2025 Yazar: Howard Calhoun | [email protected]. Son düzenleme: 2025-01-24 13:27
Kabuk kalıplarda döküm, aynı zamanda kabuk döküm olarak da adlandırılır. Ve yurt dışında bu çalışma yöntemine Shell denir.
Genel bilgi
Günümüz endüstriyel endüstrisinde birçok farklı döküm yöntemi kullanılmaktadır. Kabuk döküme ek olarak, metal kalıplarda ve diğer birçok yöntemin yanı sıra hassas döküm de kullanılır. Kum kalıplama ile karşılaştırıldığında bu döküm yöntemlerinin genel avantajı, şekil ve boyut açısından daha doğru son malzemelerle sonuçlanmalarıdır. Ayrıca bu tür ürünlerin yüzeyindeki pürüzlerin sayısı da azalır. Daha nadir durumlarda, ancak yine de, eritmeden sonra sonraki işleme ihtiyacı ortadan kalkar. Her şeyin yanı sıra kabuk kalıplarda döküm ve diğer yöntemlerin kullanılması bu işlemin olabildiğince mekanize edilebilmesine katkı sağlamakta, bunun sonucunda otomasyonu da artmaktadır. Ve bu, elbette, herhangi bir endüstriyel tesisin üretkenliğini büyük ölçüde artırır.
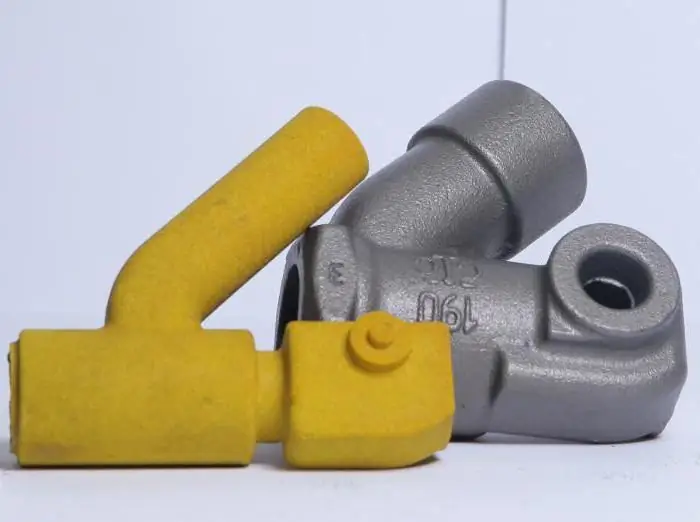
Kabuk döküm
Özellikle bunun hakkında konuşursakyöntemi, ilk olarak 1953'te fabrikalarda tanıtıldı. Şu anda, yöntem oldukça yaygın olarak kullanılmaktadır. Örneğin, Kirovets traktörü için parçaların çoğunu üreten kabuk kalıplara dökülüyor. Bu yöntemle üretilen tüm parçalar çelik veya dökme demirden en yüksek kalitededir. Kabuk döküm, dökümün nihai sonucunun iki kum-reçine kabuğundan oluşan bir şekle sahip olduğu bir yöntemdir. Ayrıca, bu parça imalat yöntemi, yalnızca küçük veya orta boyutlu, ancak aynı zamanda yüksek doğrulukta bir parça oluşturmanın gerekli olduğu durumlarda kullanılır. Bu döküm yöntemi için uygulama örnekleri, motor parçaları veya ince duvar dökümleridir.
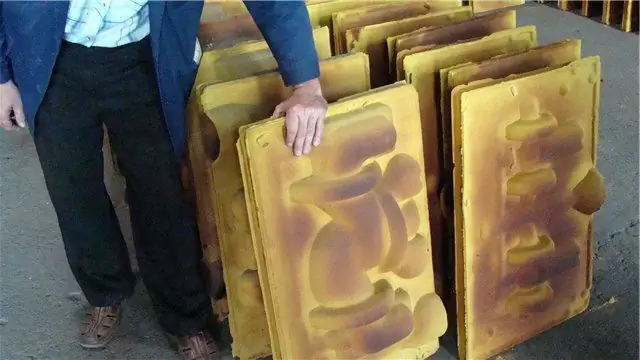
Yolun Özü
Bu çalışma yöntemi ile fanlar, motorlar, pompalar veya tekstil makineleri için çeşitli parçalar elde edebilirsiniz. Ancak alınan ürünün maksimum uzunluğu 1 metreyi geçemez ve 200 kg'dan daha ağır olamaz.
Kabuk kalıplara dökümün özü, kum-reçine karışımlarının bir parçası olan ısıyla sertleşen reçinelerin belirli özelliklerine dayanır. Bu tür bileşenleri kullanmanın avantajı, bu reçinelerin 200-250 santigrat derece sıcaklıkla işlendiğinde hızlı ve kalıcı olarak sertleşme eğiliminde olmasıdır.
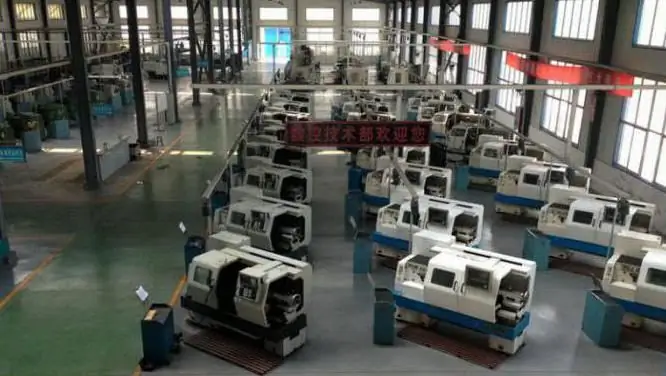
Döküm için bir kabuk kalıp yapma
Bir sonraki döküm için bir kalıp yapmak için, tam teşekküllü bir kabuk kalıbı elde etmek için bağlantı elemanı olan termoset reçine ilavesiyle birlikte gelen ince taneli kuvars kumu olması gerekir. Bu malzemeler, özellikle reçine, belirli bir sıcaklık bariyerini geçtiklerinde sertleştikleri için seçilmiştir. Üretim süreci aşağıdaki gibidir. İlk olarak, reçine 140-160 santigrat dereceye kadar ısıtılır. Böyle bir ortamın etkisi altında kuvars kumu kalıbını tamamen saran sıvı yapışkan bir kütleye dönüşür.
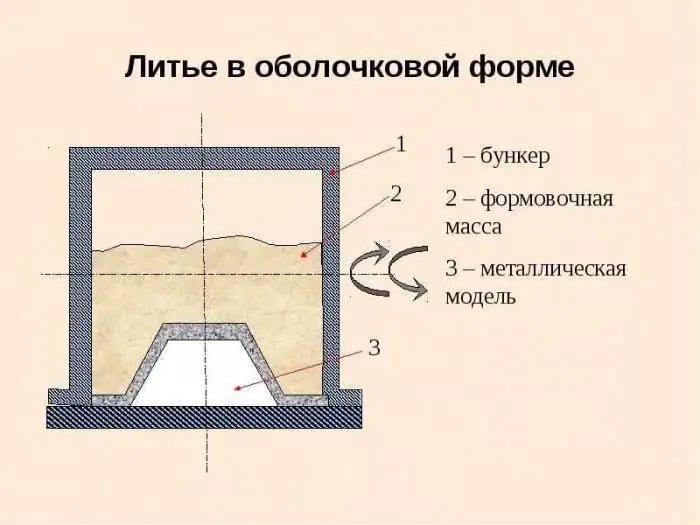
Kabuk kalıplarda dökümün kapsamı oldukça geniştir ve bu nedenle kalıp yapma süreci otomatik veya otomatik hale getirilmiştir.
Kalıp tamamen reçine ile kaplandıktan sonra sıcaklık 200-250 santigrat dereceye yükseltilir. Bu sıcaklık eşiği, yapışkan kütlenin geri dönülmez şekilde sertleşmesi ve bir şekil oluşturması için oldukça yeterlidir. Ayrıca parçaların döküm işlemi başladığında, yani erimiş metal kalıba girdiğinde, içindeki sıcaklık yaklaşık 600 dereceye ulaşır. Bu mod, reçinenin erimemesini, ancak kalıbın üzerinde gözenekler bırakarak yanmasını sağlamak için yeterlidir ve gazların kaçmasını kolaylaştırır.
Kabuk kalıba dökümün avantajları ve dezavantajları
Diğer tüm üretim süreçleri gibi, bunun da artıları ve eksileri var. Bu döküm yöntemini, örneğin, dökümle karşılaştırırsaksıradan kum kalıpların birkaç avantajı vardır:
- İlk ve oldukça önemli fark, 7-9 olan doğruluk sınıfıdır. Ayrıca elde edilen parçanın yüzey kalitesi 3-6'ya kadar iyileştirilir. Ek olarak, dökümden sonra ortaya çıkan parçanın daha sonraki işlenmesi için izin verilen paylar az altılır.
- Büyük artılardan biri, döküm imalatı için işçilik maliyetlerinde önemli bir azalmadır.
- Bu döküm yöntemi, kapı kanallarının boyutunun küçültülmesi nedeniyle metal miktarının yanı sıra kalıp malzemelerinin tüketimini de az altır.
- Evlilik çıktı miktarını önemli ölçüde az alttı.
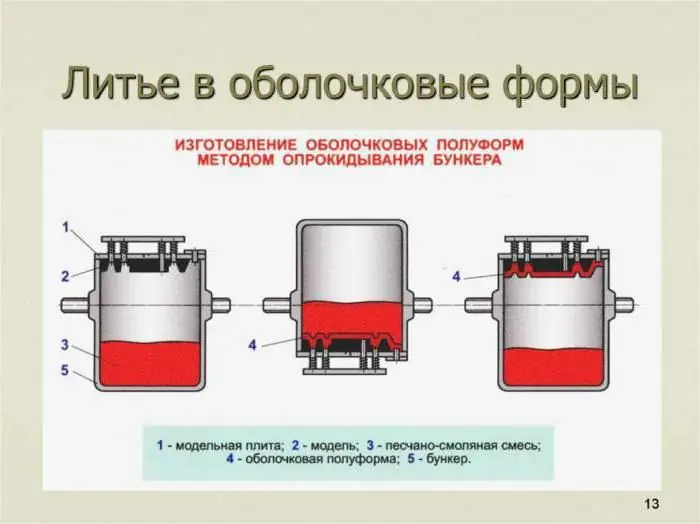
Ancak, kabuk kalıplarda döküm yapmanın bazı dezavantajları vardır. Bunlar şunları içerir:
- Kabuk kalıp ömrü - 1 döküm.
- Kum kalıplama maliyeti oldukça yüksektir.
- Zararlı gazların yüksek yüzdesi.
Corpus oluşturma süreci
Vücut şekillendirme süreci altı aşamada gerçekleştirilir:
- İlk adım, karışımı sıcak bir metal modelin üzerine dökmenin yanı sıra, parçanın etrafında ince, güçlü bir kabuk oluşana kadar birkaç on saniye boyunca tutma işlemidir. Çoğu zaman, modeller dökme demirden yapılır ve ısıtmaları 230-315 dereceye kadar gerçekleştirilir.
- Bundan sonra fazla kalıp kumunu çıkarmak için bir işlem yapılması gerekir. Kabuğun kalınlığı sonunda 10 ila 20 arasında olmalıdır.mm. Karışımın modelde kalma süresine ve ayrıca sıcaklığa bağlıdır.
- Ardından model plakasını kalıpla birlikte kürleme işleminin sonuna kadar olacakları fırına aktarmak gerekir. Bu prosedürün sonunda, kabuğun gücü 2,4 ile 3,1 MPa arasında olmalıdır.
- Fırından çıkarıldıktan sonra sertleşen kabuk plakadan çıkarılır. Bu işlem için özel bir itici kullanılır.
- Bundan sonra, iki veya daha fazla model bir çeşit kelepçe kullanılarak veya yapıştırılarak birbirine sabitlenir. Bu kalıplar, kabuk kalıplarda döküm için kullanılabilir veya basitçe depolanabilir. Neredeyse sınırsız raf ömrü.
- Bitmiş kalıba döküm işlemine başlamadan önce, içlerine bilye dökülür, bu da daha sonraki döküm sırasında kalıbın önlenmesine veya yok edilmesine yardımcı olur.
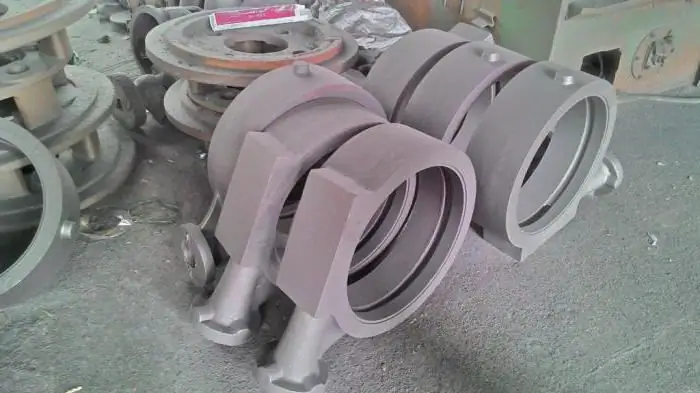
Döküm Ayrıntıları
Takım imalatında izin verilen tipik toleransların 0,5 mm olabileceği gerçeğiyle başlamaya değer. Yüzey pürüzlülüğüne 0,3 ila 0,4 mikron aralığında izin verilir. Bu sınırlar, ince taneli kum kullanılması gerçeğiyle doğrulanır. Şunu da belirtmekte fayda var: reçine kullanımı, yüzeyin çok pürüzsüz olmasına büyük ölçüde katkıda bulunur.
Üretim hacimleri
Bu tür kalıp ve parçaların imalatında bulunabilmek için kalıp modelinin montajına katılmak gerekir. Kurulum için gereken süre bir haftadan azdır. Kurulum tamamlandıktan sonra çıktı miktarısaatte 5 ila 50 parçaya ulaşın. Saatte bu tür üretim hacimleri oldukça gerçektir, ancak bunun için döküm işlemini buna göre hazırlamak gerekir. Döküm için gerekli olacak ana malzemeler, dökme demir, alüminyum, bakır ve ayrıca bu tür metallerin alaşımlarıdır. Bir diğer gerekli malzeme ise alüminyum ve magnezyum kullanan bir alaşım olacaktır.
Önerilen:
Benzin "Kabuk": incelemeler ve özellikler
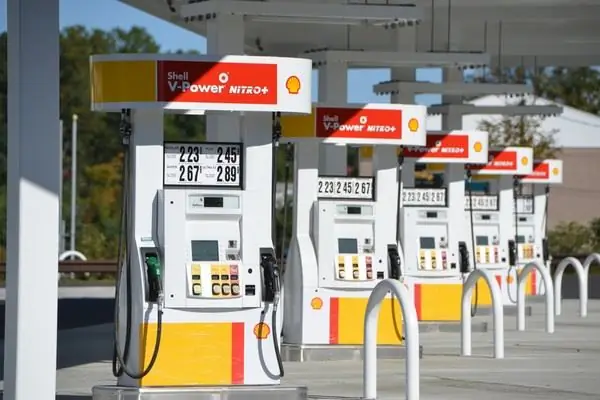
Yazı Shell ürünleri için bir reklam değildir, bu nedenle önce iyi otomotiv yakıtı kriterlerini prensip olarak tanımlayacağız, ardından Shell marka benzinin nüanslarını ele alacağız. Sürücülerin Shell benzini hakkındaki yorumları farklı ve özneldir. Bu nedenle, sakince ve duygular olmadan ilgilenelim
Sürekli çelik dökümü: çalışma prensibi, gerekli ekipman, yöntemin avantajları ve dezavantajları
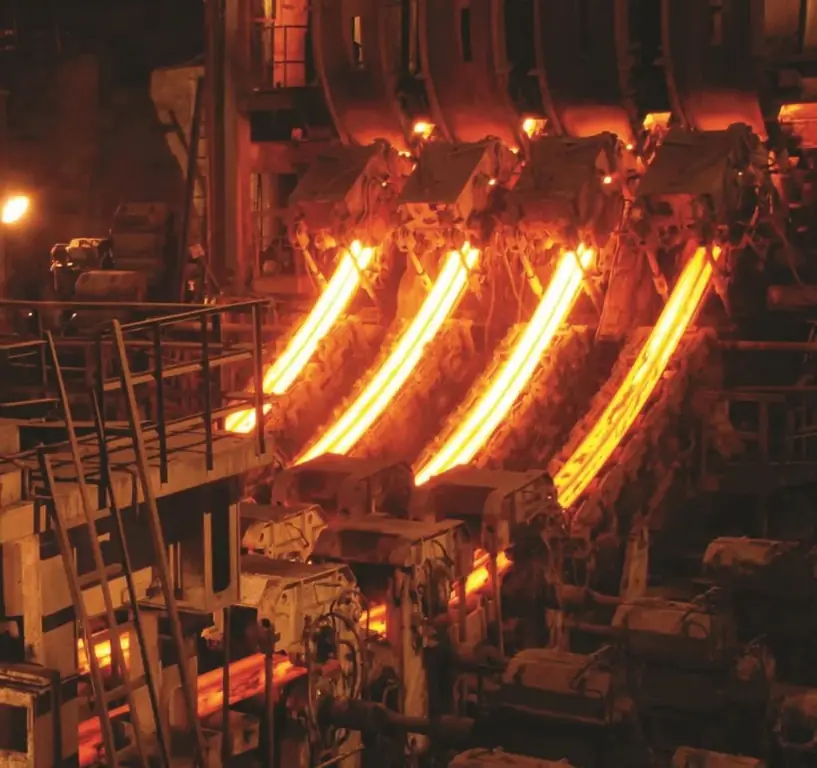
Bugün, çok sayıda çeşitli şey, parça vb. çelikten yapılmıştır.Doğal olarak, bu çok miktarda kaynak malzeme gerektirir. Bu nedenle, tesisler uzun süredir en önemli özelliği olan yüksek verimlilik ile karakterize edilen sürekli çelik döküm yöntemini kullanıyor
REPO işlemleri. Menkul kıymetlerle REPO işlemleri
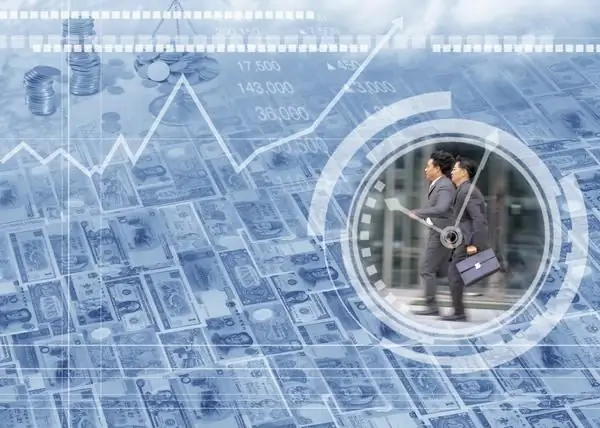
REPO işlemleri, herhangi bir değerli varlığın satışının gerçekleştirildiği ve işlem sırasında sabitlenmiş bir fiyattan belirli bir süre sonra geri alımının gerçekleştirildiği prosedürlerdir. İşlemin son (ikinci) aşamasını temsil eden ters satın alma zorunludur
Bankaların nakit ve kredi işlemleri. Bankacılık işlemleri türleri
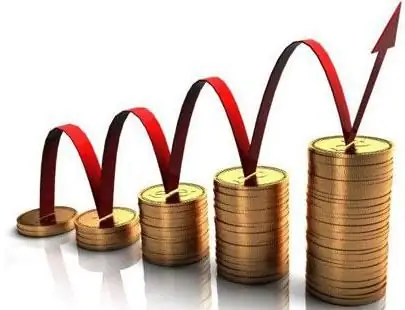
Ticari bir bankanın gerçekleştirdiği ana işlemler kredi ve nakittir. Özellikleri nelerdir? Hangi kurallara göre yapılır?
Brent ve Ural petrol vadeli işlemleri nelerdir. Petrol vadeli işlemleri
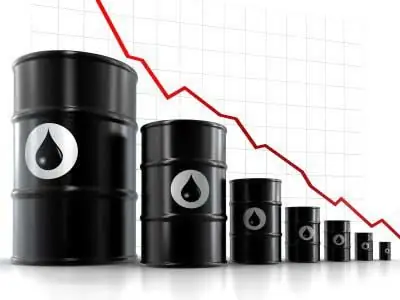
Petrol vadeli işlemleri, bir emtia satın almak veya satmak için tüm koşulları detaylandıran sözleşmelerdir. Fiyat hareketlerini tahmin etme yeteneğine sahip vadeli işlemler iyi gelir getirebilir