2025 Yazar: Howard Calhoun | [email protected]. Son düzenleme: 2025-01-24 13:27
Yalın üretim, şirket yönetiminin özel bir planıdır. Ana fikir, her türlü maliyeti ortadan kaldırmak için sürekli çaba göstermektir. Yalın üretim, her bir çalışanın optimizasyon prosedürüne dahil edilmesini içeren bir kavramdır. Böyle bir şema, tüketiciye maksimum yönelimi amaçlamaktadır. Yalın üretim sisteminin ne olduğuna daha yakından bakalım.
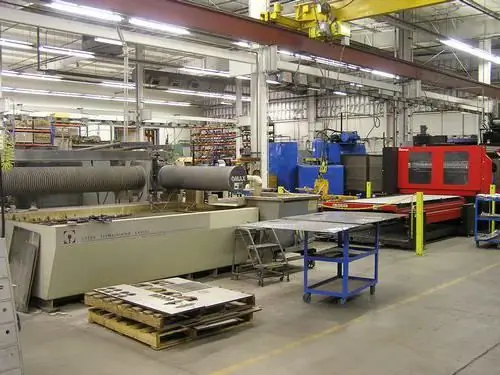
Olay tarihi
Yalın üretimin endüstriye girişi 1950'lerde Toyota Corporation'da gerçekleşti. Böyle bir kontrol şemasının yaratıcısı Taiichi Ohno'ydu. Hem teorinin hem de pratiğin daha da gelişmesine büyük katkı, diğer şeylerin yanı sıra hızlı değişim için bir yöntem yaratan meslektaşı Shigeo Shingo tarafından yapıldı. Daha sonra, Amerikalı uzmanlar sistemi araştırdı ve yalın üretim (yalın üretim) - "yalın üretim" adı altında kavramsallaştırdı. İlk başta, konsept öncelikle otomotiv endüstrisinde uygulandı. Bir süre sonra şema sürece uyarlandı.üretme. Daha sonra, sağlık, kamu hizmetleri, hizmetler, ticaret, askeri, devlet ve diğer sektörlerde yalın üretim araçları kullanılmaya başlandı.
Öne Çıkanlar
İşletmede yalın üretim, nihai tüketici için üretilen ürünün değerinin yaratılışın her aşamasında analizini içerir. Konseptin temel amacı, sürekli bir maliyet eliminasyonu sürecinin oluşturulmasıdır. Başka bir deyişle, yalın üretim, kaynakları tüketen ancak son kullanıcı için herhangi bir değer yaratmayan herhangi bir faaliyetin ortadan kaldırılmasıdır. Örneğin, bitmiş ürünün veya bileşenlerinin stokta olmasına ihtiyacı yoktur. Geleneksel sistemde, evlilik, yeniden işleme, depolama ve diğer dolaylı maliyetlerle ilgili tüm maliyetler tüketiciye yansıtılır. Yalın üretim, tüm şirket faaliyetlerinin ürüne değer katan ve katmayan süreç ve operasyonlara ayrıldığı bir şemadır. Bu nedenle asıl görev, ikincisinin sistematik olarak az altılmasıdır.
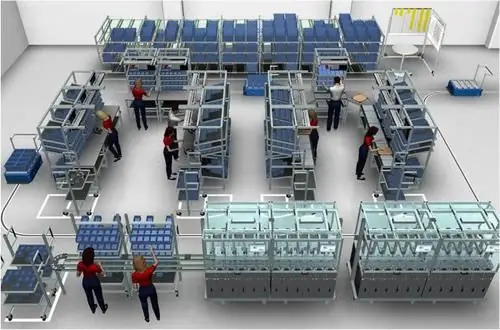
Yalın atık
Maliyetlerin eş anlamlısı olarak bazen muda terimi kullanılır. Bu kavram çeşitli giderler, çöpler, atıklar vb. Taiichi Ohno yedi tür maliyet belirlemiştir. Kayıplar şunlardan kaynaklanır:
- bekle;
- aşırı üretim;
- nakliye;
- ekstra işlem adımları;
- gereksiz hareketler;
- arızalı malları serbest bırakmak;
- fazla envanter.
Taiichi Ohno'nun aşırı üretim olarak değerlendirdiği ana kayıp türü. Diğer maliyetlerin ortaya çıkması nedeniyle bir faktördür. Yukarıdaki listeye bir madde daha eklendi. Toyota deneyimi üzerine bir araştırmacı olan Jeffrey Liker, çalışanların gerçekleşmemiş potansiyelini bir israf olarak nitelendirdi. Maliyet kaynakları aşırı yüklenmiş kapasite, artan yoğunlukta faaliyetler yürüten çalışanlar ve ayrıca operasyonun yürütülmesinin düzensizliğidir (örneğin, talepteki dalgalanmalar nedeniyle kesintiye uğramış bir program).
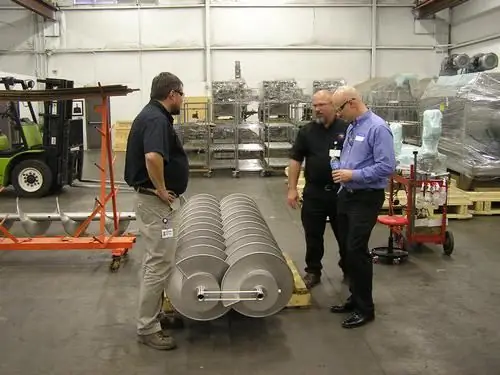
İlkeler
Yalın üretim, beş aşamaya bölünmüş bir süreç olarak sunulur:
- Belirli bir ürünün değerini belirleme.
- Bu ürünün değer akışını oluşturun.
- Sürekli akışın sağlanması.
- Tüketicinin ürünü çekmesini sağlama.
- Mükemmellik için çabalamak.
Yalın üretimin dayandığı diğer ilkeler arasında şunları vurgulamalıyız:
- Mükemmel kaliteye ulaşmak - ilk görüşte, sıfır hata, sorunları erken bir aşamada belirleme ve çözme.
- Bilgi, maliyet ve risk paylaşımı yoluyla tüketiciyle uzun vadeli bir ilişki kurmak.
- Esneklik.
Üretim sistemi,Toyota'da kullanılan sistem iki ana ilkeye dayanmaktadır: özerkleştirme ve "tam zamanında". İkincisi, montaj için gerekli tüm öğelerin, stoğu az altmak için belirli bir süreç için kesinlikle belirlenen miktarda, tam olarak ihtiyaç duyulduğu anda hatta ulaşması anlamına gelir.
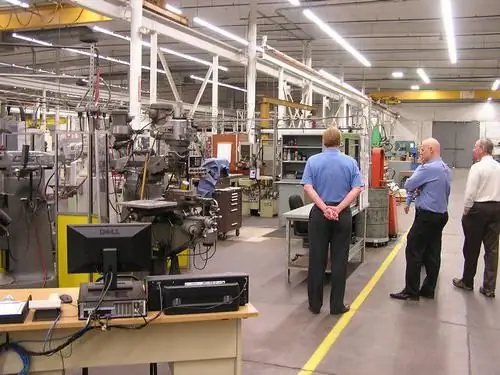
Kompozisyon öğeleri
İncelenen kavram çerçevesinde, çeşitli bileşenler ayırt edilir - yalın üretim yöntemleri. Bazıları kendileri bir kontrol şeması olarak hareket edebilir. Ana öğeler şunları içerir:
- Tek öğe akışı.
- Genel ekipman bakımı.
- 5S sistemi.
- Kaizen.
- Hızlı geçiş.
- Hata önleme.
Endüstri Seçenekleri
Yalın sağlık hizmeti, doğrudan insanlara yardım etmekle ilgili olmayan tıbbi personelin harcadığı zamanı az altma konseptidir. Yalın lojistik, değer akışında yer alan tüm tedarikçileri bir araya getiren bir çekme şemasıdır. Bu sistemde, küçük hacimlerde kısmi rezerv ikmali vardır. Bu şemadaki ana gösterge, lojistik toplam maliyettir. Yalın üretim araçları Danimarka Postanesi tarafından kullanılmaktadır. Konsept kapsamında sunulan hizmetlerde geniş çaplı bir standardizasyon gerçekleştirilmiştir. Etkinliğin amaçları verimliliği artırmak, transferleri hızlandırmaktı. "Çevrimiçi değer oluşumu kartları" tanıtıldıhizmetleri kontrol etmek ve tanımlamak. Ayrıca departman çalışanları için bir motivasyon sistemi geliştirilmiş ve akabinde uygulamaya alınmıştır. İnşaatta, tüm aşamalarda inşaat sürecinin verimliliğini artırmaya odaklanan özel bir strateji oluşturulmuştur. Yalın üretim ilkeleri yazılım geliştirmeye uyarlanmıştır. Dikkate alınan planın unsurları şehir ve eyalet yönetiminde de kullanılmaktadır.
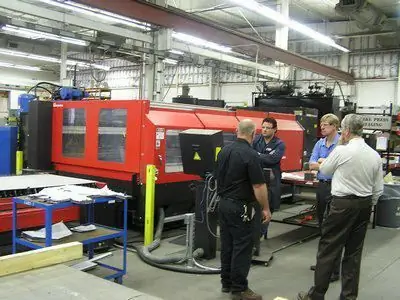
Kaizen
Fikir 1950'de Dr. Deming tarafından formüle edildi. Bu ilkenin getirilmesi Japon şirketlerine büyük kazançlar getirdi. Bunun için uzmana imparator tarafından bir madalya verildi. Bir süre sonra Japonya Bilim ve Teknoloji Birliği onlara bir ödül açıkladı. Üretilen malların kalitesi için Deming.
Kaizen Felsefesinin Faydaları
Bu sistemin faydaları, en yüksek verimlilik ve üretkenliği sağlamak için koşulların oluşturulduğu her endüstriyel sektörde değerlendirilmiştir. Kaizen bir Japon felsefesi olarak kabul edilir. Sürekli değişimi teşvik etmekten oluşur. Kaizen düşünce okulu, sürekli değişimin ilerlemenin tek yolu olduğunda ısrar eder. Sistemin ana vurgusu, gereksiz ve zor işleri ortadan kaldırarak verimliliği artırmaktır. Tanımın kendisi iki kelimeyi birleştirerek oluşturuldu: "kai" - "değişim" ("dönüştürme") ve "zen" - "daha iyiye doğru." Sistemin avantajları, Japon ekonomisinin başarısını oldukça açık bir şekilde yansıtıyor. Bu sadece Japonların kendileri tarafından değil, aynı zamanda uzmanlar tarafından da tanınmaktadır.barış.
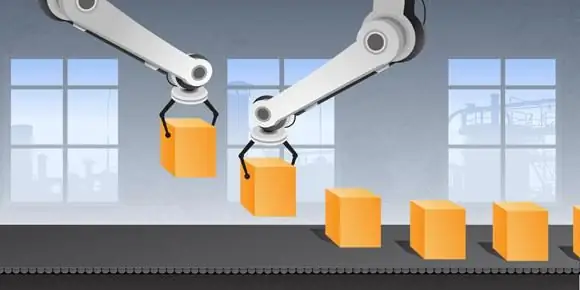
Kaizen Konsept Hedefleri
Üretim geliştirmenin gerçekleştirildiği beş ana yön vardır. Bunlar şunları içerir:
- Atık az altma.
- Anında sorun giderme.
- Optimum kullanım.
- Takım çalışması.
- Üst kalite.
İlkelerin çoğunun sağduyuya dayandığı söylenmelidir. Sistemin ana bileşenleri, her çalışanı sürece dahil etmek, etkileşime ve değişime hazır olmak, malların kalitesini iyileştirmektir. Tüm bu etkinlikler, karmaşık matematiksel hesaplamalar veya bilimsel yaklaşım arayışı gerektirmez.
Atık az altma
Kaizen felsefesinin ilkeleri, her aşamada (işlem, süreç) kayıpları önemli ölçüde az altmayı amaçlar. Programın ana avantajlarından biri, her çalışanı içermesidir. Bu da, yönetimin her düzeyinde iyileştirme önerilerinin geliştirilmesini ve müteakip uygulanmasını içerir. Bu tür çalışmalar kaynak kaybını en aza indirmeye katkıda bulunur.
Hemen sorun giderme
Her çalışan, kaizen kavramına uygun olarak sorunlara karşı koymalıdır. Bu davranış, sorunların hızlı bir şekilde çözülmesine katkıda bulunur. Anında sorun giderme ile teslim süresi artmaz. Sorunların anında çözülmesi, faaliyetleri etkili bir yöne yönlendirmenize olanak tanır.
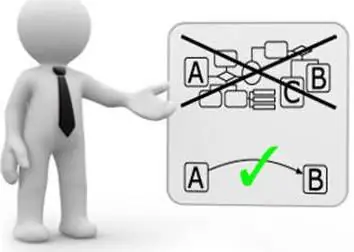
Optimum kullanım
Sorunlar hızlı bir şekilde çözüldüğünde kaynaklar serbest bırakılır. Diğer hedefleri geliştirmek ve gerçekleştirmek için kullanılabilirler. Bu önlemler birlikte, sürekli bir verimli üretim süreci oluşturmayı mümkün kılar.
Ekip çalışması
Sorunların çözümüne tüm çalışanları dahil etmek, daha hızlı bir çıkış yolu bulmanızı sağlar. Zorlukların başarıyla üstesinden gelmek, şirket çalışanlarının ruhunu ve özgüvenini güçlendirir. Takım çalışması, çatışma durumlarını ortadan kaldırır, üst ve alt çalışanlar arasında güvene dayalı ilişkilerin oluşmasını destekler.
En iyi kalite
Hızlı ve verimli problem çözme, ekip çalışmasına ve büyük miktarda kaynak yaratılmasına katkıda bulunur. Bu da ürünlerin kalitesini artıracaktır. Tüm bunlar, şirketin yeni bir kapasite düzeyine ulaşmasını sağlayacak.
Önerilen:
Profesyonelleşme - bu süreç nedir? Aşamalar, profesyonelleşme araçları, olası sorunlar
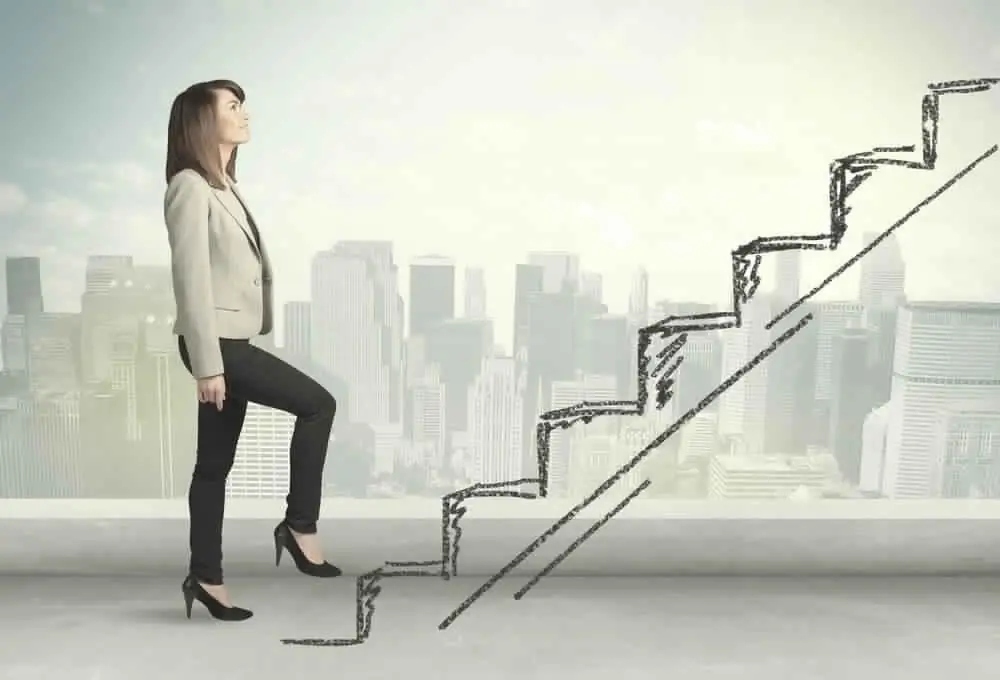
Profesyonelleşme, var olanın gelişmesi ve yeni insan emeği faaliyet türlerinin ortaya çıkması sonucu ortaya çıkan bir olgudur. Konsept, amacı psikolojik, pedagojik, felsefi ve sosyolojik süreçleri incelemek olan yerli bilim adamları sayesinde ortaya çıktı
Stratejik planlama ve stratejik yönetim. Stratejik planlama araçları
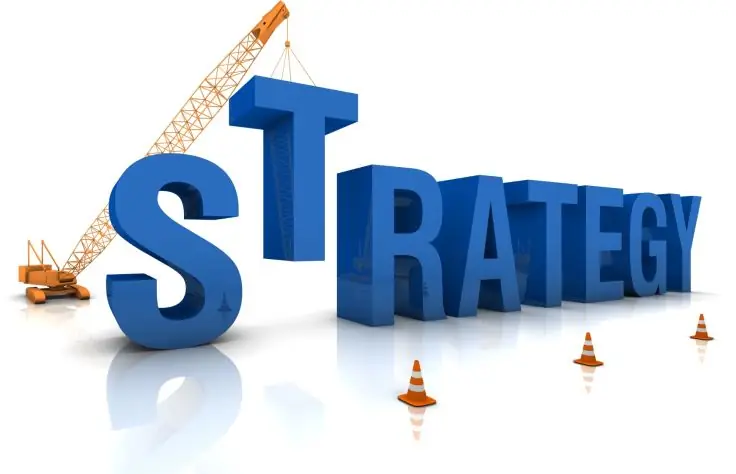
Kapalı şirket geliştirme biçimlerinin stratejik planlama ve yönetim yönetiminin bir yeniliği, durumsal davranışa yapılan vurgudur. Bu konsept, dış tehditleri önlemek ve bir piyasa ortamındaki risklere karşı koruma mekanizmaları geliştirmek için daha fazla fırsat sunar
Taşıma araçları: sınıflandırma ve türleri, tanımı, özellikleri
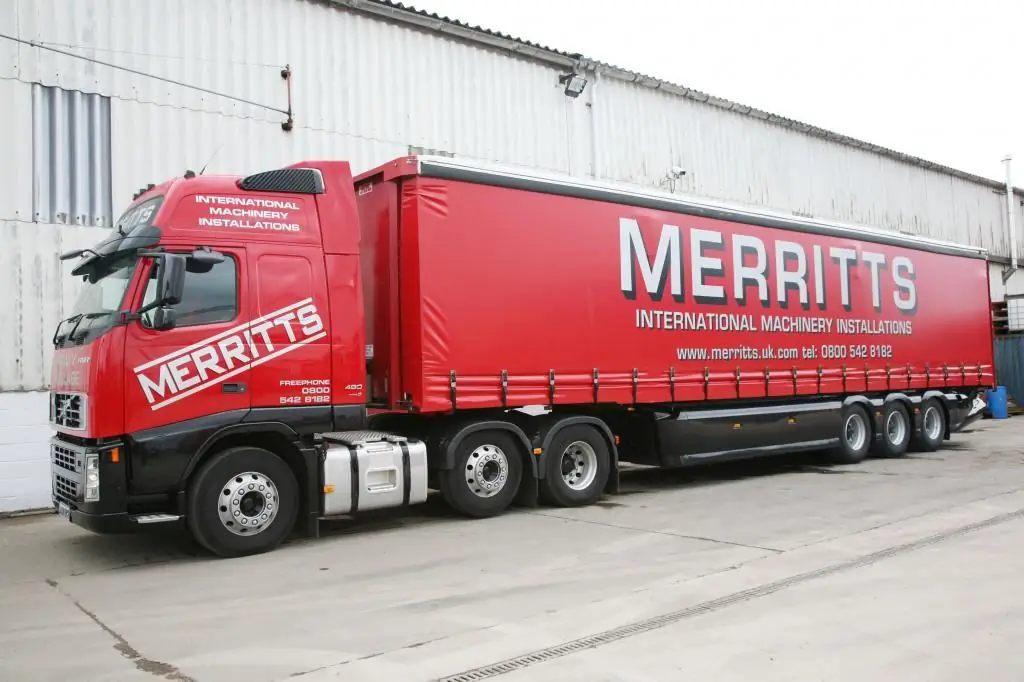
Bugün inşaatta şu tür ulaşım araçları kullanılmaktadır: kara, hava, deniz. Çoğu zaman, kullanılan yer ekipmanıdır. Tüm taşımaların yaklaşık %90'ı bu tür taşımalarla gerçekleştirilmektedir. Kara taşıtları arasında otomobil, traktör ve demiryolu taşımacılığı aktif olarak kullanılmaktadır
Arma cihazları, araçları ve mekanizmaları
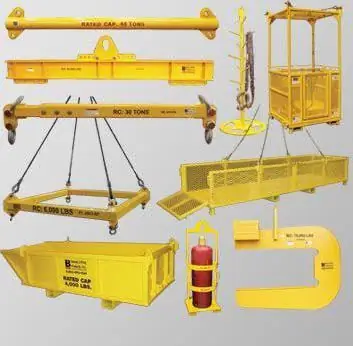
Herhangi bir endüstriyel üretim, bir dereceye kadar, büyük boyutlu ve karmaşık malların kurulumuyla ilişkilidir. Çoğu durumda, bir kişi bu işi kendi başına yapamaz. Bunun için arma araçları, mekanizmaları ve cihazları kullanılır
Engellere yönelik mühendislik araçları: açıklama, teknik özellikler, özellikler, fotoğraflar
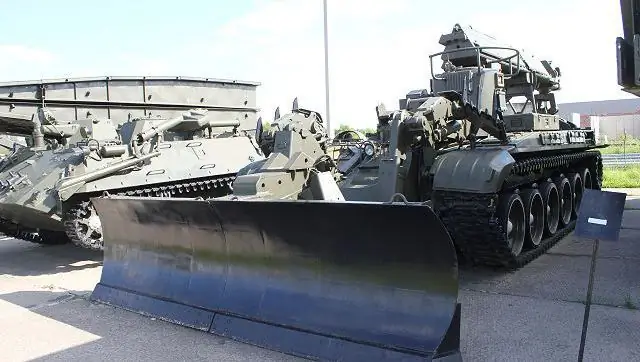
Mühendislik Engel Aracı veya kısaca WRI, bir orta tank temelinde oluşturulmuş bir tekniktir. Temel, T-55 idi. Böyle bir birimin temel amacı, yolların engebeli araziye döşenmesidir. Ek olarak, örneğin nükleer silahların kullanımından sonra sütun yolunu donatmak için kullanılabilir