2025 Yazar: Howard Calhoun | [email protected]. Son düzenleme: 2025-01-24 13:27
Bakır ve alaşımları ekonominin çeşitli sektörlerinde kullanılmaktadır. Bu metal, yapısının işlenmesini de zorlaştıran fizikokimyasal özellikleri nedeniyle talep görmektedir. İşlem oldukça yaygın ısıl işlem teknolojilerine dayanmasına rağmen, özellikle bakırın kaynağı özel koşullar gerektirir.
Bakır boşluklarının özel kaynağı
Diğer birçok metal ve alaşımdan farklı olarak, bakır ürünler, kaynak arkının termal gücünü arttırmayı gerekli kılan yüksek termal iletkenlik ile karakterize edilir. Aynı zamanda, çalışma alanından simetrik ısı tahliyesi gereklidir, bu da kusur riskini en aza indirir. Bakırın bir diğer dezavantajı akışkanlıktır. Bu özellik, tavan ve dikey dikişlerin oluşumunda bir engel haline gelir. Büyük kaynak havuzlarında bu tür işlemler hiç mümkün değildir. Küçük hacimli işler bile, grafit bazlı kısıtlayıcı astarların kullanımıyla özel koşulların düzenlenmesini gerektirir.ve asbest.
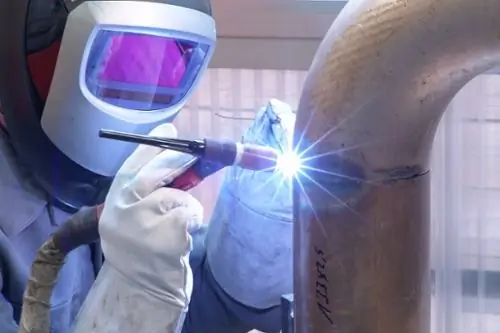
Metalin oksitlenme eğilimi, silikon, manganez ve fosfor jelleri gibi özel katkı maddelerinin refrakter oksit oluşumu ile bazı modlarda kullanılmasını da gerektirir. Bakır kaynağının özellikleri gazların emilmesini içerir - örneğin hidrojen ve oksijen. Optimal termal maruz kalma modunu seçmezseniz, dikiş kalitesiz olacaktır. Gazla aktif etkileşim nedeniyle yapısında büyük gözenekler ve çatlaklar kalacaktır.
Bakırın yabancı maddelerle etkileşimi
Bakırın genel olarak çeşitli safsızlıklar ve kimyasal elementlerle etkileşiminin doğasını hesaba katmak gerekir, çünkü bu metalin kaynak işleminde farklı malzemelerden elektrotlar ve teller sıklıkla kullanılır. Örneğin, alüminyum bir bakır eriyiği içinde çözülebilir, bu da korozyon önleyici özelliklerini arttırır ve oksitlenebilirliği az altır. Berilyum - mekanik direnci arttırır, ancak elektrik iletkenliğini az altır. Bununla birlikte, belirli etkiler koruyucu ortamın doğasına ve sıcaklık rejimine de bağlı olacaktır. Böylece bakırın 1050 °C'de kaynaklanması, demir bileşenin iş parçasının yapısına yaklaşık %3,5 katsayı ile girişini kolaylaştıracaktır. Ancak yaklaşık 650 ° C'lik bir rejimde bu rakam% 0.15'e düşürülecek. Aynı zamanda, demir, bakırın korozyon direncini, elektriksel ve termal iletkenliğini keskin bir şekilde az altır, ancak gücünü arttırır. Bu tür iş parçalarını etkilemeyen metallerden kurşun ve gümüş ayırt edilebilir.
Temel bakır kaynak yöntemleri
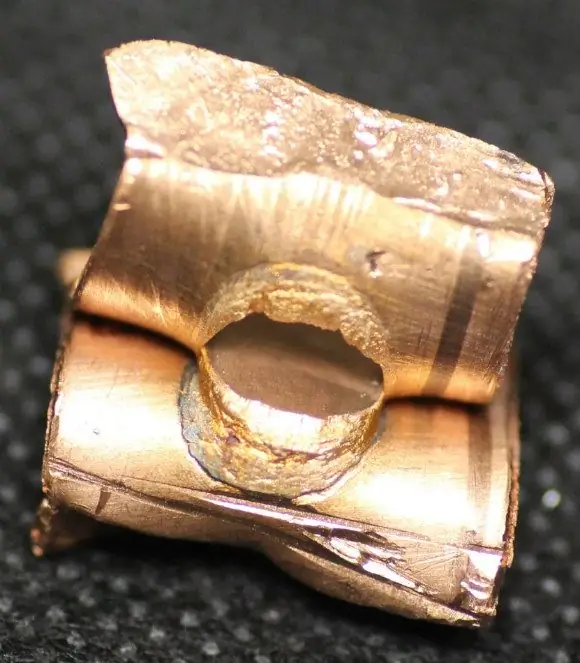
Manuel ve otomatik dahil tüm yaygın kaynak yöntemlerine çeşitli konfigürasyonlarda izin verilir. Bir veya başka bir yöntemin seçimi, bağlantı gereksinimleri ve iş parçasının özellikleri ile belirlenir. En verimli işlemler arasında elektro cüruf ve toz altı ark kaynağı bulunur. Tek bir işlemde yüksek kaliteli bir dikiş elde edilmesi planlanıyorsa, gaz teknolojisine dönülmesi tavsiye edilir. Bakır ve alaşımlarını düşük sıcaklık gradyanlarında kaynaklamaya yönelik bu yaklaşım, iş parçasının deoksidasyonu ve alaşımlanması için uygun koşullar yaratır. Sonuç olarak, dikiş olumlu bir şekilde değiştirilmiş ve dayanıklıdır. Saf bakır için tungsten elektrotlu ark kaynağı teknikleri ve koruyucu gazlar kullanılabilir. Ancak çoğu zaman bakır türevleriyle çalışırlar.
Hangi ekipman kullanılıyor?
Ön bakır ürünler, kaynak için boyutsal boşluklar oluşturmak amacıyla tornalama, taşlama ve freze makinelerinde işlenebilir. Endüstri ayrıca, neredeyse mükemmel kesme kenarlarıyla kesmeye olanak sağlayan plazma ark kesme tekniğini kullanır. Bakırın doğrudan kaynağı, argon-ark tesisatları, yarı otomatik cihazlar ve invertör cihazları ile gerçekleştirilir. Ekipmanın mevcut gücü, iş parçasının boyutuna bağlı olarak 120 ila 240 A arasında değişebilir. Elektrotların kalınlığı genellikle 2,5-4 mm'dir - yine, işin karmaşıklığına ve hacmine bağlıdır.
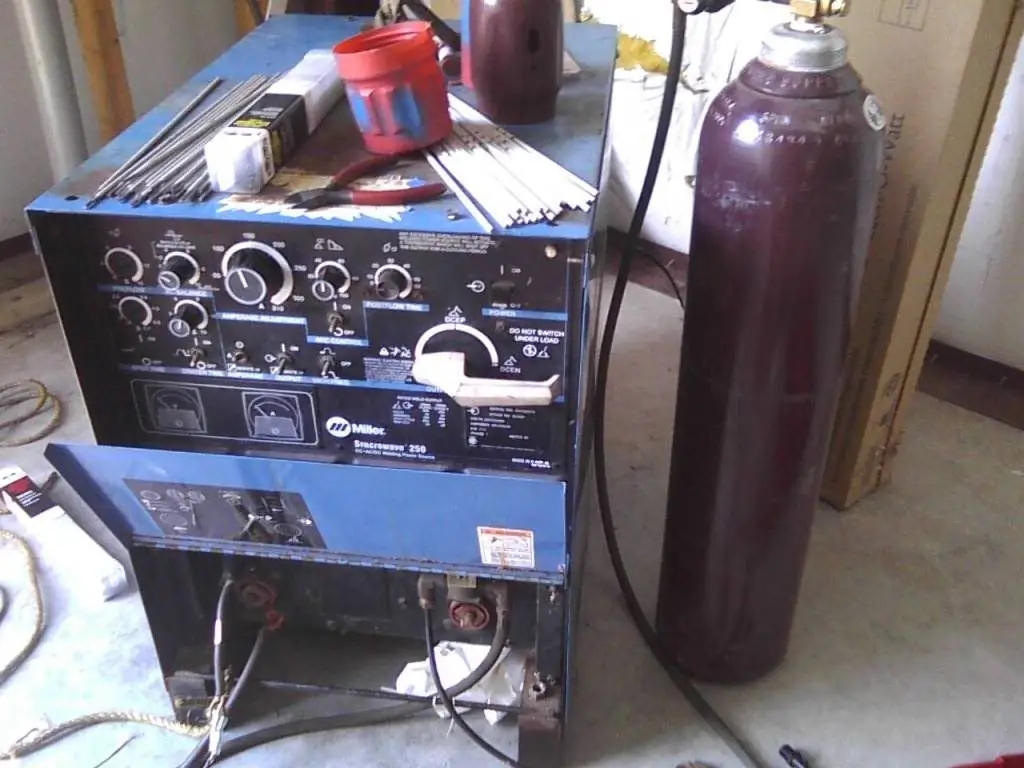
Bakır argon kaynağı
En popüler yöntemlerden biri. Özellikle, tungsten elektrotların kullanımını içeren bahsedilen argon-ark kaynağı tekniği kullanılır. Isıtma sırasında bakır, oksijenle etkileşime girerek iş parçasının yüzeyinde bir dioksit kaplama oluşturur. Bu aşamada iş parçası bükülebilir hale gelir ve tüketilmeyen bir elektrotun bağlanmasını gerektirir. Örneğin, MMZ-2 markasının çubukları, koruyucu ortam ile argon ile bakır kaynağı yaparken optimum kaynak kalitesi sağlar. İş parçasına güçlü bir nüfuz etme görevi ayarlanmazsa, nitrojen ortamında hafif bir kaynak versiyonu kullanılabilir. Bu, düşük voltajlarda iyi bir termal etki yöntemidir, ancak kombine gazlar kullanılarak kaynak kalitesi açısından daha da büyük bir etki elde edilebilir. Örneğin deneyimli kaynakçılar genellikle %75 argon içeren karışımlar kullanır.
Gaz Kaynak
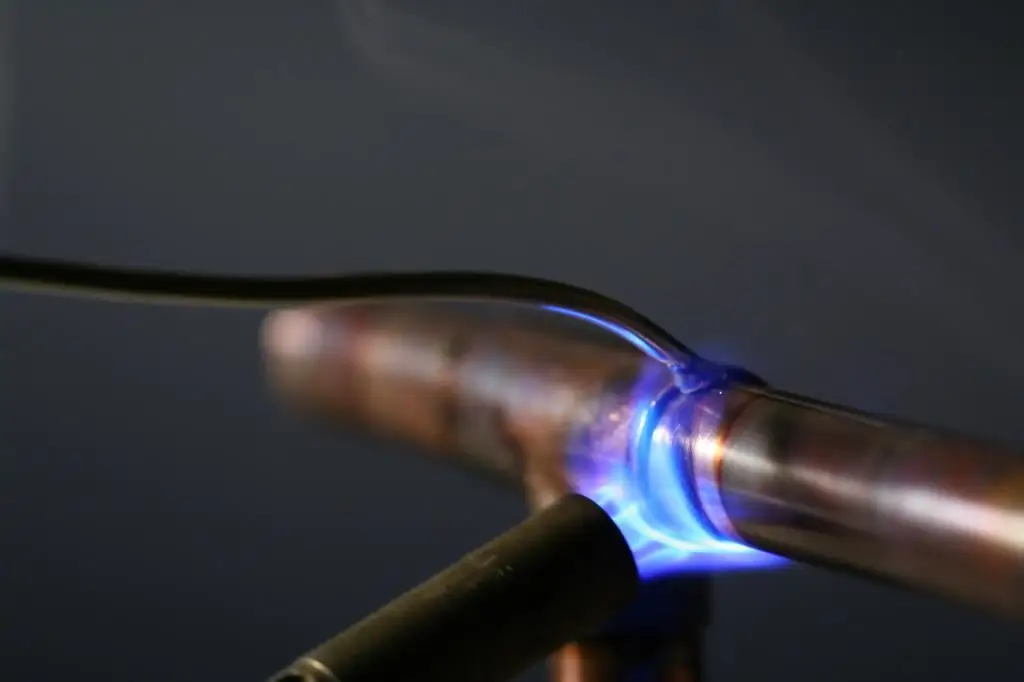
Bu durumda, alev sıcaklığının önemli ölçüde artması nedeniyle bir oksijen-asetilen ortamı kullanılır. Çalışma sürecinde bir gaz brülörü kullanılır. Bu makine performansında iyidir, ancak sınırlı ayar seçenekleri, kaynak havuzunun parametrelerinde ince ayar yapmanıza izin vermez.
Genellikle kullanılan ve iki brülörün bağlantısıyla bölünmüş termal maruz kalma yöntemi. Biri çalışma alanını ısıtmaya, ikincisi ise doğrudan hedef iş parçasının gaz kaynağına hizmet eder. Bu yaklaşım, kalın 10 mm levhalar için önerilir. İkinci bir brülör yoksa,daha sonra gelecekteki dikiş hattı boyunca iki taraflı ısıtma yapabilirsiniz. Efekt çok kaliteli değil ama asıl görev gerçekleştirilmiş.
Temiz bir derz yapısı elde etmek için gaz kaynağı tekniğine ve akı enjeksiyonuna izin verir. Özellikle, bor metil eterin metil ile azeotropik çözeltileri gibi gazlı akışlar kullanılır. Bu tür karışımların aktif buharları, kaynak havuzunun özelliklerini değiştirerek brülöre gönderilir. Bu noktada alev yeşilimsi bir renk alır.
Karbon elektrot kaynağının özellikleri
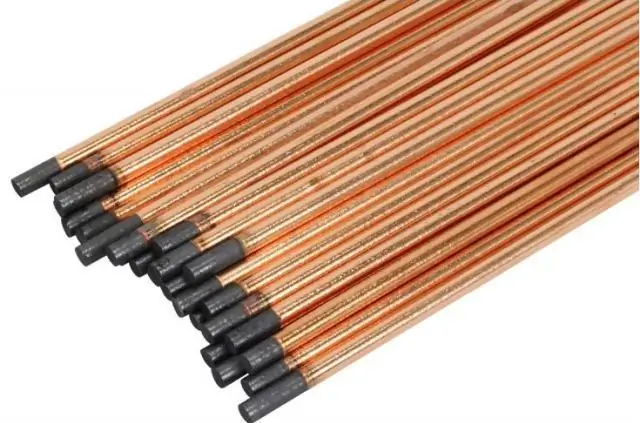
Bakır alaşımları için en uygun ark kaynağı yöntemi. Başlıca ayırt edici özelliği ergonomi ve çok yönlülük olarak adlandırılabilir - en azından operatör tarafından fiziksel eylemleri gerçekleştirme mekaniği ile ilgili her şeyde. Örneğin, bir kaynakçı, minimum bir dizi yardımcı koruyucu ekipman kullanarak manipülasyonları doğrudan havada gerçekleştirebilir. Bunun nedeni, ısıtma işlemi sırasında karbon elektrotların, üzerine düşük güçlü bakırın kaynaklandığı yeterli miktarda termal enerji vermesidir. Sürecin verimsiz olduğu ortaya çıkıyor, ancak bağlantı gerekli tüm mekanik nitelikleri kazanıyor.
Manuel ark kaynağı
Bu kaynak yönteminin teknolojisi, kaplanmış elektrotların kullanımını içerir. Bu, bağlantının yeterli mukavemet özellikleri alacağı, ancak ürün yapısının bileşiminin sonuçta birincil iş parçasından farklı olacağı anlamına gelir. Spesifik modifikasyon parametreleri, alaşımlı oksijen gidericilerin özelliklerine göre belirlenir,elektrot kaplamasında bulunanlar. Örneğin, aktif bileşimde düşük karbonlu ferromanganez, fluorspar, alüminyum tozu vb. Gibi bileşenler kullanılabilir. Bu bakır kaynak teknolojisi ve bağımsız kaplama üretimine izin verir. Genellikle bunun için sıvı camda yoğrulmuş kuru bir karışım kullanılır. Böyle bir kaplama, dikişi daha yoğun hale getirir, ancak yapının elektriksel iletkenliği önemli ölçüde azalır. Kaplanmış elektrotlarla genel kaynak işlemi, bakır için istenmeyen yüksek sıçrama ile karakterize edilir.
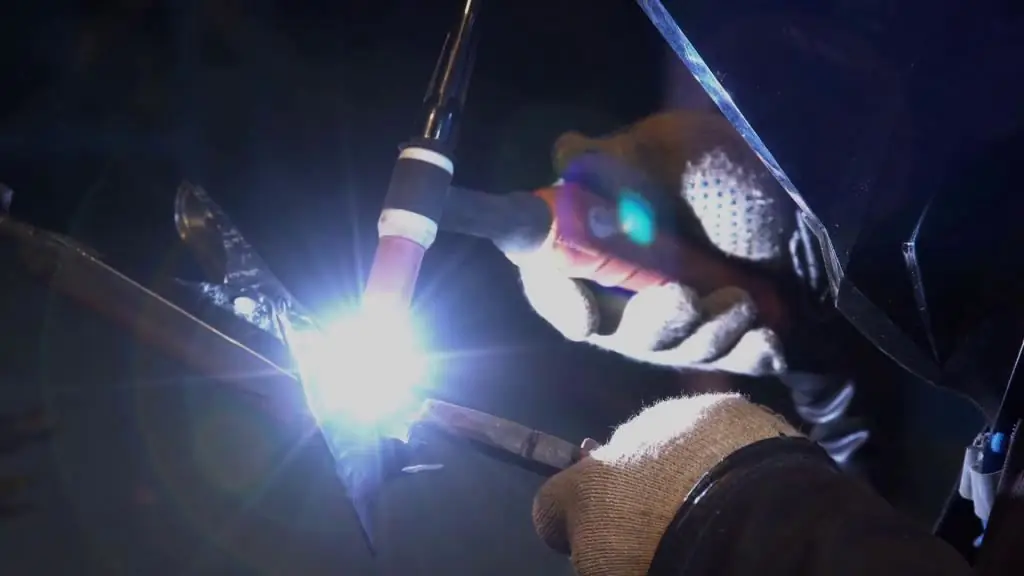
Toz altı Ark Kaynağı
Bakır ile kaynak yapmak için akının kendisine bir ark stabilizatörü ve en önemlisi atmosferik havanın olumsuz etkilerine karşı koruyucu bir bariyer olarak ihtiyaç vardır. İşlem, sarf malzemesi olmayan grafit veya karbon elektrotların yanı sıra seramik bir akış altında tüketilebilir çubuklar kullanılarak organize edilir. Karbon sarf malzemeleri kullanılıyorsa, bakır kaynak elektrotları bir spatula şeklinde düz bir uç oluşturacak şekilde bilenir. Çalışma alanına yandan tombak veya pirinçten yapılmış bir dolgu malzemesi de verilir - bu, dikiş yapısını deoksidize etmek için gereklidir.
İşlem ısıtmalı doğru akımda gerçekleştirilir. Çoğu zaman deneyimli kaynakçılar, alaşımlı telle malzemenin bileşimini iyileştirmeye çalışsa da, çeşitli koruma bariyerleri iş parçasının temel yapısını korur. Yine, istenmeyen eriyik akışlarını önlemek için, başlangıçta bir grafit substrat sağlanması tavsiye edilir,bu da akı için bir form işlevi görecektir. Bu yöntem için optimum çalışma sıcaklığı 300-400 °C'dir.
Korumalı Ark Kaynağı
İnverter ve diğer yarı otomatik cihazların bağlantısı ile kaynak işlemleri tel beslemeli gazlı ortamda gerçekleştirilir. Bu durumda, argon ve nitrojene ek olarak, helyum ve ayrıca çeşitli gaz karışımları kombinasyonları kullanılabilir. Bu tekniğin avantajları, iş parçasının mekanik özelliklerinin yüksek derecede korunması ile kalın iş parçalarının etkili bir şekilde nüfuz etme olasılığını içerir.
Güçlü termal etki, yanan gazlı bir ortamda yüksek verimli plazma akışları ile açıklanır, ancak bu parametreler ayrıca belirli bir invertör modelinin özellikleri ile belirlenecektir. Aynı zamanda, 1-2 mm kalınlığındaki iş parçalarına göre bakırın argon-ark kaynağı tekniği daha çok tercih edilir. Gazlı ortamın koruyucu işlevine gelince, tamamen güvenilemez. Telden oksitlenme, gözeneklilik ve katkı maddelerinin olumsuz etkileri riski vardır. Öte yandan, argon ortamı iş parçasını havadaki oksijene maruz kalmaktan etkili bir şekilde korur.
Sonuç
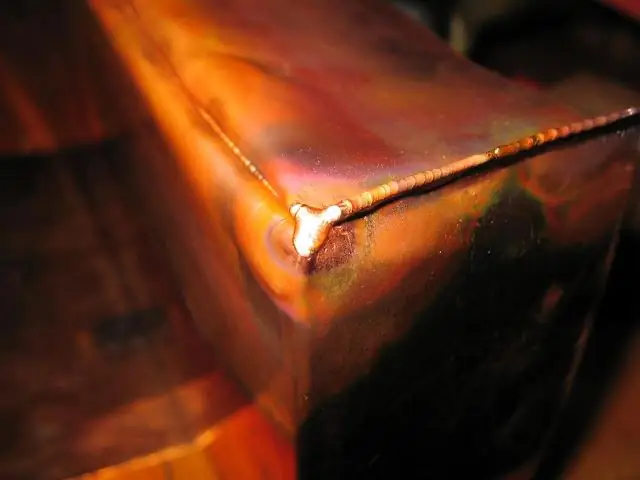
Bakırı diğer metallerden ayıran birçok özelliği vardır. Ancak, alaşımlarının genel grubu içinde bile, her durumda bir dikiş oluşturmak için en uygun teknolojiyi seçmek için bireysel bir yaklaşım aramayı gerektiren birçok farklılık vardır. Örneğin, büyük bir iş parçasında güçlü bir bağlantı kurmanız gereken durumlarda gaz kaynağı uygundur. Ancak yeni gelenlerbrülörler ve gaz tüpleri ile çalışmak için yüksek güvenlik gereksinimleri nedeniyle bu yöntem önerilmez. Yüksek hassasiyetli küçük formatlı kaynak işlemleri, kullanışlı ve üretken yarı otomatik makinelere emanet edilmiştir. Deneyimsiz bir operatör, iş akışının parametrelerini tam olarak kontrol ederek bu tür ekipmanları da kullanabilir. Gazlı ortamın önemini unutmayınız. Sadece kaynak sırasında iş parçasının yalıtkanı olarak değil, aynı zamanda malzemenin bazı teknik ve fiziksel özelliklerini iyileştirmenin bir yolu olarak da kullanılabilirler. Aynısı, pozitif bir alaşım etkisine katkıda bulunabilen elektrotlar için de geçerlidir.
Önerilen:
Mineral zenginleştirme: temel yöntemler, teknolojiler ve ekipman
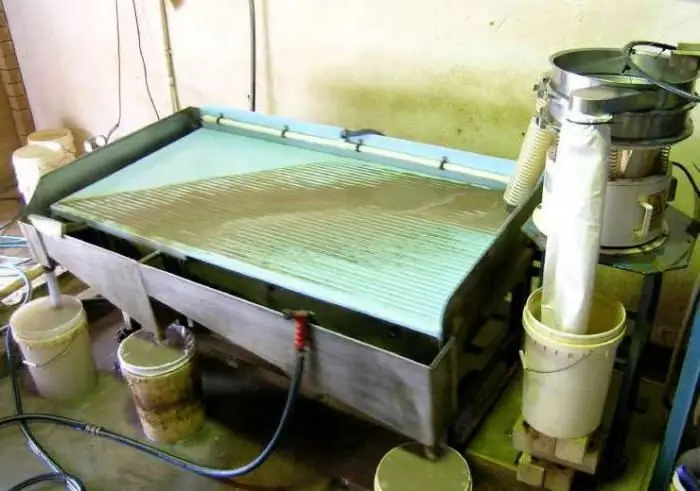
Makale maden işleme teknolojisine ayrılmıştır. Bu tür işlemeyi gerçekleştirmek için aşamalar ve yöntemler açıklanmaktadır
Alüminyum ve alaşımlarının korozyonu. Alüminyumun korozyona karşı mücadele ve korunması için yöntemler
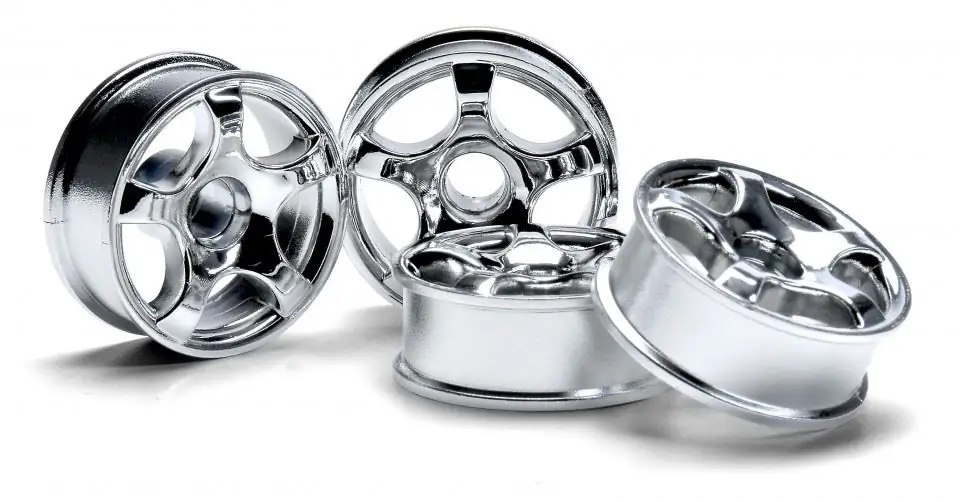
Alüminyum, demir ve çeliğin aksine korozyona karşı oldukça dayanıklıdır. Bu metal, yüzeyinde oluşan yoğun bir oksit filmi ile pastan korunur. Bununla birlikte, ikincisinin imhası durumunda, alüminyumun kimyasal aktivitesi büyük ölçüde artar
Bakır ve alaşımlarının korozyonu: nedenleri ve çözümleri
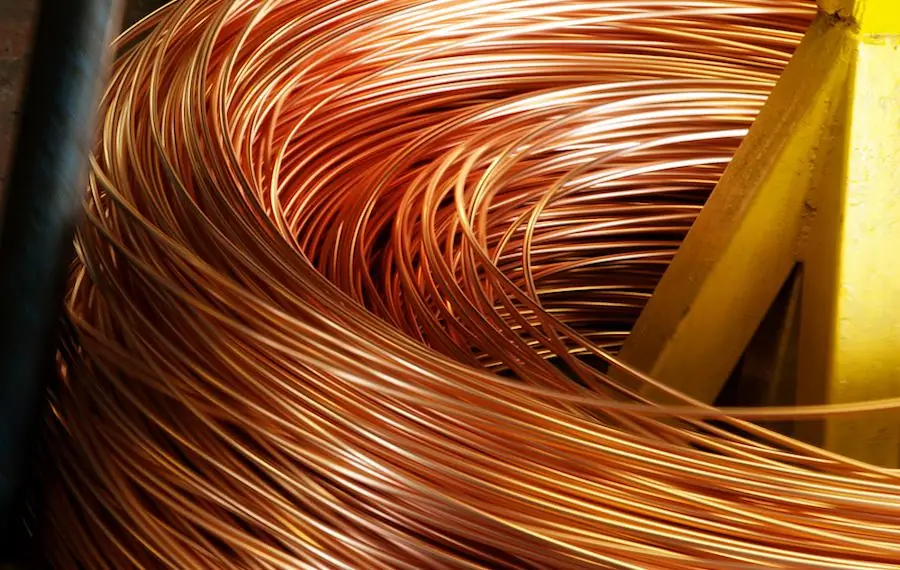
Bakır ve bakır alaşımları yüksek elektriksel ve termal iletkenliğe sahiptir, işlenebilir, iyi korozyon direncine sahiptir, bu nedenle birçok endüstride aktif olarak kullanılırlar. Ancak belirli bir ortama girdiğinde bakır ve alaşımlarının korozyonu yine kendini gösterir. Nedir ve ürünlerin hasardan nasıl korunacağını bu makalede ele alacağız
Güç kaynağı sistemi: tasarım, kurulum, çalıştırma. Otonom güç kaynağı sistemleri
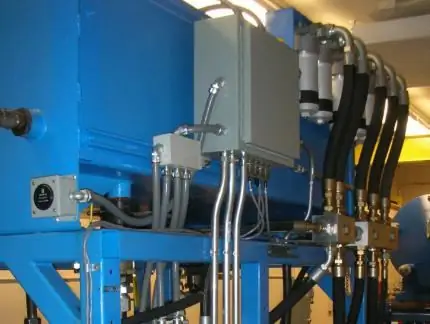
Binaların ve endüstriyel komplekslerin bakım kalitesinin iyileştirilmesi, elektrik kaynaklarının ve ilgili altyapının yaygın olarak kullanılmasına yol açmıştır
Alın kaynağı: ekipman, yöntemler ve proses teknolojisi
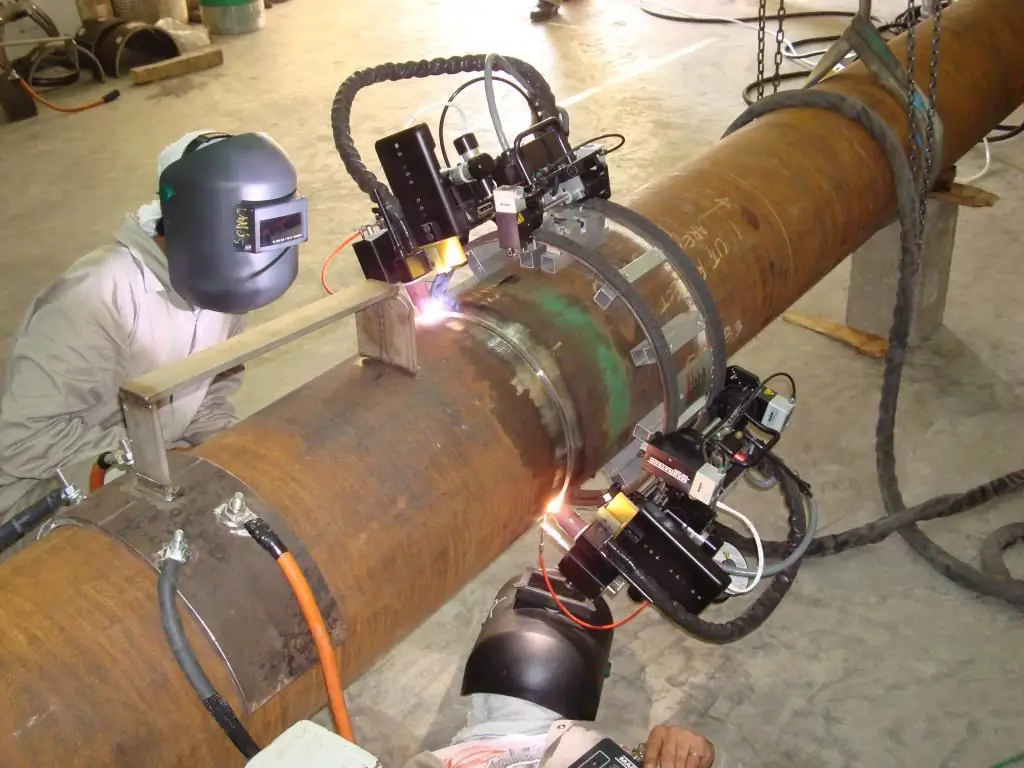
Flaş alın kaynağının özellikleri. Alın kaynağı bağlantılarının türleri ve ayrıca alın kaynağı işlemini gerçekleştirmek için ekipman, yöntemler ve teknoloji. Flaş alın kaynağından kaynaklanan kaynak dikişi kusurları ve oluşum nedenleri