2025 Yazar: Howard Calhoun | [email protected]. Son düzenleme: 2025-01-24 13:27
Kaynak ve yüzey kaplama teknolojileri, ürünün yüksek derecede güvenilirliğini ve dayanıklılığını sağlayarak metal parçaların etkin bir şekilde eski haline getirilmesini mümkün kılar. Bu, araba onarımlarından haddelenmiş metal üretimine kadar çeşitli alanlarda onarım işlemleri gerçekleştirirken bu yöntemlerin kullanılması uygulamasıyla doğrulanır. Metal yapıların onarımı ile ilgili toplam çalışma miktarında, parçaların kaynak ve yüzey kaplama ile restorasyonu yaklaşık% 60-70'dir. Çelik silindir bloklarının, motor millerinin, karterlerin, zincir bağlantılarının, bıçakların vb. en yaygın onarımı.
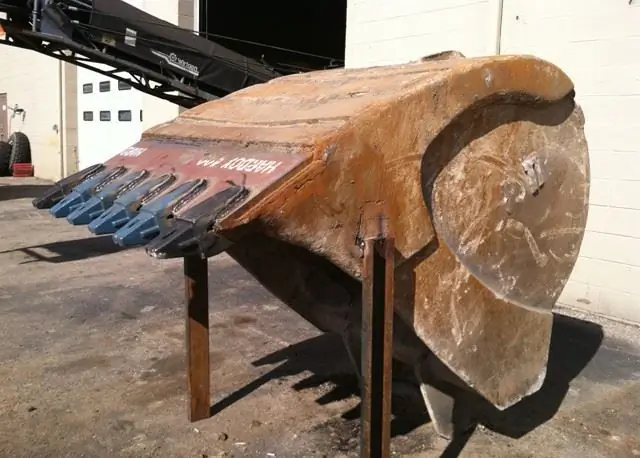
Tamir ve restorasyon işlerinde kaynak ve yüzey kaplama
Her iki yöntem de farklı parametrelere sahip ısıl işlem yöntemlerine dayanmaktadır.bağlı ekipmanın çalışması. Kaynak, bir parçanın farklı elemanlarını bağlamak, teknolojik boşlukları kapatmak ve yüzeydeki küçük kusurları ortadan kaldırmak için kullanılabilen atomlar arası bağların oluşum süreci olarak anlaşılır. Kaynak işlemi için enerji potansiyeli, iş parçasının genel veya lokal ısınması ile sağlanır.
Bu tür tipik işlemler arasında plakaların, jantların ve burçların ek veya kırık parçalarının sabitlenmesi yer alır. Basit geometrik şekillere sahip ürünlerin onarımına ek olarak, diğer teknolojik işlemlerin bir parçası olarak daha karmaşık restorasyon görevleri de mümkündür. Örneğin, kaynakla diş restorasyonu, mekanik düzeltme ve tornalama prosedürleriyle desteklenecektir. Ek olarak, bu tür çalışmalarda, doğrudan diş düzeltme ile ilgili olan, kalıplar gibi yardımcı bir aletin aşırı ısınması için gerekliliklere uyulmalıdır.
Yüzey kaplamaya gelince, bu yöntem, restore edilecek yüzeye ek bir metal kaplamanın uygulanmasını içerir. Yeni teknolojik katman, aşınmış parçaları onarırken veya sürtünme alanındaki yüzeyi güçlendirirken faydalı olabilir.
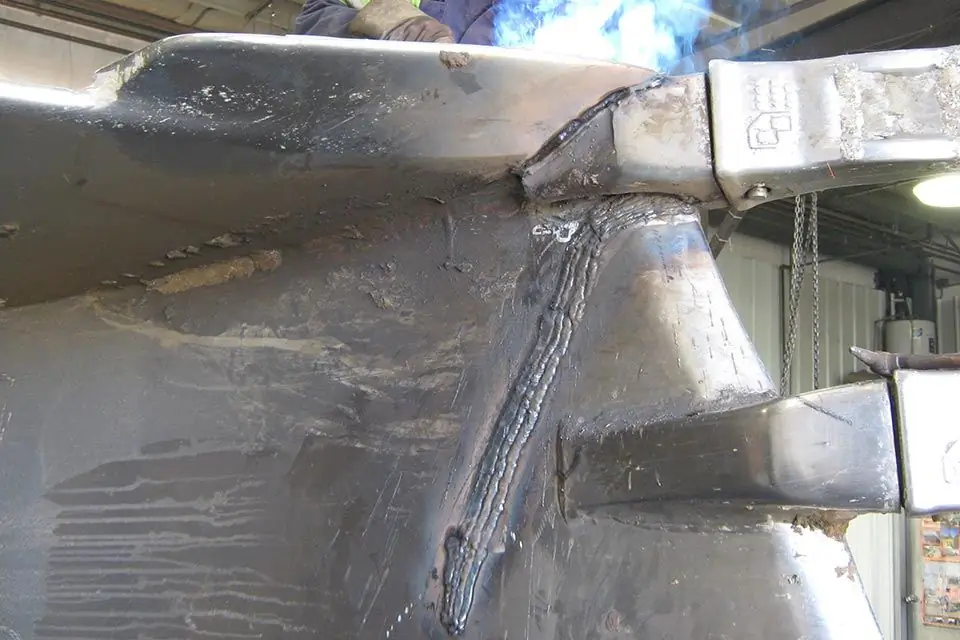
Uygulamalı Ekipman
Kaynak yaparken mutlaka bir güç kaynağı, parçayı tutacak ve arkı yönlendirecek ekipman kullanılır. Daha sık olarak, 70 ila 800 A DC jeneratörlü bir motor içeren bir kaynak dönüştürücü kullanılır. Transformatörlü doğrultucular da kullanılabilir.akım ve kontrol dişlisi. Sarf malzemeleri ve yardımcı cihazlardan bahsedersek, parçaların kaynak ve yüzey kaplaması ile restorasyonu, tutucu ağızlıkların, elektrotların ve soğutma sistemlerinin bağlantısı ile gerçekleştirilir. Yüzey kaplama sırasında, takım tezgahlarına (tornalar veya vidalı kesme) montaja izin veren kaliperler ve kaldırıcılar ile deforme kafalar da kullanılır. Fazla metal kenarları ve katmanları çıkarmak için özel kesiciler kullanılır.
Parça hazırlama gereksinimleri
Hem kaynakta hem de yüzey kaplama işleminde, işlemin kalitesi büyük ölçüde iş parçasının ilk durumuna göre belirlenecektir. Parçanın yüzeyleri pas, kireç, kir ve yağdan temizlenmelidir. Aksi takdirde, penetrasyon eksikliği, çatlaklar ve cüruf kalıntılarının kalma riski artar. Fabrika ve konservasyon yağlarından yağ alma işlemlerine özellikle dikkat edilmelidir. Bu prosedür sıcak bir solüsyonda gerçekleştirilir, ardından ürün yıkanır ve kurutulur. Parçaları kaynak yaparak geri yüklemeden önce, onarımın kalitesini artıran kumlama yapılması önerilir. Bu tür görevler için kompresör ekipmanı, taşlama diskleri ve kesicilerin bağlantısı ile aşındırıcı işleme yöntemleri kullanılır. Hafif korozyon hasarı izleri de manuel metal fırçalarla temizlenebilir.
Kurtarma için hangi elektrotlar kullanılır?
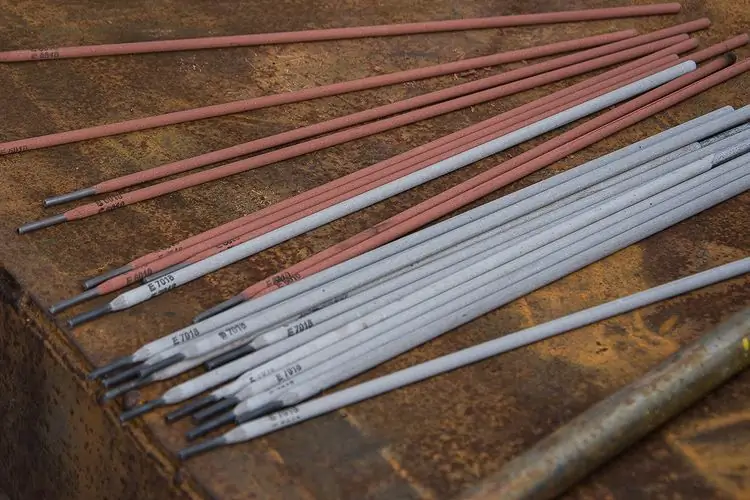
Ana çalışma ekipmanını ve iş parçasını hazırladıktan sonra elektrot seçimine geçebilirsiniz. Seçim, metalin türüne, kusurun doğasına vekaplama katmanı için gereksinimler. Kural olarak, yaygın kırılma ve çatlak durumlarında, yaklaşık 4 MPa'lık bir çekme mukavemetine sahip geleneksel kaynak elektrotları kullanılır. Karbon çelikleriyle çalışmak için, çubukları 1.5-12 mm kalınlığında Sv-08 tel kalitesinden yapılmış sarf malzemelerinin kullanılması tavsiye edilir. Kaplamanın özelliklerini göz ardı etmeyin. E-34 tipi elektrotun tebeşirle kaplanması ile parçaların kaynak ve yüzey kaplama ile restorasyonunda yüksek stabilizasyon etkisi sağlanacaktır. Yoğun ve düzgün bir dikiş oluşturmanıza olanak sağlayacak kararlı bir ark yakma işlemine katkıda bulunacaktır.
Bant ve boru şeklindeki toz elemanlar gibi standart olmayan elektrot sarf malzemeleri de günümüzde kullanılmaktadır. Genellikle 0,8 mm kalınlığa kadar haddelenmiş metal şeritlerdir ve yüzeyleri ferromangan, stalinit, vb. bazlı çeşitli toz alaşım karışımları ile doldurulur. Bu tür elektrotlar, onarılan alana ek operasyonel özellikler kazandırılması planlanıyorsa ele alınmalıdır.
Manuel ark kaynağı ve yüzey kaplama yöntemi
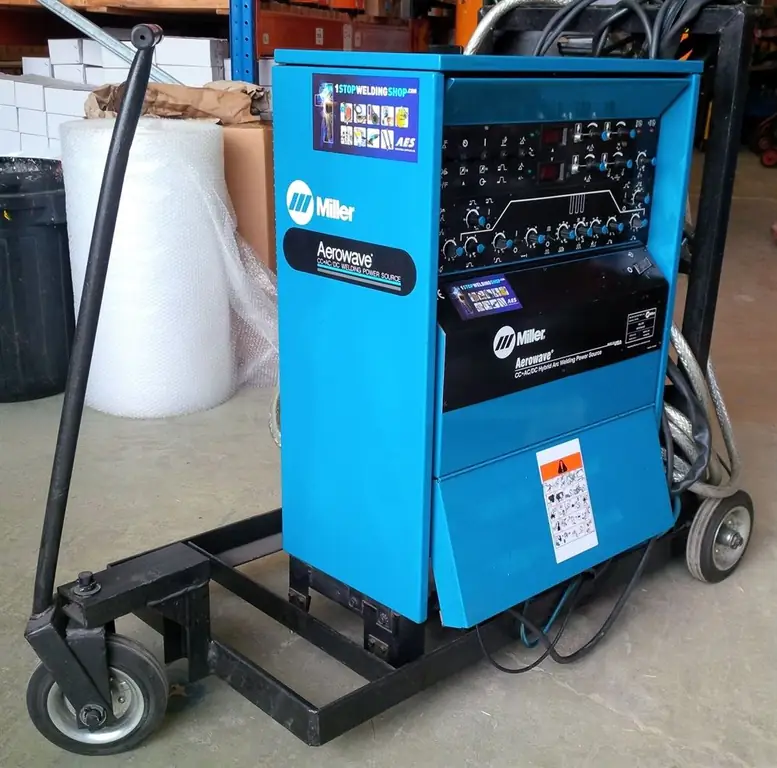
Hasarlı kaynakları onarırken, çatlakları kapatırken ve hermetik kasaları kapatırken grafit, karbon veya tungsten elektrotlarla manuel yöntemi kullanabilirsiniz. Çalışma sırasında, kaplamalı bir çubuk demeti alınır ve tel ile sabitlenir. Uçlar önceden kaynaklanmalı ve hazırlanan tutucuya yerleştirilmelidir. Çalışma sırasında elektrotlar, geniş bir etki alanına sahip, sözde dolaşan bir ark oluşturacaktır. NasılHasarlı alan ne kadar büyükse, kiriş o kadar büyük olmalıdır. Kaynak işleminin bu şekilde ana zorluğu, üç fazlı bir ağın bağlanması ihtiyacında yatmaktadır, çünkü 5-6 elektrotlu bir ışın ile aynı yüzey, artan bir akımda gerçekleştirilmelidir. Bu yöntem, orta ve büyük kalınlıktaki alaşımlı ve düşük alaşımlı çeliklerden yapılmış parçaları onarmak için kullanılır.
Otomatik toz altı kaynak yöntemi
Otomatik yüzey kaplama işlemi, arkın kendisinin çalışma yüzeyi boyunca hareketi ile elektrot beslemesinin tamamen mekanize olması bakımından farklıdır. Akı da hedef bölgenin oksijenin zararlı etkilerinden izole edilmesini sağlar. Yöntem, 15 mm'ye kadar aşınma derinliğine sahip düz ve silindirik parçaların yüzeylerini eski haline getirmek için kullanılır. Kusurun boyutu arttıkça, birkaç katman sert dolgu uygulanabilir, ancak bu durumda önceki her katmanın polimerizasyonunu beklemek gerekli olacaktır. Parçaları kaynak ve yüzey kaplama ile geri yükleme teknolojisi, akım kaynaklarının bir vidalı torna tezgahı ile bir dönüştürücü veya doğrultucu şeklinde bağlanmasını gerektirir. Çalışma alanında 1-4 mm kalınlığında bir akı kaplaması oluşur, bundan sonra arklı bir elektrot teli otomatik olarak yönlendirilir. Bu yöntemin manuel kaynağa göre ana avantajları, sıçramanın bir sonucu olarak minimum metal kaybını içerir. Manuel yöntem birkaç kat daha fazla kül ve atık verir.
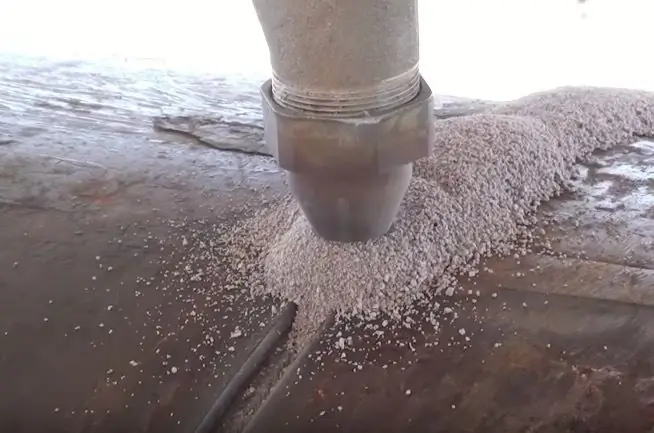
Vibro ark yüzey kaplama yöntemi
Bu durumda, işlemde olan eriyebilir elektrotlar kullanılır.yanan arklar kısa devrelerle titreşir. Sarf malzemelerinin tedarik edilmesi ve taşınması işlemleri de otomatikleştirilmiştir. Sürecin dış karmaşıklığına rağmen, yöntem oldukça basittir ve özel ekipman kullanımını gerektirmez. Ayrıca, uzun vadede, ısıl işlem uygulanmadan sertliğin korunmasıyla parçanın deformasyonunun hariç tutulması beklenebilir. Ancak, sınırlamalar da vardır. Bu nedenle, kaynak ve yüzey kaplama ile parçaları eski haline getirmek için titreşim yöntemleri, çapı en az 8 mm veya kalınlığı 0,5 ila 3,5 mm olan iş parçaları için uygundur. Teorik olarak, vibro-ark yüzey kaplaması, gaz veya akı ile çeşitli koruyucu ortamlarda gerçekleştirilebilir, ancak pratikte sıvı yalıtımı daha sık kullanılır - örneğin, soda külü çözeltisi.
Gaz koruyucu ortamlarda kaynak ve yüzey kaplama
Bu yöntem, sıkıştırılmış gaz karışımı ile özel bir silindirin hazırlanmasını içerir. Yüksek basınç altında kaynak bölgesine yönlendirilen argon ve karbondioksit gazları kullanılabilir. Karışımın görevi, iş parçasını havadaki nitrojen ve oksijenin olumsuz etkilerinden izole etme koruyucu işlevine de indirgenmiştir. Gazlı ortamda kaynak yapılarak en kaliteli derzler, çalışma alanına ayrı bir dolgu malzemesi girişi olan tungsten elektrotlar kullanılarak elde edilir. Yüzey kaplama, ters polarite ile doğru akım altında gerçekleştirilir. Bir elektrot teli kullanılırsa süreç mekanikleştirilebilir, ancak gaz-elektrik brülörleri genellikle manuel olarak işlenir.
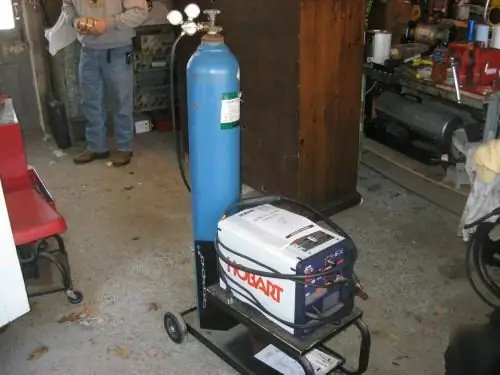
Yarı otomatik kaynak ve yüzey kaplama yöntemleri
Alüminyum ve çeşitli demir dışı alaşımlarla çalışmak için en uygun yöntem. Ekipman parametrelerinin esnek ayarı ve farklı koruyucu ortamlar kullanma olasılığı sayesinde operatör, düşük akım gücünde 12 mm kalınlığa kadar bir iş parçası üzerinde yüksek kaliteli bir dikiş elde edebilir. Parçaları kaynakla geri yüklemenin yarı otomatik yöntemi, 0,8-6 mm kalınlığında tungsten elektrotlar kullanılarak gerçekleştirilir. Bu durumda voltaj 20 ila 25 V arasında değişebilir ve akım gücü 120 A dahilindedir.
Alternatif Basınç Geri Kazanım Teknolojisi
Termal kaynak ve yüzey kaplama yöntemlerine ek olarak, metal boşlukların yapısını değiştirmek için çok çeşitli temas veya soğuk yöntemler de kullanılır. Özellikle, parçaların basınç altında kaynaklanarak restorasyonu, zımbalı mekanik üniteler kullanılarak gerçekleştirilir. Plastik deformasyon sürecinde, temas noktalarında belirli parametrelere sahip kaynaklı bir bağlantı oluşturulur. Deforme edici etkinin konfigürasyonu, zımbanın özelliklerine ve sıkıştırma tekniğine bağlı olacaktır.

Sonuç
Bugün, bir metal yapıdaki kusurları düzeltmenin kaynak ve yüzey kaplamadan daha etkili bir yolu yoktur. Başka bir şey, bu segmentlerde, teknolojinin pratikte uygulanması için çeşitli yöntemlerin aktif bir şekilde geliştirilmesidir. En umut verici yön, otomatik ekipman üzerinde kaynak ve yüzey kaplaması yaparak parçaların restorasyonu olarak adlandırılabilir. Onarım işlemlerinin mekanizasyonu, sürecin verimliliğini artırır,kaynakçı için ergonomi ve güvenlik seviyesi. Aynı zamanda, gaz koruyucu ortamın bağlantısıyla yüksek hassasiyetli argon ark kaynağı yöntemleri geliştirilmektedir. Bu yönde tam otomasyondan bahsetmek için henüz çok erken ancak sonucun kalitesi açısından bu alan ileri düzeyde.
Önerilen:
Atık yakma tesisi: teknolojik süreç. Moskova ve Moskova bölgesindeki atık yakma tesisleri
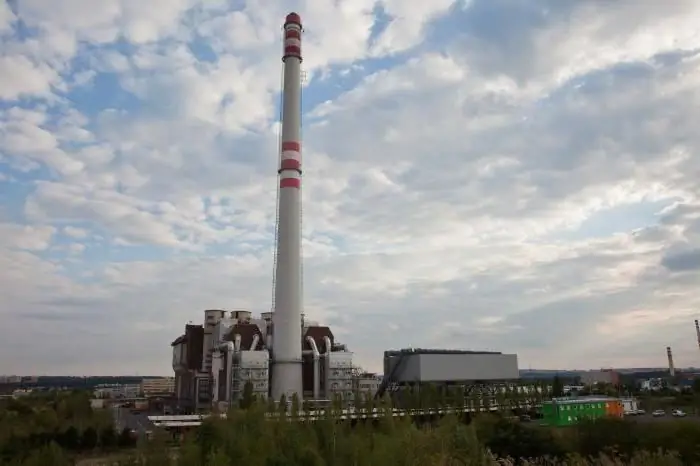
Atık yakma fırınları uzun zamandır tartışmalı. Şu anda, atıkları geri dönüştürmenin en ucuz ve en uygun fiyatlı yoludur, ancak en güvenli olmaktan çok uzaktır. Her yıl, Rusya'da bir yerden çıkarılması gereken 70 ton çöp ortaya çıkıyor. Fabrikalar bir çıkış yolu haline gelir, ancak aynı zamanda Dünya'nın atmosferi muazzam kirliliğe maruz kalır. Hangi atık yakma fırınları var ve Rusya'daki atık salgınını durdurmak mümkün mü?
Çeliğin yüzey sertleşmesi nedir? Yüzey sertleştirme ne için kullanılır?
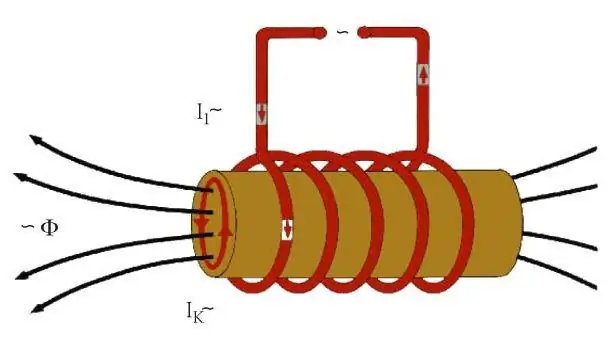
Bu makale metalurjiden uzak kişilere, gücün sıradan bir masa veya katlanır bıçaktaki iyi bir bıçaktan ne kadar farklı olduğu, yüzey sertleştirmenin toplu sertleştirmeden ve benzeri konularla ilgilenen amatörlere yöneliktir
Hat içi üretim Kavram, tanım, organizasyon yöntemleri ve teknolojik süreç
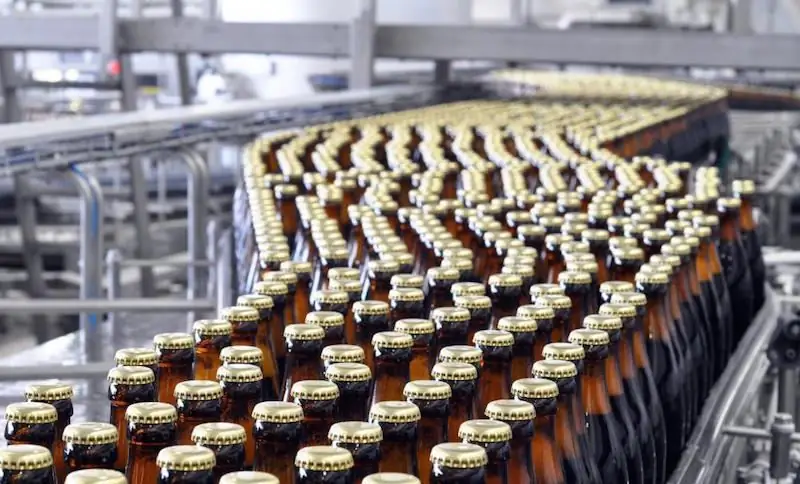
Üretim süreci, farklı şekillerde ve araçlarla düzenlenebilen karmaşık bir teknolojik eylemdir. Bir işletmenin hat içi ürün üretimi koşullarında çalışması bugün en verimli olarak kabul edilir, ancak aynı zamanda emek, organizasyon ve malzeme maliyetleri açısından talep edilir. Genel anlamda hat içi üretim, işlemlerin ritmi ve tekrarlanabilirliği ilkelerinin ön plana çıktığı bir üretim faaliyeti biçimidir
Kaplama Teknolojik Özellikler ve Faydalar
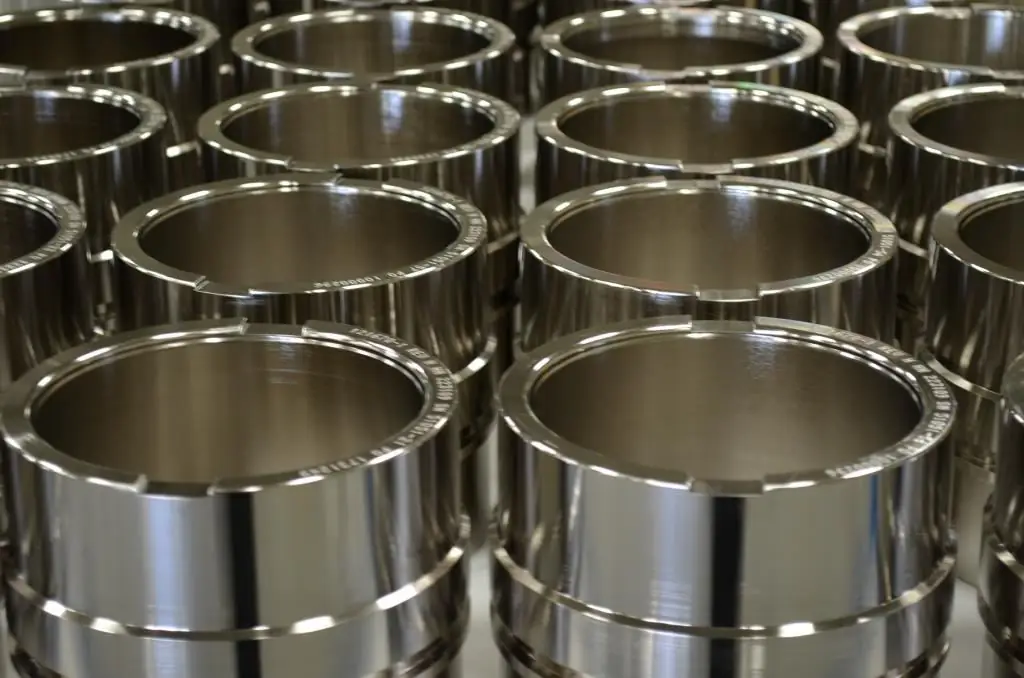
Agresif ortamlardaki malzemelerin çalışma koşulları, kaçınılmaz olarak kullanıcıları hedef nesnelerin ve yapıların özel korunması hakkında düşünmeye zorlar. Bunlar inşaat, sanayi, ev tipi teknik ve düşman etkilere karşı direnç gerektiren diğer tesisler olabilir. Bu sorunu çözmenin en etkili yollarından biri kaplamadır. Bu, parçaların ve yapıların dış kaplama yollarından biridir
Plazma yüzey kaplama: ekipman ve proses teknolojisi
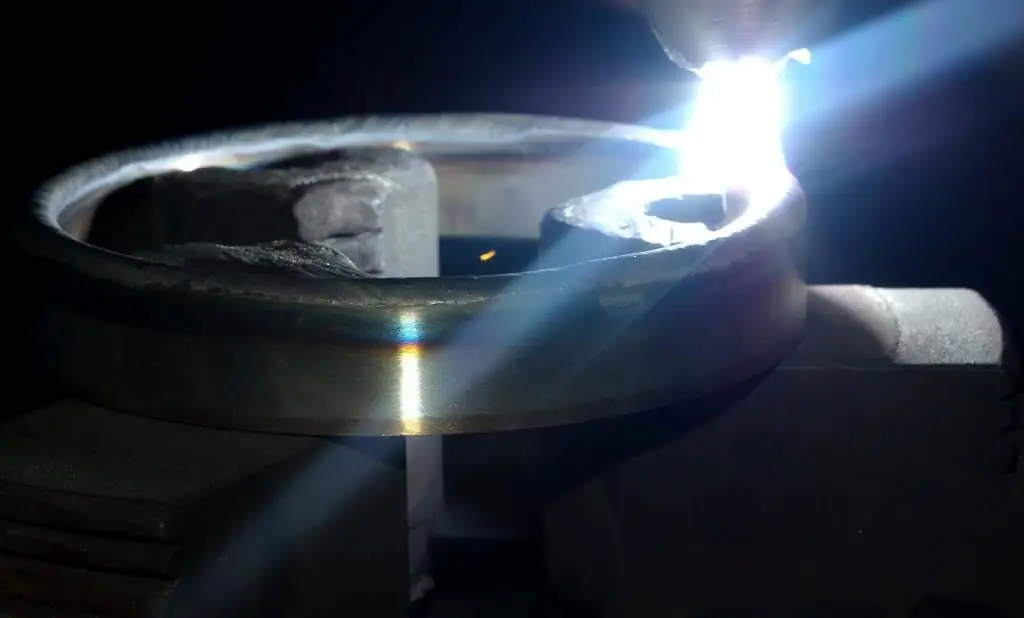
Plazma yüzey kaplamanın verimliliği ve sorunları, malzeme mühendisleri için son derece akuttur. Bu teknoloji sayesinde, yalnızca yüksek yüklü parçaların ve düzeneklerin hizmet ömrünü ve güvenilirliğini önemli ölçüde artırmakla kalmaz, aynı zamanda görünüşte %100 aşınmış ve tahrip olmuş ürünleri de eski haline getirmek mümkündür