2025 Yazar: Howard Calhoun | [email protected]. Son düzenleme: 2025-01-24 13:27
Yatırım modellerinin kullanımı oldukça popüler bir dökümhane üretim yöntemidir. Yöntem, teknolojik sürecin karmaşıklığı ve hazırlık süreçleri için yüksek işçilik maliyetleri ile ayırt edilir. Bu nedenle, boyutların doğru bir şekilde gözlemlenmesi ve parçaların yüzeyinin yüksek kalitesinin sağlanması gereken yerlerde kullanılır. Türbin kanatları ve yüksek performanslı aletler, takma dişler ve mücevherlerin yanı sıra karmaşık konfigürasyonlu heykeller bu şekilde dökülür. Kayıp mum dökümünün özü, döküm kalıbının tek parça olması, düşük erime noktalı malzemelerin modelinin kalıplama sırasında çıkarılmaması, eritilmesidir. Bu, boyutların ve kabartmanın dikkatli bir şekilde gözetilmesini sağlar. Modelden kalan boşluğa metal dökülür. Soğutma tamamlandıktan sonra kalıp bozulur ve ürün çıkarılır. Büyük seriler dökülürken ürünün maliyeti azalır.
Yöntem avantajları
Hassas dökümün ana avantajı, kalıp transferinin doğruluğu ve düşük yüzey pürüzlülüğüdür. Ayrıca başka avantajlar da mevcuttur:
- Hafif işlenmiş alaşımlı parçaların üretimi mevcuttur.
- İleri işleme ihtiyacını az altır.
- Aksi takdirde parçalar halinde yapılması ve bir araya getirilmesi gereken ürünler dökülür.
- Geniş serilerle, belirli işçilik yoğunluğunda (bir ürün başına) ve maliyetinde azalma sağlanır.
- Dökümün hazırlık işlemlerinin mekanizasyon ve kısmi otomasyonu imkanı.
Bu avantajlar, yöntemi, özellikle modern aşamalı döküm yöntemleriyle birlikte, günümüz metalurjisinde en popüler ve kullanılan yöntemlerden biri yapar.
Yatırım dökümün dezavantajları
Yöntemin şüphesiz avantajları, diğer yöntemler arasındaki hakimiyetini sağlamalıydı. Ancak hassas döküm yönteminin popülaritesine rağmen dezavantajları yaygın olarak benimsenmesini engellemiştir. Ana dezavantaj, çok aşamalı sürecin karmaşıklığıdır. Hazırlık aşamaları için oldukça karmaşık ve pahalı teknolojik donanımlar gerektirir. Küçük partiler halinde üretilen basit ürünler için bu yöntemin maliyeti daha yüksektir.
Hassas dökümün uygun maliyetli uygulaması için yöntemin avantajları ve dezavantajları karşılaştırılır, kararseçimi, fiyat / kalite oranı değerlendirmesi temelinde yapılır. Bu nedenle, esas olarak türbin kanatları, heykeller, yüksek hızlı aletler vb. gibi başka herhangi bir şekilde elde edilmesi zor olan en kritik ve pahalı ürünler için kullanılır. Diğer bir uygulama alanı ise büyük ölçekli dökümlerdir. ölçek etkisinin önemli bir maliyet düşüşü elde etmeyi mümkün kıldığı
Teknoloji
Yatırım döküm teknolojisi, nispeten emek yoğun olan çok aşamalı bir üretim sürecidir. İlk aşamada bir ana model yapılır, nihai ürünün tüm aşamalarından geçtikten sonra çalışan modellerin imalatında standart haline gelecektir. Bir ana modelin üretimi için hem özel model kompozisyonları hem de geleneksel olanlar - alçı veya ahşap - kullanılır. Ana modelin malzemesi, gücü ve işleme kolaylığını birleştirmelidir.
Ayrıca, hassas döküm teknolojisi, tüm çalışan modellerin içine döküleceği bir kalıbın oluşturulmasını sağlar. Kalıplar alçı, kauçuk, silikon, daha az sıklıkla metalden yapılır. Yapısal olarak, mutlaka sökülebilir olmalı ve tekrar tekrar kullanım için tasarlanmalıdır. Kalıp bir model kompozisyonu ile doldurulur, sertleştikten sonra demonte edilir ve bir sonraki çalışan model çıkarılır.
Benzersiz parçalar veya küçük işler üretirken, bir ana yerleşim planı ve bir kalıp oluşturma aşamaları atlanır ve malzeme manuel olarak kalıplanarak bir yerleşim (veya birkaç) yapılır.
Yatırım döküm sürecindeki bir sonraki adım,döküm kalıbının yerleşimi (veya yerleşim bloğu) etrafında imalat. Bu matrisler yapısal olarak zaten ayrılmaz ve tek kullanımlıktır, bu da ürünün boyutlarının ve pürüzlülüğünün dikkatli bir şekilde gözlemlenmesini mümkün kılar. Modern endüstride, hassas ve pahalı parçaların üretimi için iki tip kalıp kullanılır - zemine döküm için geleneksel kum-kil kalıpları ve kabuk kalıplar.
Kalıp tamamlandıktan sonra model kalıptan ısıtılarak veya kızgın buharla üflenerek eritilir. Kabuk formları ayrıca 1000 ˚С.'ye kadar ısıtılarak güçlendirilir
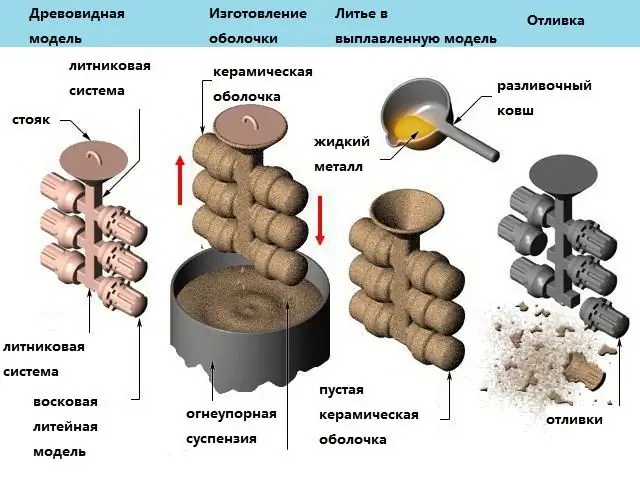
İşlemin son aşaması, ürünün fiili dökümünü, doğal koşullarda veya termostatta özel bir yöntemle soğutulmasını, kalıbın imha edilmesini ve ürünün temizlenmesini içerir. Yöntem, birkaç gramdan onlarca kilograma kadar yüksek kaliteli dökümlerin elde edilmesini sağlar.
Model Dizilimleri
Paylaşımın üretimi için malzeme belirli özelliklere sahip olmalıdır. Şuna benzer özelliklere sahip olmalıdır:
- Katı fazda plastisite. Gelecekteki ürünün şeklini doğru bir şekilde tekrarlamak ve gerekirse düzeltmek gerekiyor.
- Güç. Model, etrafında bir şekil oluşturma sürecine deformasyon olmadan dayanmalıdır.
- Birleşebilir. Model oluşturmak çok fazla zaman ve enerji gerektirmemelidir.
- Erimiş akışkanlık. Kompozisyon, gelecekteki ayrıntıların ana hatlarını tam olarak tekrarlayarak, kabartmanın tüm girintilerine ve ayrıntılarına kolayca nüfuz etmelidir.
- Ekonomi. Büyük seri üretim için özellikle önemlidir.
Model kompozisyonları için genellikle stearin ve parafin karışımı kullanılır. Bu malzemeler, parafinin yetersiz erime noktasını ve stearinin aşırı viskozitesini telafi ederek birbirlerinin parametrelerini başarıyla tamamlar.
Linyit mumu bazlı bileşimler sektörde daha az popüler değildir. Başlıca özellikleri, özellikle ürün modelleme için değerli olan neme dayanıklılık, dayanıklılık ve çok düzgün kaplamalar oluşturma yeteneğidir.
Kömür mumu, parafin ve stearin karışımından oluşan bileşikler de kullanılır.
Kalıp yapımı
Benzersiz ürünlerin üretimi için, manuel olarak veya şablonlara göre bir parça model malzeme kesilerek bir mizanpaj hazırlanır. Torna tezgahlarında da devir gövdesi şeklindeki modeller yapılmaktadır. Son zamanlarda, modellerin 3D baskı yöntemi giderek daha yaygın hale geldi. Hem tekli düzenler hem de küçük seriler için uygundur.
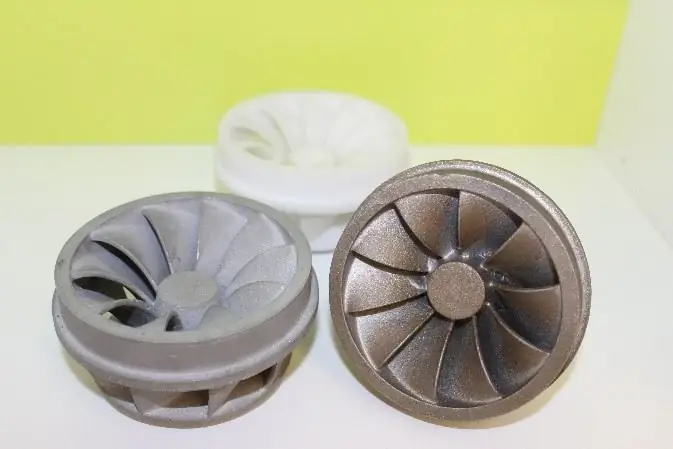
Modern bir endüstriyel 3D yazıcının maliyeti hala yüksektir, ancak bir üründen diğerine yeniden yapılandırma kolaylığı nedeniyle, çok sayıda heterojen küçük seri sipariş durumunda etkili bir model oluşturma aracı olabilir.
Çok sayıda aynı düzen yapmak için alçı, kauçuk, silikon veya metalden bir matris yapılır. Çalışma düzenleri, sırayla, bir matrise dökülerek üretilir. Tasarım gereği, belirli sayıda model üretme olasılığını sağlamak için kalıp katlanabilir olmalıdır. Seçilen malzeme de böyle bir fırsat sağlamalıdır, bu nedenle, yerleşime göre mukavemet, yoğunluk, düşük pürüzlülük ve kimyasal inertlik gibi gereksinimler uygulanır. Kalıp malzemesi ayrıca, bitmiş maketlerin kolayca çıkarılabilmesini ve boyutların yapıştırılabilmesini sağlamak için makete minimum düzeyde yapışmalıdır. Kalıbın önemli bir özelliği, özellikle büyük seriler için sağlamlığı ve aşınma direncidir.
Modeller ve bloklar yapma
Yatırım modellerinin üretiminde yaygın olarak kullanılan bir yöntem, bunları düşük basınç altında kalıplara dökmektir. Sıvı karışımın enjeksiyonu, hem manuel olarak, pistonlu şırıngalar kullanılarak hem de mekanik, hidrolik veya pnömatik süper şarj cihazları kullanılarak gerçekleştirilir. Kahverengi kömür mumu kullanılması durumunda, yüksek viskozitesi nedeniyle bileşimi beslemek için boru hatlarını ısıtmak gerekir. Genişletilmiş polistiren modelleri, otomatik kalıplama makinelerinde ekstrüzyonla yapılır.
Küçük dökümlerin seri üretimi durumunda ekonomik verimliliği artırmak ve emek yoğunluğunu az altmak için yerleşimleri bloklar halinde birleştirilir. Yolluk sistemleri, bir el havyası kullanılarak ladinlere ayrı ayrı düzenler eklenerek blokların üzerinde oluşturulur. Tek döküm veya küçük seri olması durumunda modeller el yapımıdır.
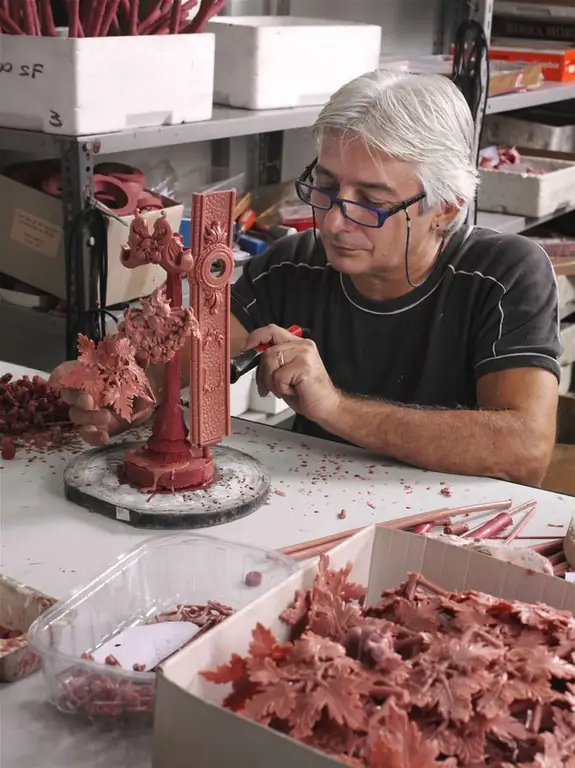
Kaplama sistemleri oluştururken, eriyiğin türbülanssız akışını, matrisin tüm elemanlarının eşit şekilde doldurulmasını sağlamak gerekir. PGS'den bir form doldururken, tüm formların tek tip doldurulmasını da izlemelisiniz.ladinler arasındaki açıklıklar ve hasarı önleme.
Kalıp yapmak
İncelenen hassas döküm yönteminde iki ana kalıp türü vardır:
- Kum-kil karışımları (SGM).
- Kabuk.
Akışkan mum döküm kalıpları esas olarak çok yüksek doğruluk gerektirmeyen küçük seri ürünlerin üretiminde kullanılır. Üretim süreci oldukça emek yoğundur ve modelcilerin ve kalıpçıların yüksek ve genellikle benzersiz becerilerini gerektirir. Kısmi mekanizasyon, kalıp kumunun hazırlanması ve doldurulması, sıkıştırılması gibi yalnızca belirli işlemlere uygundur.
Kabuk kalıplar ise özel imalat hassasiyeti gerektiren parçaların üretiminde kullanılmaktadır. Üretim süreci daha karmaşık ve uzundur, ancak makineleşmeye daha uygundur.
Zemin döküm
Bu, insanlığın ustalaştığı en eski metal işleme yöntemidir. Metal ürünlerin silah, alet veya mutfak eşyası olarak kullanılmaya başlamasıyla, yani yaklaşık 5 bin yıl önce, atalarımız tarafından eş zamanlı olarak hakim oldu. Erimiş metal, kum ve kil karışımından hazırlanmış bir matrise dökülür. Metal işleme için en erken yerler, külçeler ve plaserler şeklinde metal birikintilerinin yakınlarda bulunduğu yerlerde ortaya çıktı. Tipik bir örnek, demir dantel dökümü ile dünyaca ünlü Urallardaki Kaslı Fabrikasıdır.
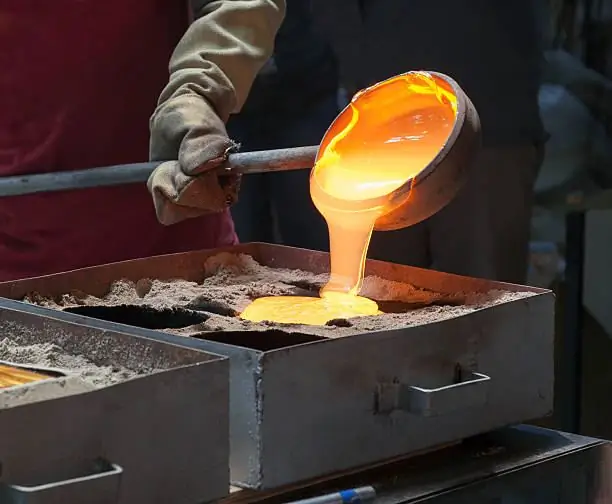
Hassas döküm yöntemi metal ürünlerin imalatı için kullanılır - hem demirli hem derenkli. Ve yalnızca sıvı fazda (titan gibi) reaksiyona girme eğiliminde olan metaller için, diğer bileşimlerden matrisler yapmak gerekir.
PGS'de döküm üretim süreci aşağıdaki aşamalardan oluşur:
- model yapımı;
- şişenin hazırlanması;
- Karışımın şişeye doldurulması ve sıkıştırılması;
- metal döküm;
- dökümü çıkarma ve temizleme.
ASG'den form - tek kullanım. Bitmiş ürünü elde etmek için kırılması gerekecek. Aynı zamanda, karışımın çoğu yeniden kullanıma hazırdır.
Çeşitli tane boyutlarında ağırlıklı olarak kuvars kumlarının ve içeriği yüzde 3 ila 45 arasında değişen plastik killerin bileşimleri ASG için malzeme olarak kullanılır. Bu nedenle, örneğin sanat dökümleri, %10-20 kil içeriğine sahip bir karışım kullanılarak üretilir, özellikle büyük dökümler için kil içeriği %25'e ayarlanır.
İki alt tür kullanılır:
- Karışımları kaplama. Kalıbın iç yüzeyinde bulunurlar ve erimiş metal ile etkileşime girerler. Isıya dayanıklı olmalı, sıcaklık farkları ve bunun sonucunda ortaya çıkan gerilimler tarafından yok edilememelidir. Bu karışımlar, yüzeyin ayrıntılarını dikkatlice iletmek için ince tanelidir. Karışımın gaz geçirme özelliği de çok önemlidir.
- Doldurma karışımları. Kaplama tabakası ile şişenin duvarları arasında dolgu yapmak için kullanılırlar. Dökülen metalin ağırlığına dayanmalı, ürünün şeklini korumalı ve gazların zamanında ve tam olarak çıkarılmasına katkıda bulunmalıdırlar. Daha ucuz kum kalitelerinden üretilir,yeniden kullanılabilir.
Döküm gazları kalıp kumunun kütlelerinden değil de yolluk sisteminden kaçarsa, dökümde kusurlar meydana gelir ve bu da evliliğe yol açar.
Toprağa dökmenin geleneksel teknolojisi, A. Tarkovsky'nin "Andrei Rublev" filminde ayrıntılı olarak gösterilmektedir. "Çan" adlı kısa hikayede, ölen bir ustanın oğlu olan genç adam Boriska, bir dökümhane artelini yönetiyor ve bir kilise çanı çalıyor.
Kabuk döküm
Kabuk kalıplarda hassas döküm yöntemi, ürün boyutlarının en iyi aktarımı ve düşük yüzey pürüzlülüğü ile karakterize edilir. Model, kahverengi kömür mumu gibi eriyebilir bileşiklerden yapılmıştır. Dökümhaneler ayrıca parafin-stearin bileşimini eşit oranlarda yaygın olarak kullanır. Büyük ebatlı dökümlerde, modeli deformasyondan korumak için model malzemesine tuzlar dahil edilir. Çözeltiye daldırılarak model, yüksek sıcaklık süspansiyonu ile 6-10 katman halinde kaplanır.
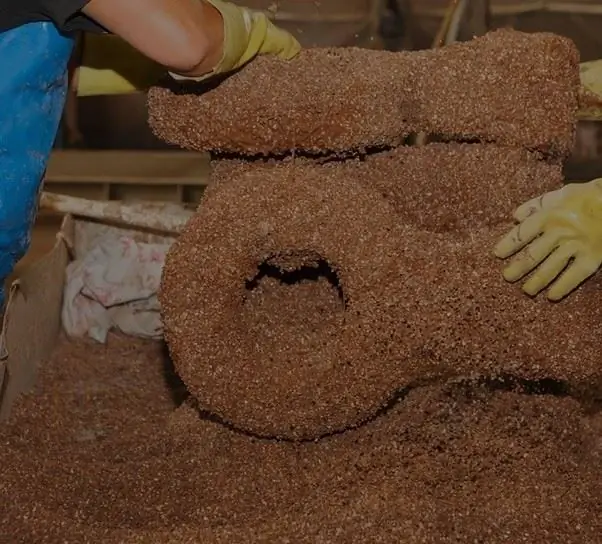
Hidrolize silikatlar bağlayıcı görevi görür, elektrokorindon veya kuvars kristalleri ısıya dayanıklı serpme olarak alınır. Kabuk kalıp malzemeleri yüksek mukavemet, düşük higroskopiklik ve mükemmel gaz geçirgenliği ile karakterize edilir.
Düzen gazlı amonyak atmosferinde kurutulur. Bir sonraki aşamada, parafin modeli çıkarmak için kalıp 120 ˚C'ye ısıtılır. Karışımın kalıntıları, yüksek basınç altında aşırı ısıtılmış buharla çıkarılır. Daha sonra, kalıp 1000 ˚С'ye kadar olan sıcaklıklarda kalsine edilir, bu da nihai sabitlenmesine ve maddelerin uzaklaştırılmasına yol açar,döküm işlemi sırasında gazlar olarak salınabilir.
Kabuk, çelik bilye ile kaplanmış bir tür şişeye yerleştirilir. Bu, kalıbı eriyikle doldururken konfigürasyonun korunmasına yardımcı olur ve aynı zamanda dökümün soğutulması için koşulları iyileştirir. Eriyik 1000 ˚С'ye ısıtılan kalıplara dökülür. Ürün termostatta özel bir programa göre soğutulduktan sonra kalıp bozulur, döküm çıkarılır ve temizlenir.
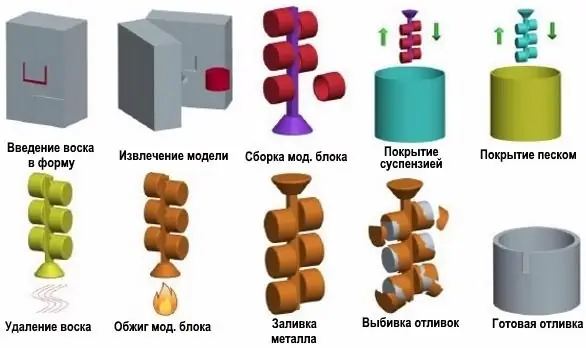
Bu döküm yönteminin ana avantajı, yüksek boyutsal doğruluk ve düşük yüzey pürüzlülüğüdür.
Yöntemin ek avantajları:
- İşlenmesi zor olan alaşımlardan döküm parçalar.
- Aksi takdirde parça parça dökülüp tekrar bir araya getirilmesi gereken öğelerin dökümü.
Bu hassas döküm yönteminin dezavantajları, düşük metal kullanımı ve artan emek yoğunluğudur.
Hassas döküm
Hassas hassas döküm - bu hem teknolojiye hem de nihai ürünün kendisine verilen isimdir. Yüksek döküm doğruluğu, kalıbın hazırlanması sırasında ürünün modelini ondan çıkarmaya gerek olmamasıyla sağlanır. Geleneksel yöntemi kullanırken, bir döküm matrisinin üretimi karmaşık ve çok zaman alan çok aşamalı bir süreçtir. Bu, özellikle girintiler, girintiler ve iç boşluklar içeren karmaşık konfigürasyonlu parçaların dökümü durumunda geçerlidir.
Örneğin, değişken yüzey eğriliğine sahip bir dökme demir veya bakır vazoyu dökerken birçok hile kullanmanız gerekir. evet, ilkşişenin alt yarısı doldurulur, daha sonra model çıkarılır, ters çevrilir ve üst yarısı sıkıştırılır. Model kompozit yapılmalıdır, vazonun kulpları iki elemandan yapılmıştır, iki aşamada model boşluğundan dışarı çekilirler - önce alt eleman, sonra üst eleman. Tüm bu sayısız dönme ve sürükleme, kalıp yüzeyinin bütünlüğü üzerinde ve nihayetinde dökümün boyutlarının ve yüzeyinin kalitesinin korunmasının doğruluğu üzerinde olumlu bir etkiye sahip olamaz. Ek olarak, şişelerin parçalarını doğru bir şekilde eşleştirme ve bunları birbirine güvenli bir şekilde bağlama sorunu devam etmektedir.
Hassas döküm üretimi bu eksikliklerden yoksundur, bu kadar yüksek nitelikli modelciler gerektirmez ve ön döküm işlemlerinin emek yoğunluğunu önemli ölçüde az altır. Bu, özellikle çok sayıda dökümde belirgindir.
Yöntem, GOST 26645-85'e göre 2-5. doğruluk sınıfına ulaşmayı sağlar. Bu, türbin bıçakları, yüksek performanslı frezeler ve matkaplar dahil kesici aletler, kritik yüksek yüklü braketler, araçların yüksek yüklü küçük parçaları, takım tezgahları ve diğer karmaşık mekanizmalar gibi yüksek hassasiyetli ürünlerin dökümünü mümkün kılar.
Yüksek boyutsal doğruluk ve yüksek yüzey sınıfı, metal tasarrufu sağlayan ve üretim maliyetlerini az altan dökümün daha fazla işlenmesi ihtiyacını en aza indirir.
Ekipman
Gerekli olan hassas döküm ekipmanı çeşitli ve karmaşıktır. İşletmeler bunları tek ve iyi koordine edilmiş bir komplekste birleştirir,site, atölye veya ayrı üretim olarak düzenlenmiştir.
Kompleksin bileşimi, dökümlerin üretim ölçeğine, boyutuna, konfigürasyonuna ve dolaşımına bağlıdır.
Böylece takma diş ve mücevher üretiminde ekipman şunları içerecektir:
- model tablosu;
- termostatlı mufla fırını;
- modelin şeklini düzeltmek için bir dizi neşter ve spatula;
- oluşturma tahtası;
- şişe;
- kalıp kumunu depolamak ve hazırlamak için tanklar;
- kum tokmak aletleri seti;
- metal eritmek için pota;
- Forseps;
- kalıbı kırmak için çekiç.
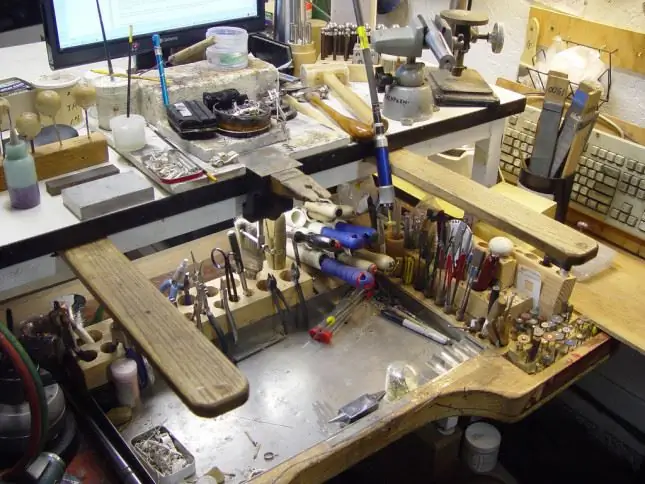
Bu üretim kompleksi bir masaya ve bir dolaba kolayca sığabilir. Örneğin, alüminyum dökümler - bir cihazın parçaları gibi seri üretim yapılması planlanıyorsa, aşağıdakiler için ekipman gerekli olacaktır:
- seramik kalıpları şekillendirme ve dökme;
- kurutma formları;
- model malzemeyi eritmek ve ısıya dayanıklı bir tabaka uygulamak;
- kalıp malzemelerinden dökümleri temizleme.
Ve son olarak, bir eriyik elde etmek ve bir kalıba dökmek için tasarlanmış dökümhane kompleksinin gerçek ekipmanı. Döküm ekipmanı olabilir:
- düşük basınç altında;
- santrifüj;
- her zamanki yerçekimi yolunda.
Enjeksiyon kalıplama ve santrifüj döküm makineleri, ayrı bir yüksek düzeyde mekanize ve otomatiktir. Dükkanın atmosferinden izole edilmiş üretim kompleksi. El emeğini ve insanların zararlı koşullara maruz kalmasını en aza indirirler. Komplekslerin bulunduğu sızdırmaz odalar, egzoz gazlarının tam olarak yakalanmasını ve saflaştırılmasını sağlayarak işletmenin çevre dostu olma özelliğini önemli ölçüde artırır.
Kayıp mum dökümü, özellikle gelişmiş kalıp yapımı ve dökme teknikleri ile birleştirildiğinde, gelişme için oldukça yüksek bir potansiyele sahiptir.
Önerilen:
Welsumer tavuk ırkı: açıklama, içerik, avantajlar ve dezavantajlar, incelemeler
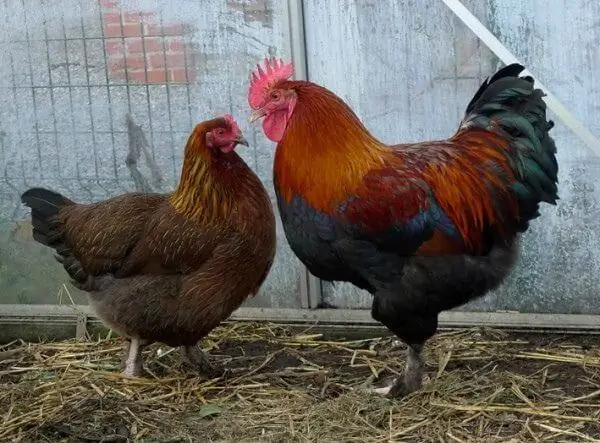
Kişisel ev arsaları için, tavukların cinsi her zaman üretkenliğe göre seçilmez, bazıları için görünüm önemlidir. Parlak tüyleri olan kuşların, özel bir bakıma ihtiyaç duymayan bahçede dolaşması güzeldir. Dış güzellik mükemmel performansla birleştiğinde daha da iyi. Bu gereksinimler, Welzumer cinsi tavuklar tarafından karşılanır. Pek çok olumlu özelliği vardır, bu yüzden genellikle özel arka bahçelerde yetiştirilir
Kayıp SNILS, numara nasıl bulunur? Kayıp durumunda SNILS'i geri yüklemek için belgeler
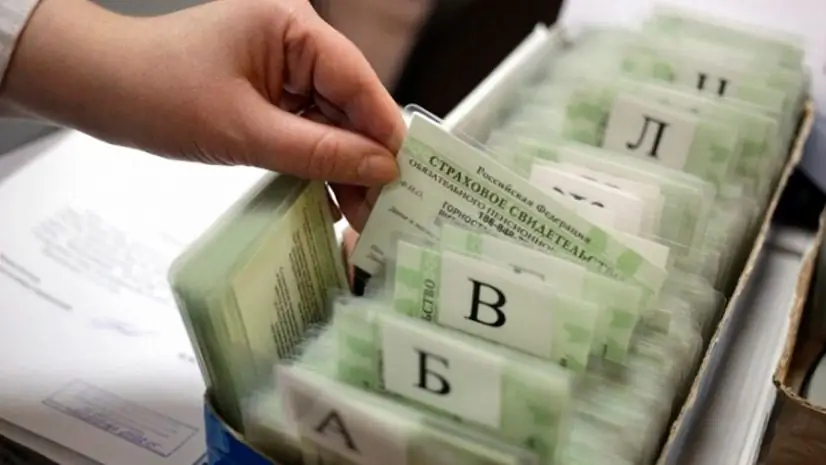
SNILS, Rusya Federasyonu'nda yaşayan her insanın hayatında önemli bir belge ve sayıdır. Ne yazık ki, herhangi bir belge kaybolabilir. Ve sigorta sertifikası da. Bu makale, SNILS numarasını nasıl bulacağınız ve kaybolursa nasıl geri yükleyeceğiniz hakkında konuşacaktır
Leasing: avantajlar ve dezavantajlar, ana işlev, sınıflandırma, ipuçları ve püf noktaları
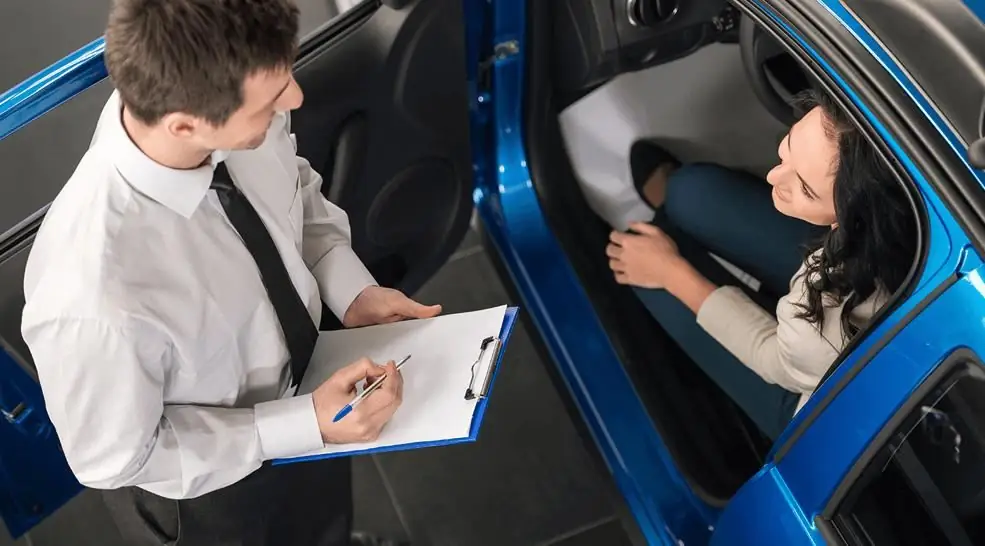
Bir finansal faaliyet biçimi olarak leasing'in tanımı, işlevleri, avantajları ve dezavantajları. Genel bilgiler, kiralama ilişkilerinin sınıflandırılması. En yaygın ürün olarak kiralama yoluyla araba satın almanın artıları ve eksileri. Leasing şirketi seçimi için öneriler
Plexiglas gravür: avantajlar ve dezavantajlar, teknoloji, ekipman
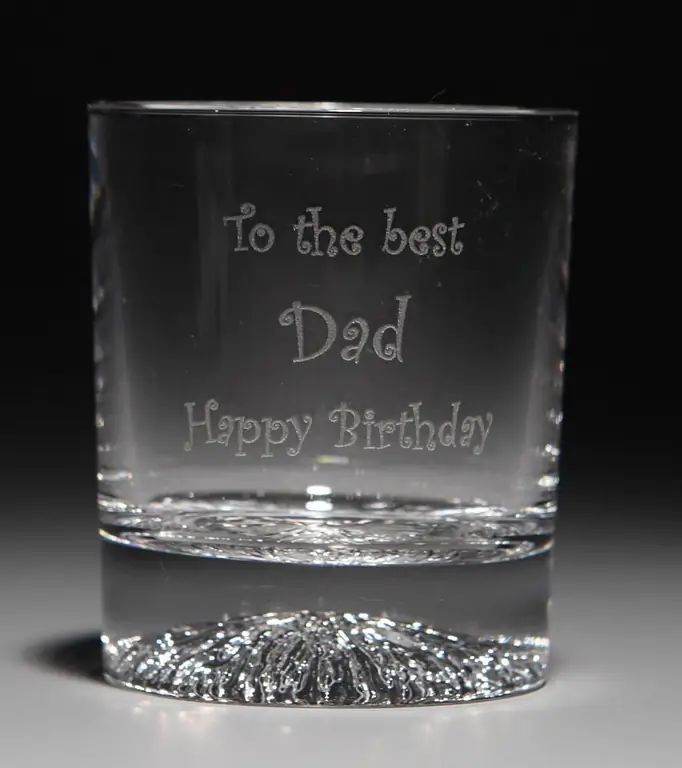
Plexiglas oymacılığı bir resim sanatı olarak kabul edilir. Enfes çizimlerle süslenmiş bir hatıra heykelciği, vitray pencereler veya cam bir masa, hassas bir sanatsal tadı barındırıyor. Asitleme ve kumlama teknolojileri geçmişte kaldı. Bugün, bir lazer makinesinin yardımıyla her kişi son derece ayrıntılı bir desen oluşturabiliyor
Ultrasonik işleme: teknoloji, avantajlar ve dezavantajlar
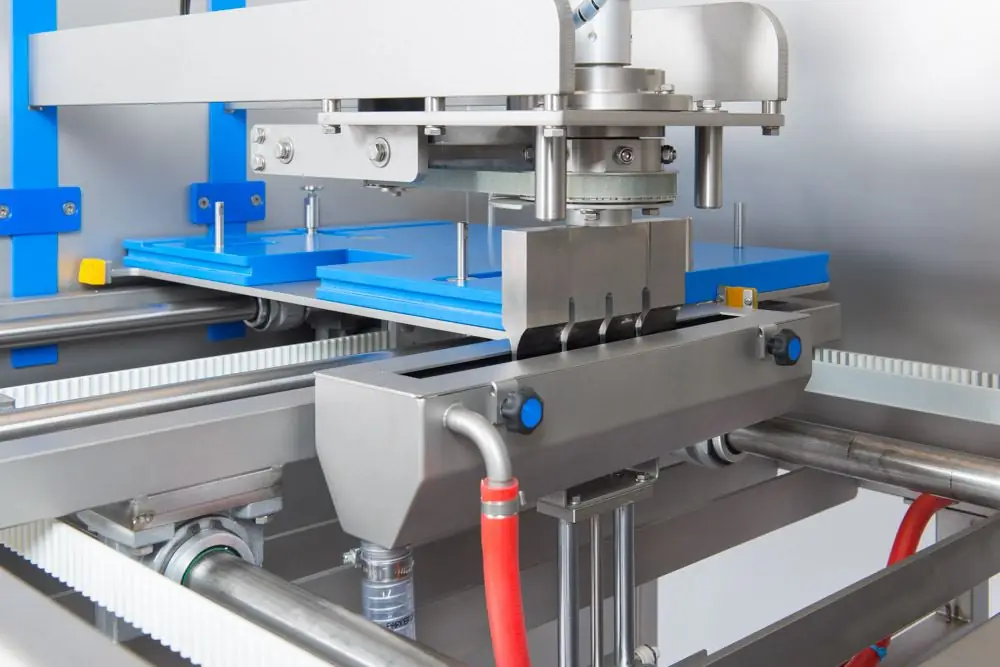
Geliştirmenin bu aşamasındaki metal işleme endüstrisi, farklı sertlik derecelerine sahip iş parçalarını kesme ve delme gibi karmaşık görevleri çözebilir. Bu, geniş bir elektromekanik yöntem grubu da dahil olmak üzere, malzemeyi etkilemenin temelde yeni yollarının geliştirilmesi nedeniyle mümkün oldu. Bu türün en etkili teknolojilerinden biri, elektroakustik radyasyon ilkelerine dayanan ultrasonik tedavidir (UZO)