüj döküm
Bu durumda, eriyik, yatay veya dikey bir çıkıntıda çok yüksek bir hızda dönen özel bir forma dökülür. Eşit olarak uygulanan güçlü merkezkaç kuvvetlerinin etkisinin bir sonucu olarak, metal, kalıbın tüm boşluklarına eşit şekilde akar ve böylece yüksek kalitede bitmiş ürün elde edilir. Bu döküm yöntemi, çeşitli boru türlerinin üretimi için idealdir. Çok daha düzgün bir kalınlık oluşturmaya izin verir"statik" yöntemlerle elde edilmesi son derece zor olan duvarlar.
Elektro-cüruf döküm
Metalleri dökmenin haklı olarak modern olarak adlandırılabilecek herhangi bir yolu var mı? Elektroslag döküm. Bu durumda önce güçlü elektrik ark deşarjları ile önceden hazırlanmış ham maddeye etki edilerek sıvı metal elde edilir. Arksız yöntem, cürufun biriktirdiği ısıdan demir eritildiğinde de kullanılabilir. Ama sonuncusu güçlü deşarjlardan etkilenir.
Bundan sonra, tüm süreç boyunca hiç hava ile temas etmeyen sıvı metal, "kombinasyon halinde" aynı zamanda bir döküm kalıbı olan kristalizasyon odasına girer. Bu yöntem, imalatı için birçok koşulun gözetilmesi gerekmeyen nispeten basit ve masif dökümler için kullanılır.
Vakum doldurma
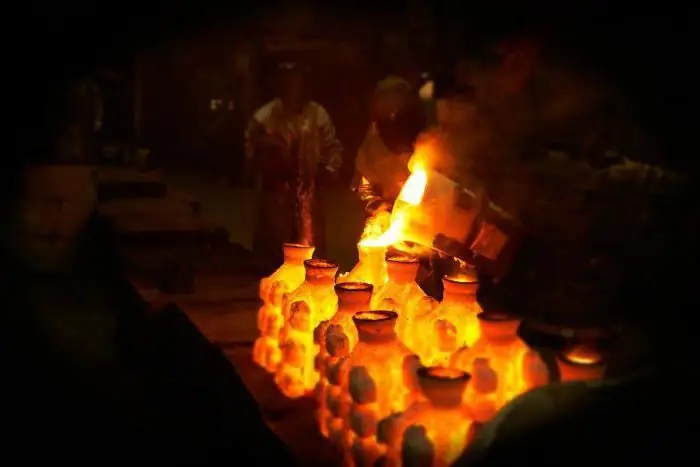
Yalnızca altın, titanyum, paslanmaz çelik gibi "yüksek kaliteli" malzemeler için geçerlidir. Bu durumda metal vakum koşullarında eritilir ve daha sonra hızlı bir şekilde (aynı koşullar altında) kalıplara dağıtılır. Yöntem, kullanıldığında, mevcut gazların miktarı minimum olduğundan, üründe hava boşlukları ve boşlukların oluşumunun pratik olarak hariç tutulması bakımından iyidir. Bu durumda dökümlerin ağırlığının yüz veya iki kilogramı aşamayacağını hatırlamak önemlidir.
Daha büyük parçalar elde etmek mümkün mü?
Evet, böyle bir teknoloji var. Ancak sadece yüz ton çeliğin aynı anda işlendiği durumlarda kullanılabilir.ve dahası. Önce metal vakum koşullarında eritilir ve daha sonra kalıplara değil, boşluklarına giren havadan da korunan özel kalıplama potalarına dökülür.
Bundan sonra, bitmiş eriyik, havanın daha önce bir pompa ile dışarı pompalandığı kalıplara dağıtılabilir. Böyle bir teknolojik işlem sonucunda elde edilen çelik oldukça pahalıdır. En yüksek kalitede boşluklar ve parçalar elde etmek gerektiğinde, aynı dökümün bazı türlerinin yanı sıra dövme için kullanılır.
Gazlaştırılmış (yanmış) kalıplara döküm
Döküm kalitesi ve basitliği açısından bu yöntem en karlı yöntemlerden biridir ve bu nedenle modern endüstride giderek daha yaygın olarak kullanılmaktadır. Üretimi yıldan yıla artan bu tür metal döküm, özellikle PRC ve ABD'de popülerdir, çünkü bu iki ülkenin endüstriyel üsleri yüksek kaliteli çeliğe en büyük ihtiyaç ile ayırt edilir. Bu yöntemin avantajı, ağırlık ve boyut kısıtlaması olmaksızın döküm üretimine olanak sağlamasıdır.
Birçok yönden, bu yöntem yukarıda açıklananlara benzer: örneğin, bu durumda, birincil model mum veya hamuru değil, şimdi yaygın olan köpükten kullanılır. Bu malzemenin kendine has özellikleri olduğundan, bağlayıcı kum karışımı, yaklaşık 50 kPa'lık bir basınç altında şişeye doldurulur. Çoğu zaman, bu yöntem 100 gramdan iki tona kadar olan parçaların yapılmasının gerekli olduğu durumlarda uygulanır.
Ancak, bazı katı kısıtlamalarınboyut ayrıntıları hayır. Böylece, bu döküm yöntemini kullanarak, hiçbir zaman “mütevazı” boyutta olmayan gemi motorları için bileşenler bile üretilebilir. Her bir ton metal hammaddesi için aşağıdaki miktarda ek malzeme tüketilir:
- Kum kuvars ince - 50 kg.
- Özel yapışmaz kaplama - 25 kg.
- Tanecikli polistiren köpük - 6 kg.
- Yoğun polietilen film - 10 metrekare m.
Tüm kalıplama kumları, herhangi bir ek katkı maddesi ve katkı maddesi içermeyen saf kuvars kumudur. Yaklaşık %95-97 yeniden kullanılabilir olabilir, bu da ekonomiyi büyük ölçüde iyileştirir ve işlemin maliyetini düşürür.
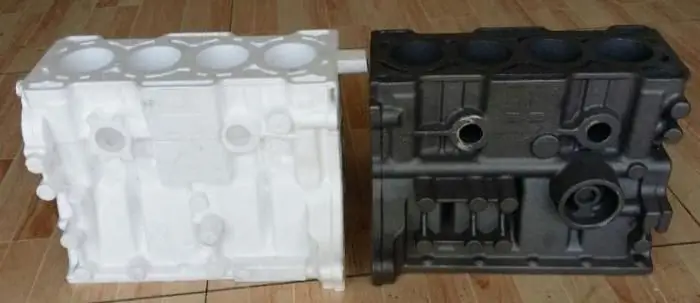
Böylece metal döküm (işlemin fiziği tarafımızdan kısmen değerlendirildi) “çok yönlü” bir fenomendir, çünkü bugün birçok yeni yöntem vardır. Aynı zamanda, modern endüstri, birkaç bin yıl önce kullanılan yöntemleri bir şekilde mevcut gerçeklere uyarlayarak uyguluyor.
Önerilen:
Silikon kalıpta döküm: ekipman. Silikon kalıplarda vakumlu döküm
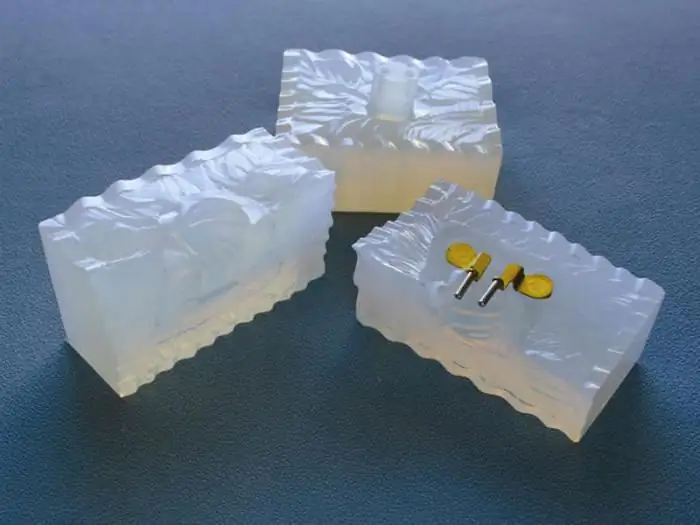
Az sayıda plastik boşluk üretimi için, çoğunlukla silikon kalıplara vakumlu döküm kullanılır. Bu yöntem oldukça ekonomiktir (metal kalıp yapmak daha fazla zaman ve para gerektirir). Ayrıca silikon kalıplar tekrar tekrar kullanılır ve bu da üretim maliyetini önemli ölçüde az altır
Döküm kalıbı: özellikler, teknoloji, türler
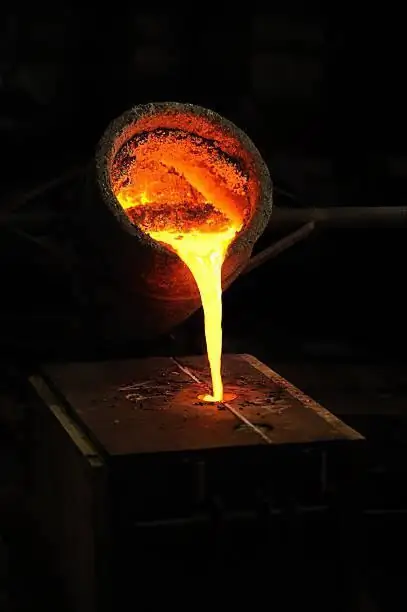
Sektördeki en önemli süreçlerden biri çeşitli parçaların, hammaddelerin ve diğer şeylerin dökümüdür. Bununla birlikte, istenen şeyi başarılı bir şekilde üretebilmek için, nihai sonucu büyük ölçüde belirleyen bir kalıp yapmak gerekir
Kuyu geliştirme: yöntemler, süreç tanımı, güvenlik. iyi onarım
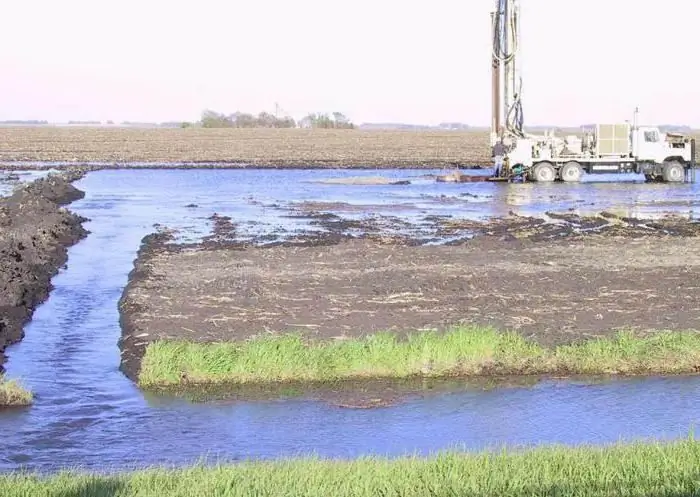
Makale, kuyuların geliştirilmesine ayrılmıştır. Bu etkinliğin uygulanmasının yöntemleri, özellikleri ve nüansları ile güvenlik önlemleri ve onarım çalışmaları dikkate alınır
İşleme için yağın hazırlanması: ana süreç, yöntemler ve teknolojiler
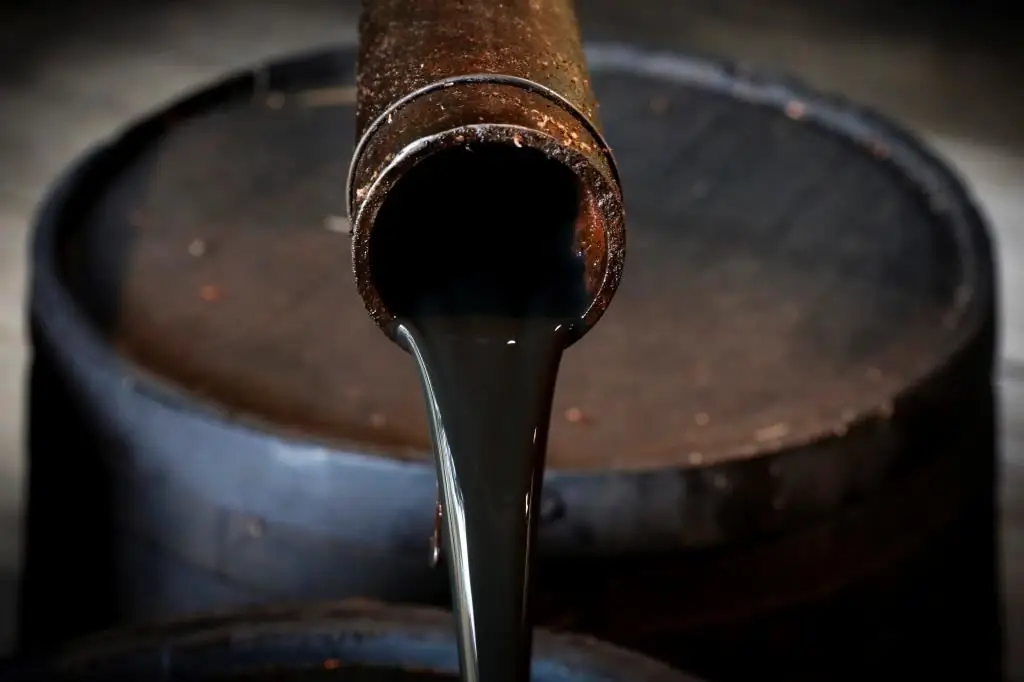
Petrol sahalarının kuyularından üretilenler saf haliyle hammadde değildir. Gerekli tüketici niteliklerine sahip bir ticari ürünün alınmasıyla ana işlemenin üretim sürecinin aşamalarından önce, gelecekteki enerji kaynağı birkaç teknolojik işleme aşamasından geçer. Bu süreçlerin uygulanması ihtiyacı, ham petrolün ilk kirlenmesinden kaynaklanmaktadır
Sfero döküm: özellikler, işaretleme ve kapsam
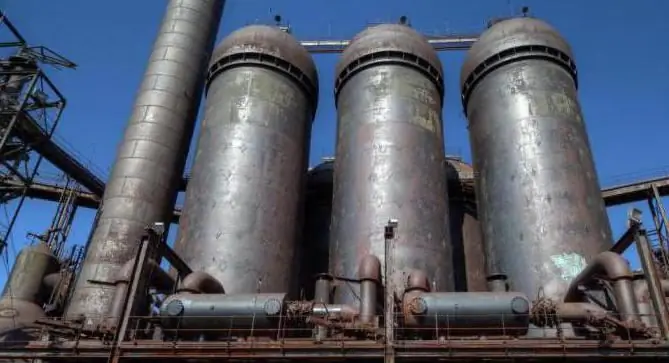
Dökme demir, karbon içeriği C %2,14 ile %6,67 arasında değişen sert, korozyona dayanıklı, ancak kırılgan bir demir-karbon alaşımıdır. Karakteristik eksikliklerin varlığına rağmen, çeşitli türleri, özellikleri ve uygulamaları vardır. Sfero döküm yaygın olarak kullanılmaktadır