2025 Yazar: Howard Calhoun | [email protected]. Son düzenleme: 2025-01-24 13:26
Demir cevheri olağan şekilde elde edilir: açık ocak veya yer altı madenciliği ve ardından malzemenin ezildiği, yıkandığı ve işlendiği ilk hazırlık için nakliye.
Cevher bir yüksek fırına dökülür ve sıcak hava ve ısı ile püskürtülür, bu da onu erimiş demire dönüştürür. Daha sonra fırının altından pik demir üretmek için soğutulduğu pik olarak bilinen kalıplara çıkarılır. Çeşitli şekillerde dövme demire dönüştürülür veya çeliğe işlenir.
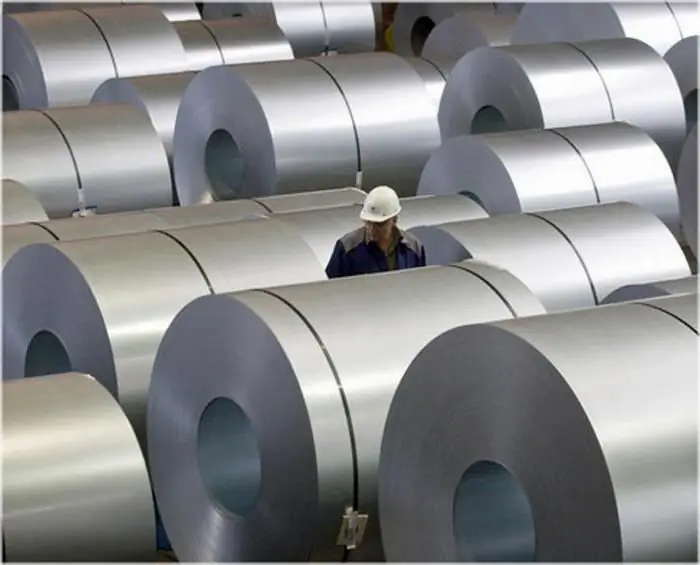
Çelik nedir?
Başlangıçta demir vardı. Yerkabuğundaki en yaygın metallerden biridir. Cevher formunda diğer birçok elementle birlikte hemen hemen her yerde bulunabilir. Avrupa'da demir işçiliği MÖ 1700'e kadar uzanır
1786'da Fransız bilim adamları Berthollet, Monge ve Vandermonde, demir, dökme demir ve çelik arasındaki farkın farklı karbon içeriğinden kaynaklandığını doğru bir şekilde belirlediler. Bununla birlikte, demirden yapılan çelik, hızla Sanayi Devrimi'nin en önemli metali haline geldi. 20. yüzyılın başında dünya çelik üretimi 28 idi.milyon ton - bu 1880'den altı kat daha fazla. Birinci Dünya Savaşı'nın başlangıcında, üretimi 85 milyon tondu. Birkaç on yıl boyunca pratik olarak demirin yerini aldı.
Karbon içeriği metalin özelliklerini etkiler. İki ana çelik türü vardır: alaşımlı ve alaşımsız. Çelik alaşımı, demire eklenen karbon dışındaki kimyasal elementleri ifade eder. Bu nedenle, paslanmaz çelik oluşturmak için %17 krom ve %8 nikel alaşımı kullanılır.
Şu anda, bireysel ihtiyaçları karşılamak için oluşturulanlar hariç, kataloglanmış 3000'den fazla marka (kimyasal bileşim) vardır. Hepsi çeliğin geleceğin zorlukları için en uygun malzeme olmasına katkıda bulunur.
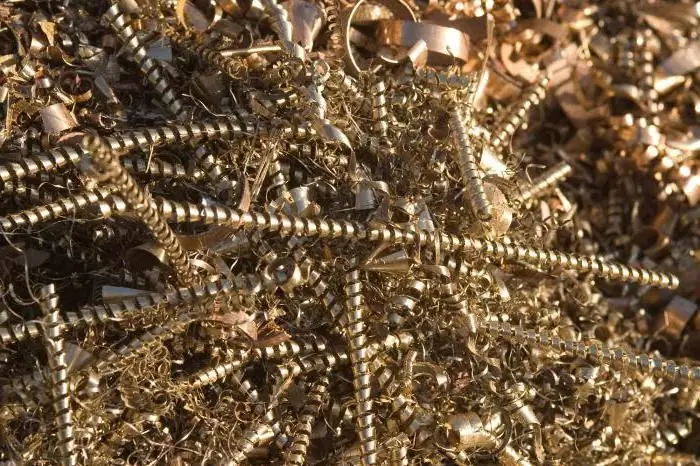
Çelik üretimi hammaddeleri: birincil ve ikincil
Bu metali birçok bileşen kullanarak eritmek en yaygın madencilik yöntemidir. Yük malzemeleri hem birincil hem de ikincil olabilir. Yükün ana bileşimi, kural olarak, %55 pik demir ve kalan hurda metalin %45'idir. Alaşımın ana elementi olarak ferro alaşımlar, dönüştürülmüş dökme demir ve ticari olarak saf metaller kullanılır, kural olarak her türlü demirli metal ikincil olarak sınıflandırılır.
Demir cevheri, demir çelik endüstrisindeki en önemli ve temel hammaddedir. Bir ton pik demir üretmek için bu malzemeden yaklaşık 1,5 ton gerekir. Bir ton pik demir üretmek için yaklaşık 450 ton kok kullanılmaktadır. birçok demirhanekömür bile kullanılıyor.
Su, demir çelik sektörü için önemli bir hammaddedir. Esas olarak kok söndürme, yüksek fırın soğutma, kömür fırını kapısı buhar üretimi, hidrolik ekipman çalışması ve atık su bertarafı için kullanılır. Bir ton çelik üretmek için yaklaşık 4 ton hava gerekir. Eritme cevherinden kirleticileri çıkarmak için yüksek fırında eritken kullanılır. Kireçtaşı ve dolomit, çıkarılan safsızlıklarla birleşerek cüruf oluşturur.
Refrakterlerle kaplı hem yüksek hem de çelik fırınlar. Demir cevheri eritme amaçlı kaplama fırınlarında kullanılırlar. Kalıplama için silikon dioksit veya kum kullanılır. Demir dışı metaller çeşitli kalitelerde çelik üretmek için kullanılır: alüminyum, krom, kob alt, bakır, kurşun, manganez, molibden, nikel, kalay, tungsten, çinko, vanadyum, vb. Tüm bu ferro alaşımlar arasında manganez çelik yapımında yaygın olarak kullanılmaktadır..
Sökülen fabrika yapılarından, makinelerden, eski araçlardan vb. kaynaklanan demir atıkları geri dönüştürülür ve endüstride yaygın olarak kullanılır.
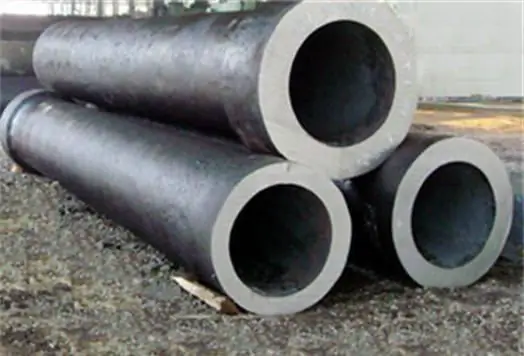
Çelik için demir
Dökme demir ile çelik eritme, diğer malzemelerden çok daha yaygındır. Dökme demir, genellikle gri demire atıfta bulunan bir terimdir, ancak aynı zamanda büyük bir ferroalyaj grubuyla da tanımlanır. Karbon, alaşımda ağırlıkça yaklaşık %2.1 ila 4'ünü oluştururken, silikon tipik olarak ağırlıkça %1 ila 3'tür.
Demir ve çelik eritme belirli bir sıcaklıkta gerçekleşir.saf demirin erime noktasından yaklaşık 300 derece daha düşük olan 1150 ile 1200 derece arasındaki erime noktası. Dökme demir ayrıca iyi akışkanlık, mükemmel işlenebilirlik, deformasyona, oksidasyona ve döküme karşı direnç gösterir.
Çelik aynı zamanda değişken karbon içeriğine sahip bir demir alaşımıdır. Çeliğin karbon içeriği kütle olarak %0,2 ila 2,1'dir ve demir için en ekonomik alaşım malzemesidir. Çeliğin dökme demirden eritilmesi, çeşitli mühendislik ve yapısal amaçlar için kullanışlıdır.
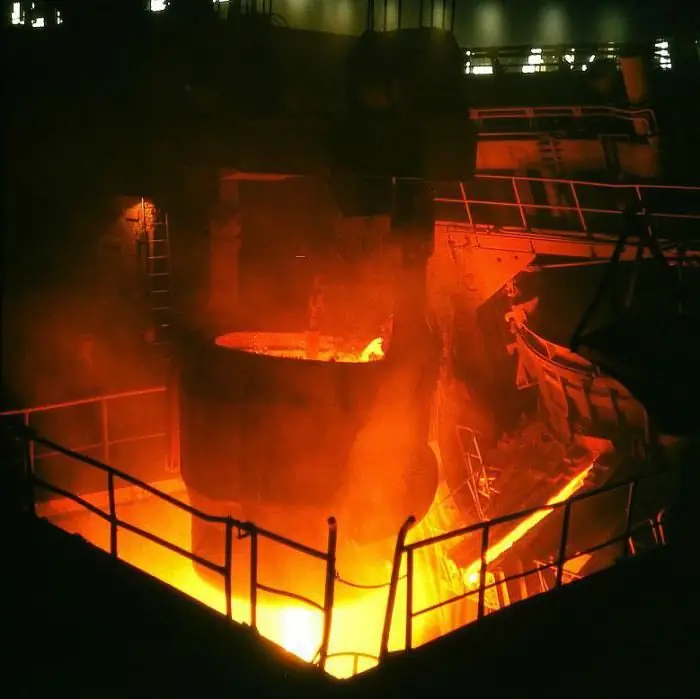
Çelik için demir cevheri
Çelik yapma süreci demir cevherinin işlenmesiyle başlar. Demir cevheri içeren kaya ezilir. Cevher, manyetik silindirler kullanılarak çıkarılır. İnce taneli demir cevheri, yüksek fırında kullanılmak üzere kaba taneli topaklar halinde işlenir. Kömür, neredeyse saf bir karbon formu üretmek için bir kok fırınında rafine edilir. Demir cevheri ve kömür karışımı daha sonra erimiş demir veya çeliğin yapıldığı pik demir üretmek için ısıtılır.
Ana oksijen fırınında, erimiş demir cevheri ana hammaddedir ve çeşitli derecelerde çelik üretmek için çeşitli miktarlarda hurda çelik ve alaşımlarla karıştırılır. Bir elektrik ark ocağında, geri dönüştürülmüş çelik hurdası doğrudan yeni çeliğe eritilir. Çeliğin yaklaşık %12'si geri dönüştürülmüş malzemeden yapılmıştır.
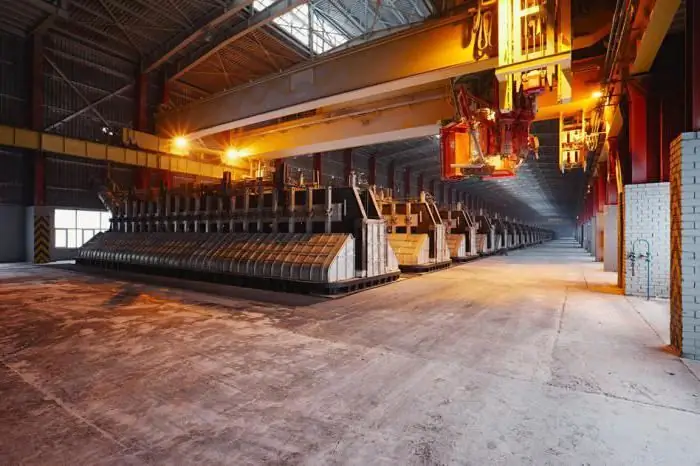
Ergitme teknolojisi
Ergitme, bir metalin bir element şeklinde elde edildiği bir işlemdir.genellikle hava gibi oksitleyici ajanların veya kok gibi indirgeyici ajanların mevcudiyetinde erime noktasının üzerinde ısıtılarak cevherinden basit bir bileşik olarak.
Çelik üretim teknolojisinde, oksijen ile birleşen demir oksit gibi metal, yüksek bir sıcaklığa ısıtılır ve oksit, karbon monoksit veya karbon olarak salınan yakıtta karbon ile kombinasyon halinde oluşur. dioksit. Toplu olarak damarlar olarak adlandırılan diğer safsızlıklar, cüruf oluşturmak üzere birleştikleri bir akış eklenerek çıkarılır.
Modern çelik üretimi, yankılı bir fırın kullanır. Konsantre cevher ve akıntı (genellikle kireçtaşı) üstte yüklenirken, erimiş mat (bakır, demir, kükürt ve cüruf bileşiği) alttan çekilir. Mat yüzeyden demiri çıkarmak için bir dönüştürücü fırınında ikinci bir ısıl işlem gereklidir.
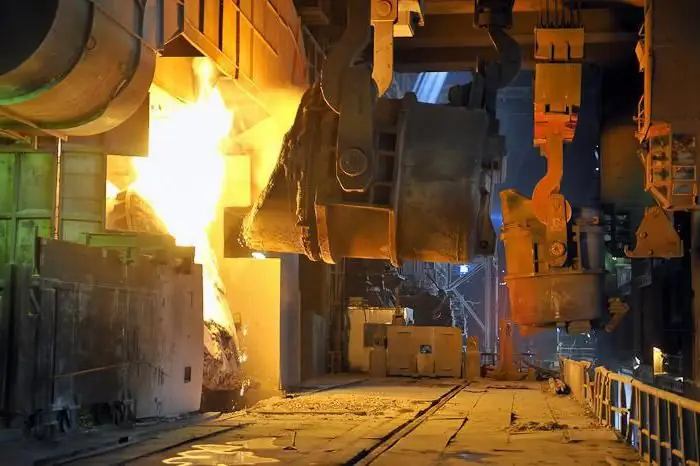
Oksijen konvektör yöntemi
BOF süreci, dünyanın önde gelen çelik üretim sürecidir. 2003 yılında dünya konvertör çeliği üretimi 964.8 milyon ton veya toplam üretimin %63.3'üne ulaştı. Konvertör üretimi bir çevre kirliliği kaynağıdır. Bunun temel sorunları emisyonların, deşarjların ve atıkların az altılmasıdır. Özleri, ikincil enerji ve maddi kaynakların kullanımında yatar.
Egzotermik ısı, blöf sırasında oksidasyon reaksiyonları ile üretilir.
Kendi teknolojimizi kullanarak çelik üretiminin ana sürecihisse senetleri:
- Bir yüksek fırından çıkan erimiş demir (bazen sıcak metal olarak adlandırılır), pota adı verilen büyük, ateşe dayanıklı astarlı bir kaba dökülür.
- Potadaki metal doğrudan ana çelik üretimine veya ön işlem aşamasına gönderilir.
- 700-1000 kilopaskal basınçta yüksek saflıkta oksijen, bir kapta asılı duran ve banyonun birkaç fit yukarısında tutulan su soğutmalı bir mızrak vasıtasıyla demir banyosunun yüzeyine süpersonik hızda enjekte edilir.
Ön işlem kararı, sıcak metalin kalitesine ve istenen nihai çelik kalitesine bağlıdır. Sökülebilen ve onarılabilen ilk çıkarılabilir alt dönüştürücüler hala kullanımda. Üfleme için kullanılan mızraklar değiştirildi. Üfleme sırasında mızrağın sıkışmasını önlemek için uzun sivrilen bakır uçlu oluklu bilezikler kullanılmıştır. Ucun uçları, yanmadan sonra, CO2 içine üflendiğinde oluşan CO'yu yakar ve ek ısı sağlar. Cürufları uzaklaştırmak için dart, refrakter toplar ve cüruf dedektörleri kullanılır.
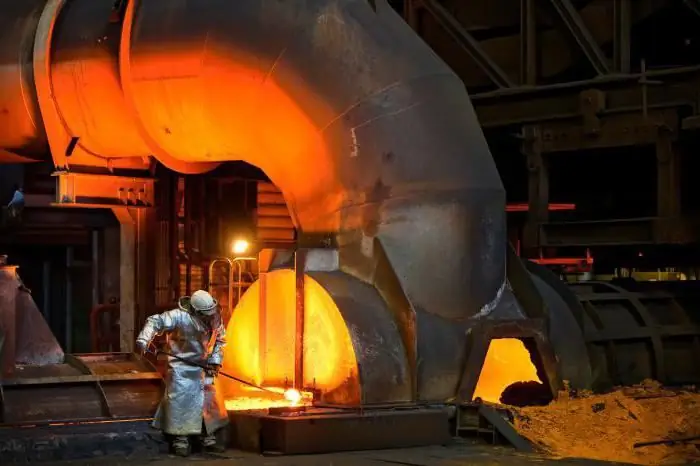
Oksijen konvektör yöntemi: avantajlar ve dezavantajlar
Toz oluşumu yani demirin buharlaşması 3 kat azaldığı için gaz arıtma ekipmanı maliyeti gerektirmez. Demir verimindeki azalmaya bağlı olarak sıvı çelik veriminde %1,5 - %2,5 oranında bir artış gözlenir. Avantajı, bu yöntemde üfleme yoğunluğunun artmasıdır, bu dadönüştürücünün performansını% 18 artırma yeteneği. Tahliye bölgesindeki sıcaklık daha düşük olduğundan çeliğin kalitesi daha yüksektir, bu da daha az nitrojen oluşumuna neden olur.
Bu çelik eritme yönteminin eksiklikleri, yüksek yakıt yanması tüketimi nedeniyle oksijen tüketimi seviyesi %7 arttığı için tüketim talebinde düşüşe neden oldu. Geri dönüştürülmüş metalde artan bir hidrojen içeriği vardır, bu nedenle işlemin sona ermesinden sonra oksijenle temizlemenin gerçekleştirilmesi biraz zaman alır. Tüm yöntemler arasında oksijen dönüştürücü en yüksek cüruf oluşumuna sahiptir, bunun nedeni ekipman içindeki oksidasyon sürecinin izlenememesidir.
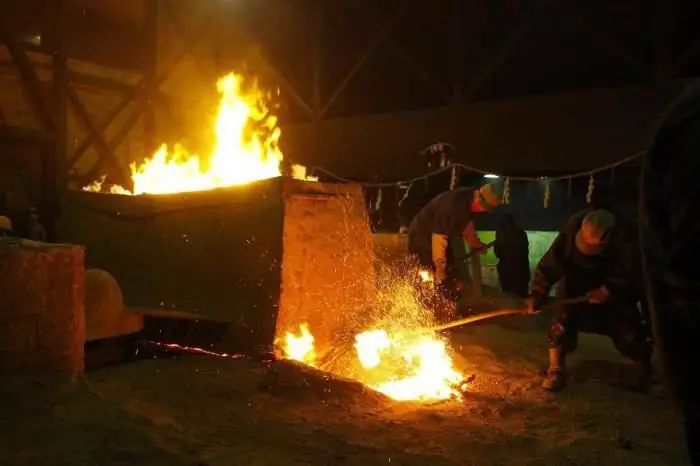
Açık ocak yöntemi
20. yüzyılın çoğu için açık ocak süreci, dünyada üretilen tüm çeliğin işlenmesinin ana parçasıydı. 1860'larda William Siemens, metalürjik bir fırında sıcaklığı yükseltmenin bir yolunu aradı ve fırın tarafından üretilen atık ısıyı kullanmak için eski bir öneriyi yeniden canlandırdı. Tuğlayı yüksek bir sıcaklığa kadar ısıttı, ardından fırına hava vermek için aynı yolu kullandı. Önceden ısıtılmış hava alevin sıcaklığını önemli ölçüde artırdı.
Yakıt olarak doğal gaz veya atomize ağır yağlar kullanılır; yanmadan önce hava ve yakıt ısıtılır. Fırın, demir cevheri, kalker, dolomit ve flux ile birlikte sıvı pik demir ve çelik hurda ile yüklenir.
Sobanın kendisimanyezit ocak tuğlaları gibi oldukça refrakter malzemeler. Açık ocak fırınları 600 tona kadar ağırlığa sahiptir ve genellikle gruplar halinde kurulur, böylece fırınları doldurmak ve sıvı çeliği işlemek için gereken devasa yardımcı ekipman etkin bir şekilde kullanılabilir.
Açık ocak işlemi, çoğu sanayileşmiş ülkede neredeyse tamamen bazik oksijen işlemi ve elektrik ark ocağı ile değiştirilmiş olsa da, dünya çapında üretilen tüm çeliğin yaklaşık 1/6'sını oluşturur.
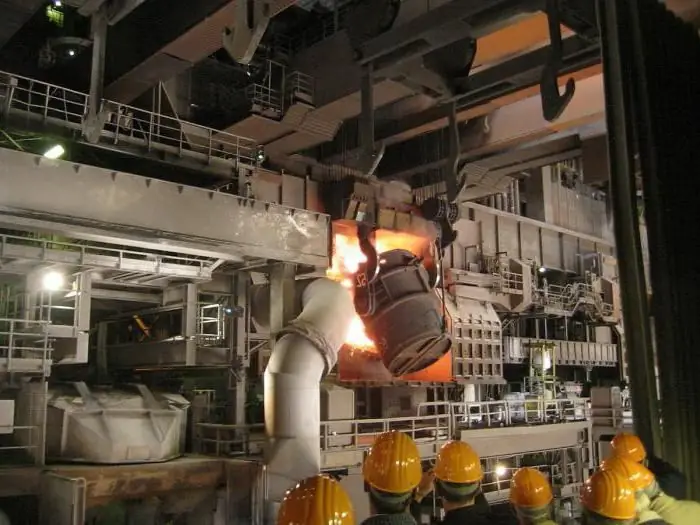
Bu yöntemin avantajları ve dezavantajları
Avantajları arasında kullanım kolaylığı ve malzemeye çeşitli özel özellikler kazandıran çeşitli katkı maddeleri içeren alaşımlı çeliğin üretim kolaylığı yer alır. Gerekli katkı maddeleri ve alaşımlar, ergitme bitmeden hemen önce eklenir.
Dezavantajları arasında oksijen dönüştürücü yöntemine kıyasla düşük verimlilik sayılabilir. Ayrıca çeliğin kalitesi diğer metal eritme yöntemlerine göre daha düşüktür.
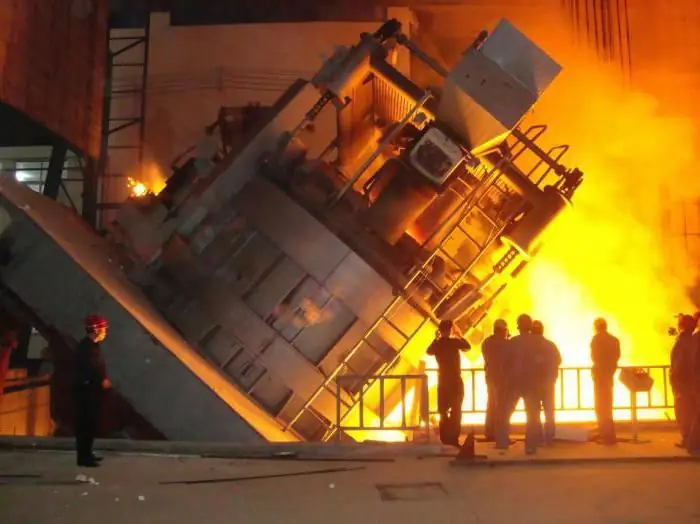
Elektrikli çelik üretim yöntemi
Çeliği kendi rezervlerimizi kullanarak eritmenin modern yöntemi, yüklü bir malzemeyi elektrik arkıyla ısıtan bir fırındır. Endüstriyel ark ocaklarının boyutları, yaklaşık bir ton kapasiteli küçük birimlerden (dökümhanelerde demir ürünleri üretimi için kullanılır) ikincil metalurjide kullanılan 400 tonluk birimlere kadar değişir.
Ark fırınları,araştırma laboratuvarlarında kullanılan sadece birkaç on gramlık bir kapasiteye sahip olabilir. Endüstriyel elektrik ark ocağı sıcaklıkları 1800 °C'ye (3, 272 °F) ulaşabilirken, laboratuvar kurulumları 3000 °C'yi (5432 °F) aşabilir.
Ark fırınları, şarj malzemesinin doğrudan bir elektrik arkına maruz kalması ve terminallerdeki akımın yüklü malzemeden geçmesiyle endüksiyon fırınlarından farklıdır. Elektrik ark ocağı çelik üretimi için kullanılır, genellikle su soğutmalı, büyük boyutlu, geri çekilebilir bir çatı ile kaplanmış refrakter bir astardan oluşur.
Fırın temel olarak üç bölüme ayrılmıştır:
- Yan duvarlar ve alt çelik kaseden oluşan kabuk.
- Ocak, alt hazneyi dışarı çeken bir refrakterden oluşur.
- Refrakter astarlı veya su soğutmalı çatı, top kesitli veya kesik koni (konik kesitli) olarak yapılabilir.
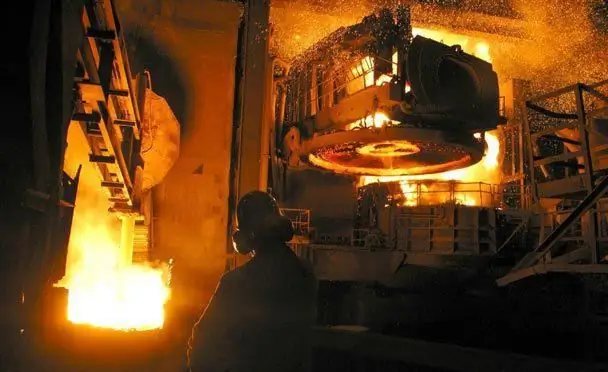
Yöntemin avantajları ve dezavantajları
Bu yöntem, çelik üretimi alanında lider konumdadır. Çelik eritme yöntemi, kükürt, fosfor ve oksijen gibi istenmeyen safsızlıkları ya tamamen içermeyen ya da az miktarda içeren yüksek kaliteli metal oluşturmak için kullanılır.
Yöntemin ana avantajı, ısıtma için elektriğin kullanılmasıdır, böylece erime sıcaklığını kolayca kontrol edebilir ve inanılmaz bir metal ısıtma hızı elde edebilirsiniz. Otomatik çalışma olacakçeşitli hurda metallerin yüksek kalitede işlenmesi için mükemmel fırsata hoş bir katkı.
Dezavantajları arasında yüksek güç tüketimi bulunur.
Önerilen:
Gıda paslanmaz çelik: GOST. Gıda sınıfı paslanmaz çelik nasıl belirlenir? Gıda paslanmaz çelik ile teknik paslanmaz çelik arasındaki fark nedir?

Makale, gıda sınıfı paslanmaz çelik kalitelerinden bahsediyor. Gıda paslanmaz çeliğini teknikten nasıl ayırt edeceğinizi okuyun
Et işleme tesislerinde sığır kesimi: kurallar, teknoloji, yöntemler ve yöntemler
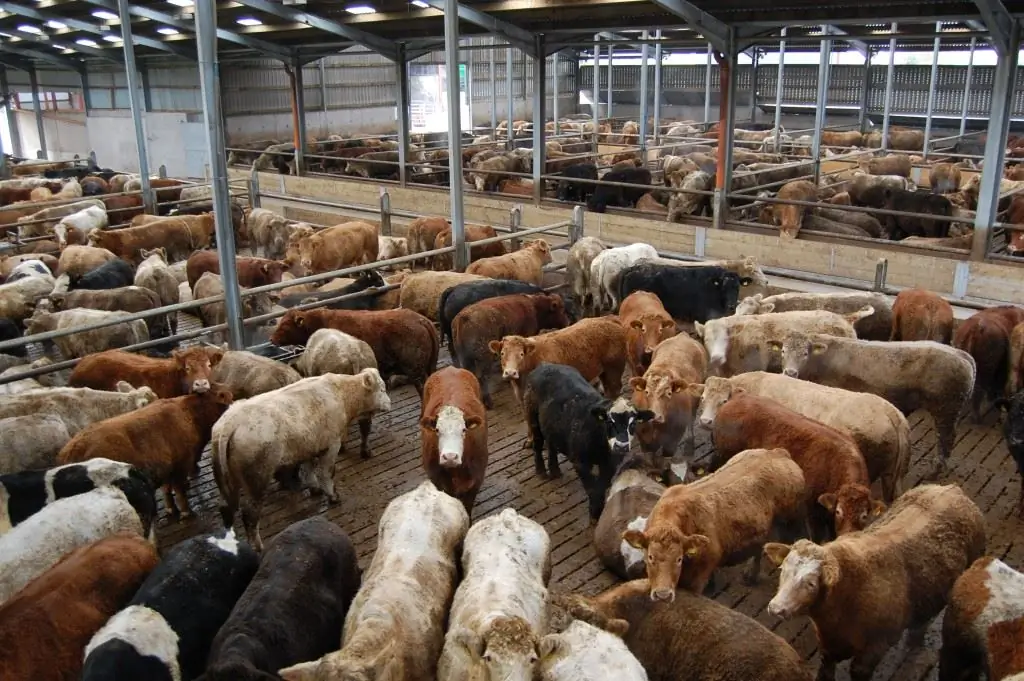
Tüketici sepetine doğrudan et ürünleri sağlanması, sığırların kesilmesine ve işlenmesine bağlıdır. Lezzetli sığır eti ve dana eti yemekleri, büyük ölçüde, boğaları ve inekleri nasıl düzgün bir şekilde keseceğini bilen hayvan yetiştiricilerinin meziyetidir. Sığır kesimi için yüksek kaliteli et ürünleri elde etmeyi mümkün kılan çeşitli teknolojiler, yöntemler ve yöntemler vardır
Korozyona dayanıklı çelik. Çelik kaliteleri: GOST. Paslanmaz çelik - fiyat
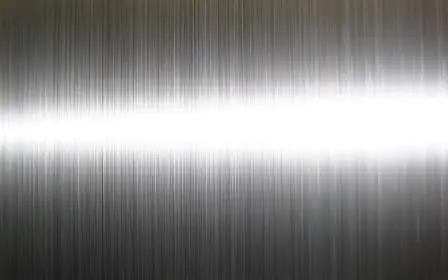
Metal malzemeler neden bozulur? Korozyona dayanıklı çelikler ve alaşımlar nelerdir. Paslanmaz çelik mikroyapı tipine göre kimyasal bileşimi ve sınıflandırılması. Fiyatlandırmayı etkileyen faktörler. Çelik kalite belirleme sistemi (GOST gereksinimleri). Uygulama alanı
Poliüretan köpük üretimi: teknoloji, hammaddeler, ekipman
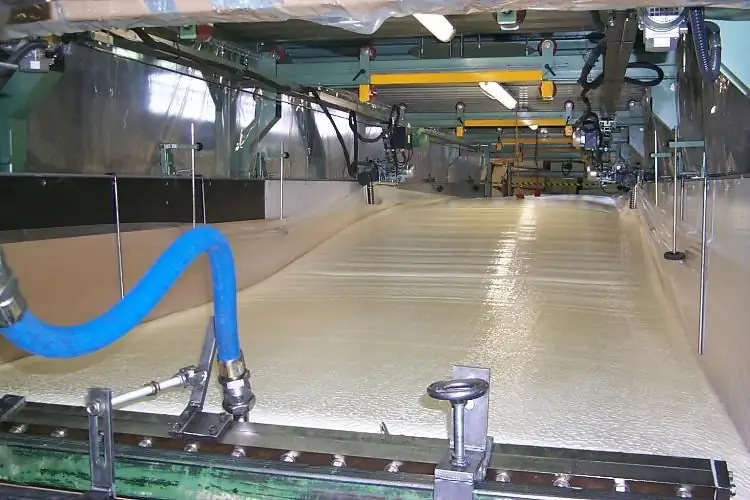
Pencere açıklıklarını kapatmanın olağan yollarından montaj köpüğü, uzun zamandır çeşitli iş türlerinde yaygın olarak kullanılan tam teşekküllü bir yapı malzemesi durumuna geçmiştir. Bu ürünün uygulama çeşitliliği, üretim teknolojilerine farklı bir yaklaşıma olan ihtiyacı da belirler. Bununla birlikte, poliüretan köpüğün üretim yöntemlerindeki farklılıklar, temel teknolojik süreçleri etkilemeden daha çok kozmetik niteliktedir
440 çelik - paslanmaz çelik. Çelik 440: özellikler
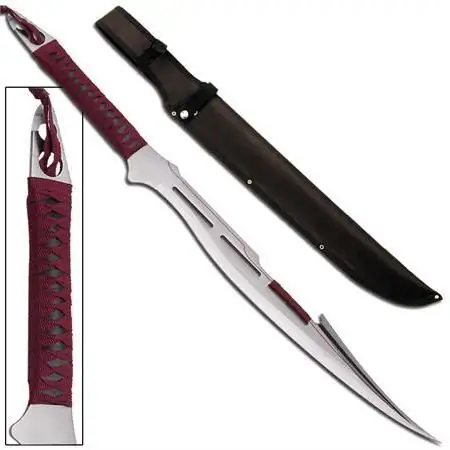
Birçok insan 440 çeliği bilir. Çeşitli amaçlar için bıçak imalatında sıklıkla kullanılan, güvenilir, korozyon önleyici, zamanla test edilmiş sert bir malzeme olarak kendini kanıtlamıştır. Bu alaşımın sırrı nedir? Kimyasal, fiziksel özellikleri ve uygulamaları nelerdir?