2025 Yazar: Howard Calhoun | [email protected]. Son düzenleme: 2025-01-24 13:27
Kalıp, boyut, pürüzlülük, yapı ve ürün özellikleri için tüm gereksinimleri karşılayan bir döküm elde etmek için erimiş metali işlemek için kullanılan en önemli unsurdur.
Kabuk Türleri
Şu anda, temelde farklı iki tür form vardır. Aralarındaki fark, kalıbın üretim teknolojisindedir. Süspansiyon uygulanmasının yanı sıra daha sonraki kaplama ve kurutma işlemleri kullanılarak üretilen çok katmanlı türleri vardır.
İkinci tip iki katmanlıdır. Bu formların üretimi elektroforetik yöntemle yapılmaktadır. Kalıp kabuğu için temel gereksinimler, sıcak, sert, gaz geçirgen, doğru, pürüzsüz bir temas yüzeyi ve ayrıca tek parçadır.

Çok katmanlı kabuklar
Çok katmanlı bir kabuk elde etme süreci şu şekilde ilerler: kalıbın yüzeyi bir süspansiyon ile ıslatılır. Bu işlem, formun gerekli maddeye daldırılmasıyla gerçekleştirilir. Bloğu süspansiyondan çıkardıktan sonra, hemen granül bir madde ile serpilir. Bulamaç, konfigürasyonunu büyük bir doğrulukla yeniden oluşturmanıza izin veren bloğun yüzeyine yapışır ve bulamacı kalıbın yüzeyine sabitlemek ve katmanını daha yoğun ve daha kalın hale getirmek için granüler malzeme gereklidir..
Yeni uygulanan bulamaç ve granüler malzeme tabakası pratik olarak kalıp yüzeyine yapışmaz. Kaymasını engelleyen tek şey ıslatma kuvvetleridir. Bu forma gerekli gücün verilmesi, sonraki kurutma işleminde - kimyasal sertleştirmede gerçekleştirilir. Çok katmanlı bir döküm kalıbının üretimi için üç aşamanın gerçekleştirilmesi gerektiği ortaya çıktı - kabuğu bir süspansiyonla nemlendirin, granül malzeme ile serpin ve ardından kurutun. Bu işlem ortalama 4 ila 6 kez gerçekleştirilir. Ancak daha güçlü bir kasa hazırlamak gerekirse miktar 12 katına kadar arttırılabilir.
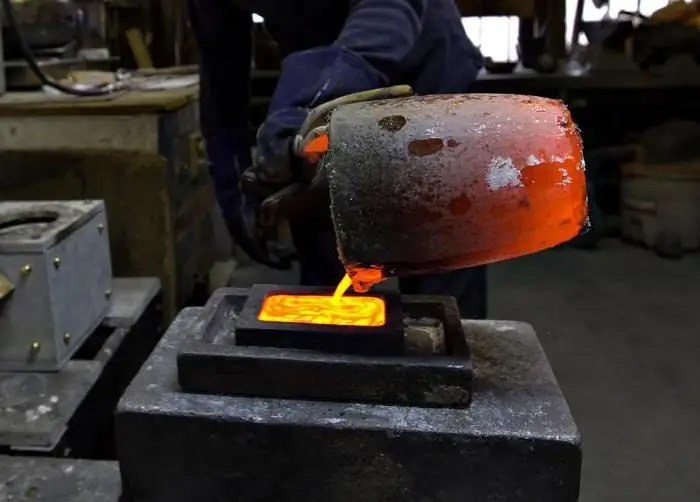
Çift katmanlı muhafazalar
İki katmanlı kalıpların üretimi daha az prosedürle gerçekleştirilir. Kalıp hazırlamanın ilk aşaması, çok katmanlı kalıpların üretiminden farklı değildir. Blok ıslatılır ve granül bir ürün ile serpilir. Ancak foretik adı verilen ikinci tabakayı uygulamaya başlamadan önce birinci tabaka mutlaka elektrolit içeren bir süspansiyon ile tekrar nemlendirilmelidir. Örneğin bileşim, 2. türden bir iletken olan hidroklorik asit içerebilir. Ek olarak, bulamaç ayrıca kalıp için bir bağlayıcı içermelidir. Ve ıslattıktan sonra tekrar granüler malzeme serpin.
Bloğun üzerine iki kat uygulandıktan sonra kalıbın kurutulma işlemi başlar. Et kalınlığı 6-8 mm'yi geçmeyecek bir kalıp elde edilmesi gerekiyorsa bu yeterlidir. Bu göstergenin artırılması gerekiyorsa iki katman daha uygulanır.
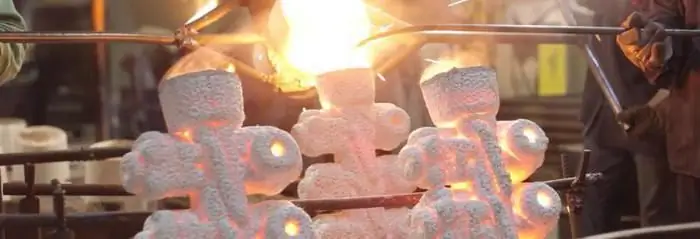
Çeşitler
Metal döküm işlemi için, içine her zaman erimiş maddenin döküldüğü bir döküm kalıbı gereklidir. Bu formlar arasındaki temel fark, bir kerelik ve çoklu kullanımdır. Ancak bu iki farklı form türü de birkaç sınıfa ayrılır.
Kum bazlı tek kullanımlık kalıplar vardır. Bu tip döküm kalıplarının imalatı için, özel bir makinede suyla karıştırılan özel silisli kum ve diğer bağlayıcı elemanlar kullanılır. Bu kategorideki kalıplar, her şekil ve boyutta parça üretmek için kullanılır.
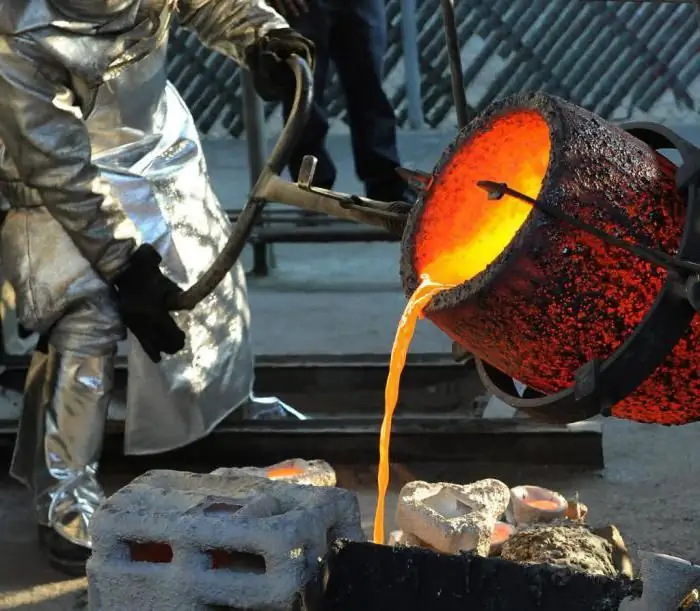
Demir dışı metaller dökülürken, çoğunlukla tek kullanımlık kabuk kalıplar kullanılır. Alçı kabuk kalıplar (alçıtaşı ve hızlı sertleşen bir polimerden oluşur) bir döküm modelinin astarlanması işlemi için kullanılır. Alçı kabuk formu kuruduktan sonra iki parçaya kesilir ve tekrar kurutulur. Bundan sonra form bağlanır ve içine metal dökülebilir.
Erişen döküm
Eriterek döküm işlemini başarılı bir şekilde uygulamak için silikon dioksit bazlı kabuk kalıplar kullanılır. Bu maddeçeşitli bağlayıcı elemanlar tarafından bir arada tutulan bir tozdur. Bu tür kalıpların kullanımı, erime noktası yüksek bir parçanın üretilmesi gerektiğinde ortaya çıkar.
Ergen metal döküm kalıbı çeşitli elemanlarla doldurulur. Parafin veya daha sonra donmuş cıva veya plastik olabilir. Modelin üretiminden sonra bir nevi refrakter malzeme ile astarlanır. Kalıbı ve refrakter tabakayı sıkıştırmak için titreşim kullanılır. Sertleştirme işlemi tamamlandıktan sonra, kabuk ısıtılır, bu nedenle blok erir ve dışarı akar, kalıp kalır ve içine metal dökmek için kullanılabilir.
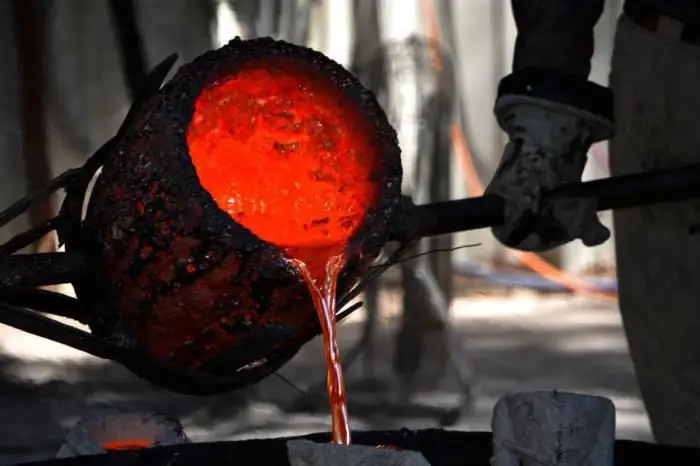
Yeniden kullanılabilir kalıplar
Kullanımı açısından tekrar kullanılabilir olan döküm kalıplar, döküm, bakır, pirinç veya ısıya dayanıklı çelik gibi malzemelerden yapılmaktadır. Yeniden kullanılabilir kalıplar, uygulamalarını demir dışı metal dökümde bulmuştur. Çinko, pirinç veya alüminyum alaşımlarının dökümünde kullanılırlar. Bunların yanı sıra grafit malzemeden yapılan kalıplar da aktif olarak kullanılmaktadır. Bu tür bloklar birkaç yüz döküme kadar dayanabilir. Grafitten kalıp üretme işlemi, malzeme üzerinde mekanik etki ile gerçekleştirilir. Çoğu zaman, bu formun tasarımı, birbirine tutturulmuş birkaç parçadan oluşur. Bu kalıbın tek açık kısmı eriyiğin döküldüğü deliktir.
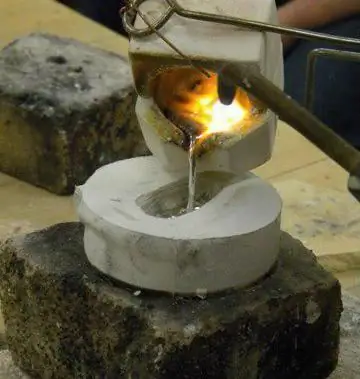
Kalıplar
Konuşmakdöküm için kullanılan birden fazla kalıp, kalıplar da ayırt edilebilir. Bunlar, erimiş metal akışının yerçekimi ile gerçekleştirildiği açık tip kalıplardır. Çoğu zaman, bir döküm kalıbının üretimi, dökme demirden gerçekleştirilir. Ancak metalleri kalıba dökerken belirli kurallara kesinlikle uyulması ve belirli özelliklere dikkat edilmesi gerektiğini bilmelisiniz.
- Metalin dökülmesinin sonraki her aşamasından önce kalıbın temizliğini dikkatlice izlemek gerekir.
- İçine döküldüğünde metalin kalıbın duvarlarına sıçramasını önlemek gerekir.
Her döküm işleminden sonra kalıp temizlenir ve her zaman iç yüzeye kalıplama yapışmaz boyaları uygulanır. Kalıp, kullanılamaz hale gelmeden önce 100'e kadar döküm tutabilir.
Şekillendirme Malzemeleri
Döküm kalıpları yapmak için kullanılan malzemelere kalıplama denir.
Tek kullanımlık kalıplar oluşturmak için malzemenin mukavemet, kalıba uygulanan dinamik etkilere karşı direnç ve dökülen metalin uyguladığı hidrostatik basınca dayanma yeteneği gibi gereksinimleri karşılamasına özen gösterilmelidir..
Kalıpları yeniden kullanılabilir hale getirmek için malzemeye mukavemet açısından daha yüksek taleplerde bulunmak gerekir. Ancak, bu malzemeler için geçerli olan tüm gerekliliklerle birlikte kabul edilebilir bir fiyata sahip olmaları gerektiğini anlamak önemlidir. Aksi haldebu tür formlarda üretilen parçalar çok yüksek bir nihai maliyete sahip olacaktır. Ve satış fiyatı daha da yüksek olacak.
Önerilen:
Silikon kalıpta döküm: ekipman. Silikon kalıplarda vakumlu döküm
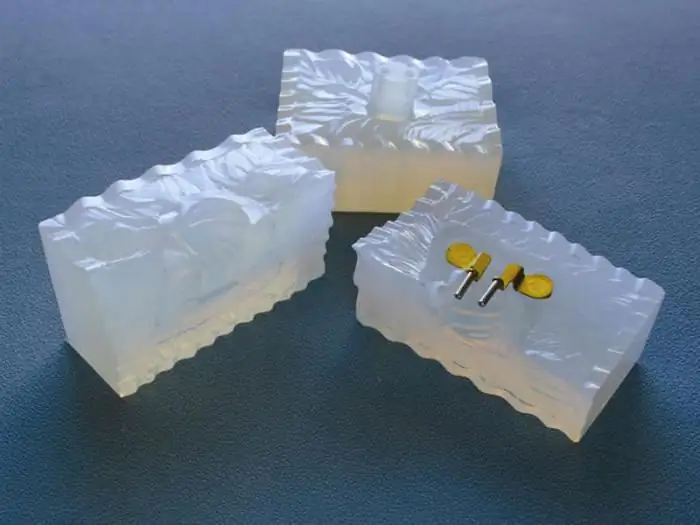
Az sayıda plastik boşluk üretimi için, çoğunlukla silikon kalıplara vakumlu döküm kullanılır. Bu yöntem oldukça ekonomiktir (metal kalıp yapmak daha fazla zaman ve para gerektirir). Ayrıca silikon kalıplar tekrar tekrar kullanılır ve bu da üretim maliyetini önemli ölçüde az altır
Yüksek frekans üreteci: genel bakış, özellikler, türler ve özellikler
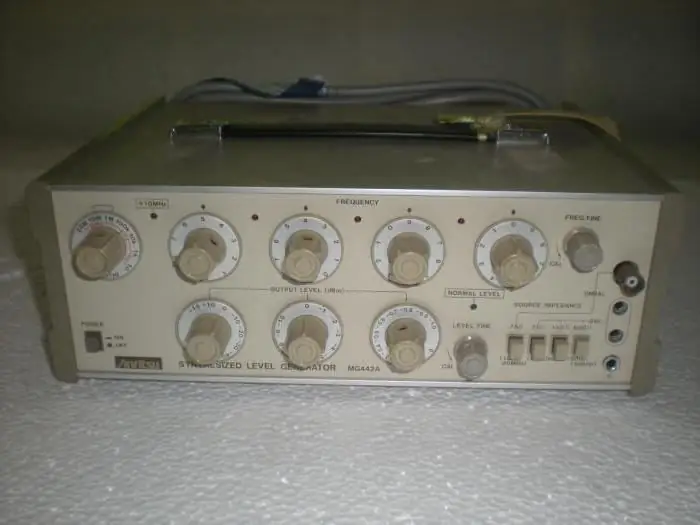
Şu anda, çeşitli elektrikli aletlerin sayısı çoktur. Bunlardan biri yüksek frekanslı bir jeneratördü. Adından da anlaşılacağı gibi salınım frekansını belirli bir aralıkta ayarlamak için kullanılır
Sfero döküm: özellikler, işaretleme ve kapsam
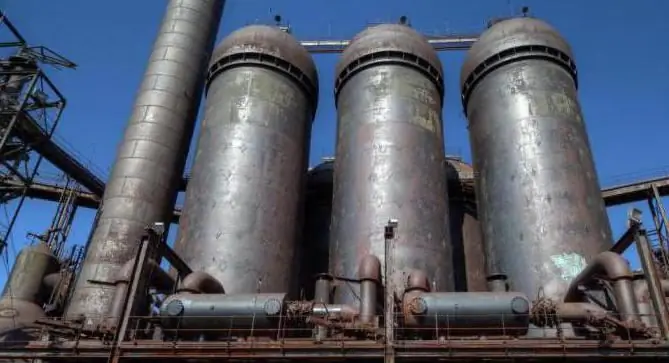
Dökme demir, karbon içeriği C %2,14 ile %6,67 arasında değişen sert, korozyona dayanıklı, ancak kırılgan bir demir-karbon alaşımıdır. Karakteristik eksikliklerin varlığına rağmen, çeşitli türleri, özellikleri ve uygulamaları vardır. Sfero döküm yaygın olarak kullanılmaktadır
Betonun kürlenme programı: özellikler, türler, teknoloji ve temel göstergeler
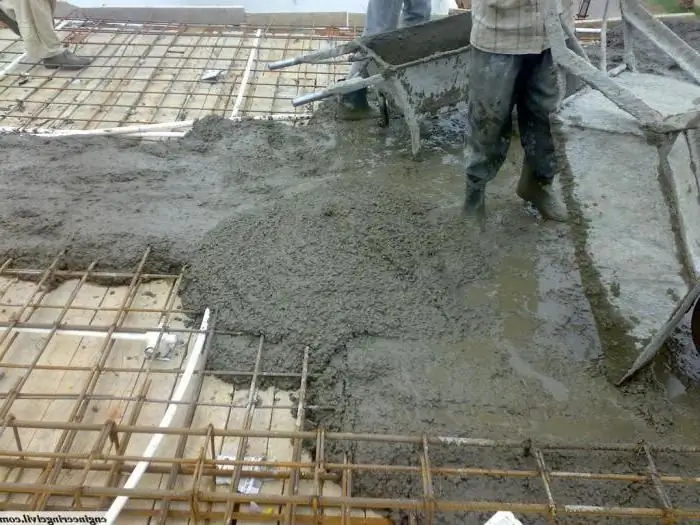
Beton çözeltisi döküldükten sonra belirli bir süre istenilen performans özelliklerini kazanacaktır. Bu zaman aralığına bekletme periyodu denir ve sonrasında koruyucu bir tabaka uygulanabilir
Elektrikli diş açma kalıbı: özellikler, teknik özellikler
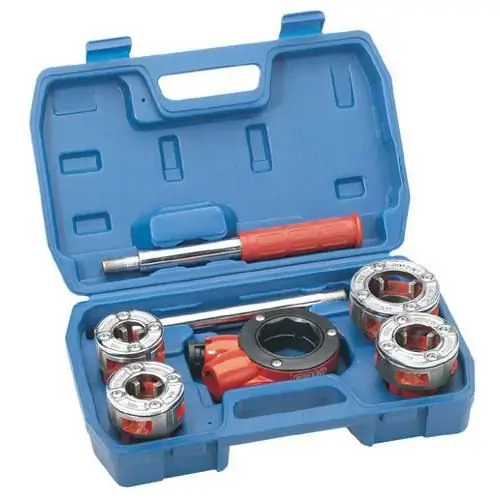
Oymak için zanaatkarlar, seçimi belirli bir görevin gereksinimlerine bağlı olan farklı aletler kullanır. Takım tezgahları için hem el aletleri hem de ekipman olabilir. Bu tür aletlerin ayrı bir grubu, yapısal ve ergonomik verilerde farklılık gösteren borulara diş açmak için kalıp kesiciler ile temsil edilir