2025 Yazar: Howard Calhoun | [email protected]. Son düzenleme: 2025-06-01 07:15
Gecikmeli koklaştırma üniteleri, ağır petrol arıtma için en yaygın donanım çözümüdür. Cihazları 2 ana modül içerir - hammaddenin ısıtıldığı ve koklaştırıldığı reaktör ve mekanik işleme. Tesislerin tasarımı aşamalar halinde gerçekleştirilir ve proses ekipmanlarının hesaplanması ve seçilmesini, teknik ve ekonomik göstergelerin belirlenmesini içerir.
Hedef
Koklaştırmanın teknolojik süreci, petrol arıtmanın yollarından biridir. Ana amacı, büyük topaklı petrol koku elde etmektir. Endüstride kullanılan 3 koklaştırma yöntemi vardır:
- Periyodik, küplü. Hammadde yatay bir aparata yüklenir, altındaki ocak ile ısıtılır ve 2-3 saat kalsine edilir. Bundan sonra fırın soğutulur ve bitmiş ürün boş altılır. Bu yöntem en basit ve en az üretken olanıdır.
- Sürekli. Bu yöntem hala endüstriyel gelişme aşamasındadır.
- Yarı-sürekli, şu anda alınanen yaygın.
Ultra gecikmeli kok üniteleri, en son proses ekipmanı türüdür. İçlerinde hammadde bir fırında önceden ısıtılır ve daha sonra gerekli sıcaklığı korumak için bir ısı yalıtım katmanına sahip olan ısıtılmamış reaksiyon odalarına aktarılır. Reaktörlerin sayısı ve boyutu, fırınların gücü tüm tesisin performansını etkiler.
Rusya'daki ilk DCU'nun operasyonu 1965 yılında Ufaneftekhim'de başladı. Tesisin gecikmeli kok kömürü bugün hala çalışıyor. 2007 yılında yeniden yapılanmadan sonra, işlenmiş hammadde kütlesi açısından verimliliği yaklaşık 700-750 bin ton/yıl'dır.
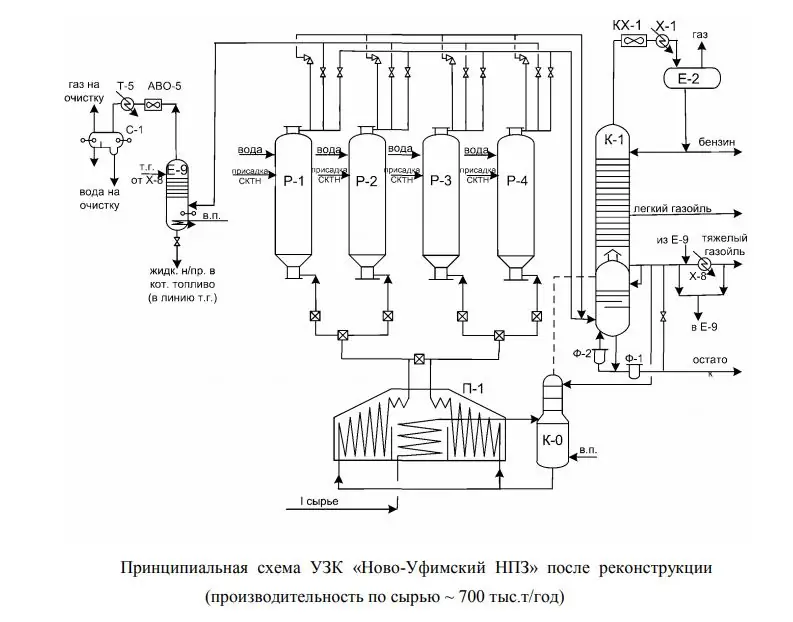
Nihai ürünler
Kok hariç, ultrasonik testte aşağıdaki maddeler elde edilir:
- koklaştırma gazları (proses yakıtı olarak kullanılır veya propan-bütan fraksiyonu elde etmek için işlenir);
- benzin;
- kok distilatları (yakıt, kırma besleme stoğu).
Yerli ultrasonik test makinelerinde, kok verimi ağırlıkça %20-30'dur. Bu gösterge öncelikle hammadde kalitesine bağlıdır. Metalurji endüstrisi bu ürüne en büyük ihtiyacı yaşıyor (anot ve elektrot üretimi, alüminyum, aşındırıcılar, karbürler, karbon-grafit malzemeler, ferroalyajlar). İlk Ufa DCU'ya ek olarak, Rusya'da başka gecikmeli kok üniteleri de inşa edildi: Omsk Rafinerisi, Novokuibyshevsk Rafinerisi, LLC LUKOIL-Volgogradneftepererabotka, LUKOIL-Permnefteorgsintez, LUKOIL-Permnefteorgsintez, Angarsk Petrokimya Şirketinde, NOVOIL OJSC (Ufa), TANECO PJSC (Nizhnekamsk).
Hammaddeler
Koklaşma için gıda malzemeleri 2 gruba ayrılır: birincil ve ikincil işleme ürünleri. Gecikmeli koklama ünitelerinde hammadde olarak aşağıdaki maddeler kullanılmaktadır:
- akaryakıt;
- yarım katran;
- tar;
- kömür katranı;
- asf alt ve diğer endüstriyel petrol ürünleri;
- sıvı kömür kalıntısı;
- ağır piroliz ve şeyl katranı;
- termal çatlama kalıntıları;
- petrol bitüm ve ağır yağlar.
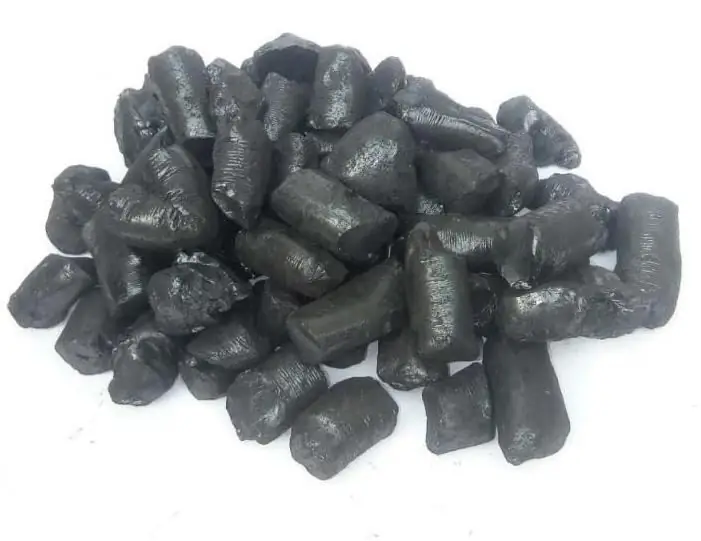
Yüksek oranda aromatize edilmiş yağ kalıntıları şu anda en yaygın hammaddedir.
Teknolojik parametreler üzerindeki etki
Koklaştırma tesisinin aşağıdaki parametreleri, besleme malzemelerinin özelliklerine bağlıdır:
- reaksiyon odasının verimliliği;
- alınan ürünlerin kalitesi;
- kok çıkışı;
- süreç için koşullar.
En önemli hammadde parametreleri şunlardır:
- Koklaşma, asf alt reçineli maddelerin içeriğine bağlı olarak. Koklaşma değeri %10-20 aralığında olmalıdır. Değer küçüldükçe kok verimi düşer ve daha büyük değerle fırınlarda kangalların içinde tortu birikir. Koklaştırma kapasitesi, içindeki yağ ürünü numunesinin ısıtılmasından sonra potadaki katı kalıntının kütlesi ile belirlenir.
- Yoğunluk.
- Kimyasal bileşim. İtibarenkok yayan kükürtün kalitesi üzerinde en büyük etkiye sahip olan zararlı safsızlıklar (ağırlıkça %1,5'ten fazla olmamalıdır). Kokun teknolojik süreçteki amacına bağlı olarak, farklı türde hammaddelerin kullanılması tercih edilir. Bu nedenle, nihai ürünün lifli bir yapısını elde etmek için parafin bazlı malzemeler kullanılır.
Kok verimi, besleme yoğunluğu ve asf alten içeriği ile orantılıdır.
Koklama aşamaları
Gecikmeli koklaştırma ünitelerindeki teknolojik süreç, hammadde tedarikinden bitmiş ürünün boş altılmasına kadar uzun ve süreklidir. Geleneksel olarak 3 aşamaya ayrılır:
- Dekompozisyon reaksiyonları, distilat fraksiyonlarının oluşumu, ara ürünler, yoğuşma.
- Gazlardaki doymamış hidrokarbonların içeriğinde önemli azalma, kalıntı bileşenlerin moleküler ağırlığında artış, siklizasyon reaksiyonları.
- Kalıntıdaki asf alten içeriğinde %26'ya varan artış, reçine ve yağ miktarında azalma. Sıvı kalıntıyı katı koka dönüştürün.
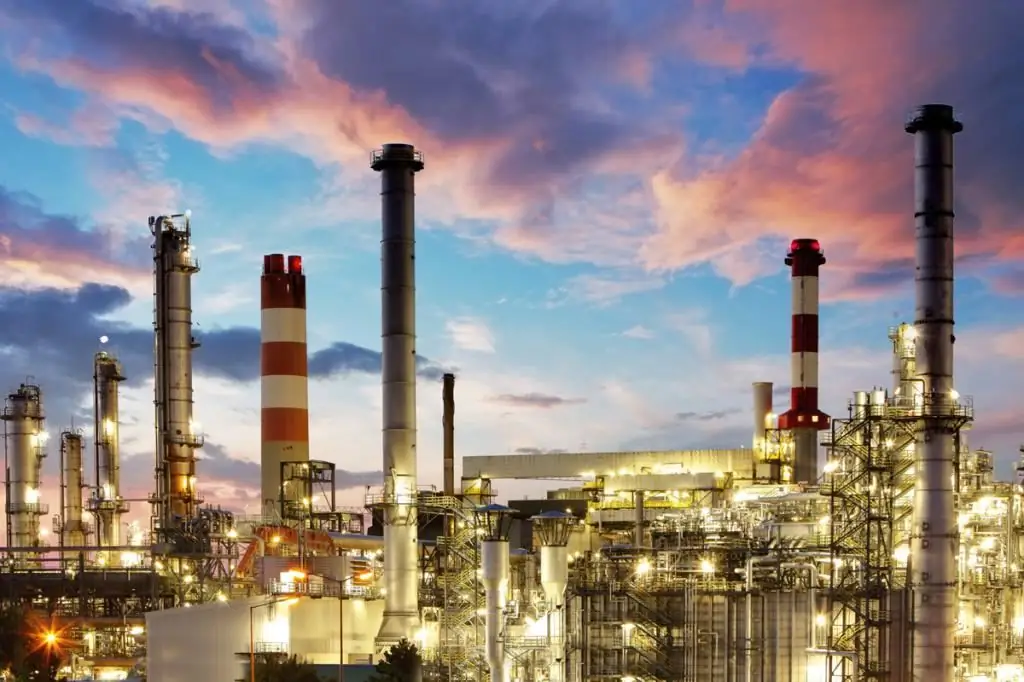
Sınıflandırma
Düzenlerine göre 2 ana tip gecikmeli kok ünitesi vardır: tek blok ve çift blok.
İki bloklu tesisler arasında, aşağıdaki tasarım ve teknolojik özelliklerle karakterize edilen 4 tip vardır:
- Koklaştırma odalarının iç çapı - 4,6 m Çadır ısıtma fırınları, çiftler halinde çalışan dört oda. Koklama işlemi sırasında elde edilen gazyağı ve gaz yağı ısıtma için kullanılır.
- Kolahazneler Ø 5,5 m Hammadde - kaliteli bir ürün verimini artıran yüksek aromatik hidrokarbonların eklenmesiyle düz akışlı akaryakıtlar.
- Alaşımlı çelikten Ø 5,5 m, yükseklik 27,6 m, hacimsel serme torçlu boru şeklinde fırınlar, artırılmış kesitli üst valfler, kok-köpük faz ayrımının konumunun kaydedilmesine izin veren radyoaktif seviye göstergeleri. En son yenilik, reaktörün faydalı hacminin daha iyi kullanılmasına yardımcı olur. Bobinlerin koklaşmasını az altmak için deterjan katkılı türbülatörlerin temini, kafa tüplerinde soğutulmuş gaz yağı.
- Reaksiyon odaları Ø 7 m, yükseklik 29,3 m Reaktörlere eksenel hammadde girişi, uzaktan kumandalı kok boş altmak için hidrolik sistem, elektrikli vinçler, zemin tipi depolu depolar.
Uygulamalı Ekipman
Bu tip tesisatlarla donatılmış ekipmanlar amaca göre aşağıdaki gruplara ayrılır:
- Teknolojik, doğrudan koklaştırma sürecine dahil (fırınlar, kolon ekipmanları, ısı eşanjörleri, reaktör odaları, küpler, buzdolapları, pompalar, boru hatları, enstrümantasyon, musluklar ve diğer kapatma ve anahtarlama vanaları).
- Atık su - çalışma döngüsüne geri dönmek için suyun toplanması ve arıtılması (soğutma ve kok çıkarma işlemleri).
- Odalardan (küpler) kok boş altmak için ekipman. Modern mekanize kurulumlarda, mekanik ve hidrolik tipte olabilir (sapanlar, vinçler, taraklar, kesiciler, çubuklar, kuleler, lastik manşonlar).
- Bitmiş ürünün taşınması ve işlenmesi için cihazlar (alıcı oluklar ve rampalar, vinçler, konveyörler, besleyiciler, kırıcılar, depolar).
- İşin mekanizasyonu için makineler ve ekipmanlar.
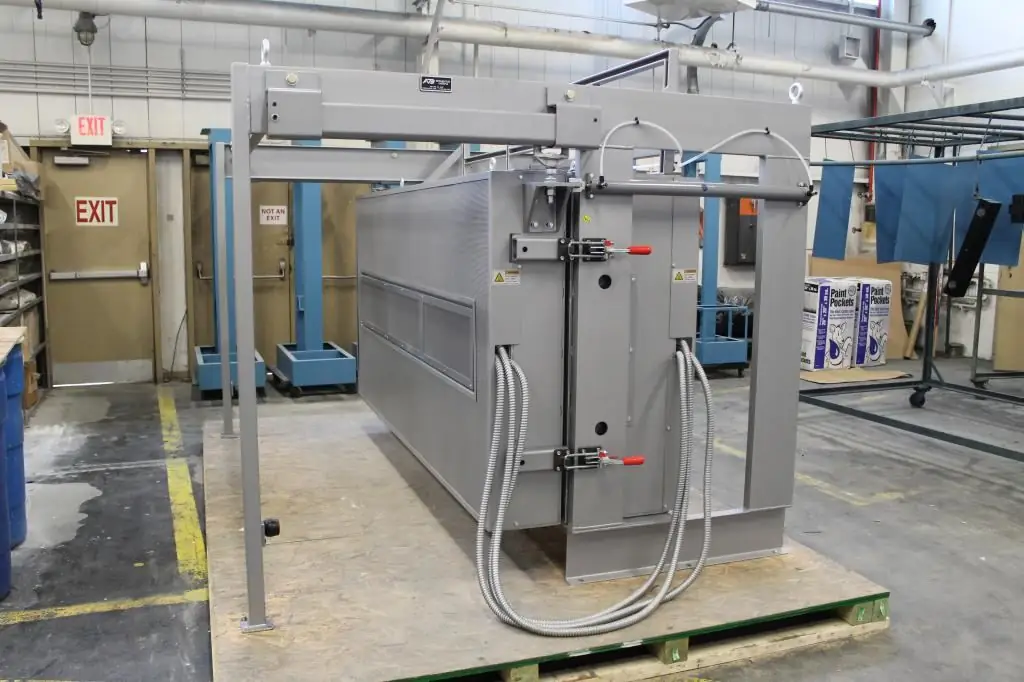
Gecikmeli kok tesislerini tasarlarken, çalışma döngüsünün süresi operasyonlarının güvenilirliğine bağlı olduğundan, reaksiyon odalarının ve fırınların tasarımını dikkatlice düşünmek gerekir.
Proses parametreleri
Koklaştırma teknolojisinin ana parametreleri:
- Fırınların reaksiyon bobinlerinin toplam yükünün, hammadde cinsinden tüm tesisin yüküne oranı olarak tanımlanan devridaim oranı. Değerinin artmasıyla yüksek kaliteli kok, gaz ve benzin verimi artar, ancak ağır gaz yağı miktarı azalır.
- Reaksiyon odasındaki basınç. Azalması gaz yağı veriminde artışa, kok ve gaz veriminde düşüşe ve köpürmede artışa neden olur.
- Proses sıcaklığı. Ne kadar büyük olursa, uçucu madde miktarı, gücü ve yoğunluğu açısından kok kalitesi o kadar yüksek olur. Maksimum değer, bobinlerin dayanıklılığını az altan fırın ve boru hatlarının koklaşma riski ile sınırlıdır. Her tür hammaddenin kendi optimum sıcaklığı vardır.
Gecikmeli koklaştırma ünitelerinin inşası, yüksek sermaye maliyetleriyle ilişkilidir. Bu nedenle, çoğu zaman halihazırda işleyen bir ekipman kompleksinin yeniden inşası gerçekleştirilir. Bu, döngüyü az altarak elde edilirkoklaştırma, yeni reaksiyon odalarının tanıtılması veya devridaim oranının düşürülmesi.
Çalışma prensibi
Gecikmeli koklama üniteleri, bir odanın kok üretimi aşamasında ve diğerinin boş altma veya bir ara durumda çalıştığı bir veya daha fazla eşleştirilmiş oda grubundan oluşur. Kaynak malzemenin ayrışma süreci, 470-510 °C'ye ısıtıldığı bir tüp fırında başlar. Bundan sonra, hammadde, beraberinde gelen ısı nedeniyle derin bir şekilde koklaştığı, ısıtılmamış odalara girer.
Gazlı ve sıvı hidrokarbonlar, damıtma kolonunda fraksiyonel ayırma için boş altılır. Kok, boş altıldığı, sıralandığı ve taşındığı mekanik işleme bölümüne girer. Bitmiş ürün tabakasına bir kuyu açılır ve içine bir hidrolik kesici yerleştirilir. Nozulları 20 MPa'ya kadar basınç altında çalışır. Ayrılan kok parçaları, suyun tahliye edildiği bir drenaj platformuna düşer. Ürün daha sonra daha küçük parçalara ezilir ve fraksiyonlara ayrılır. Ardından, kok depoya taşınır.
Ultrasonik testin prensip şeması aşağıdaki şekilde gösterilmektedir.
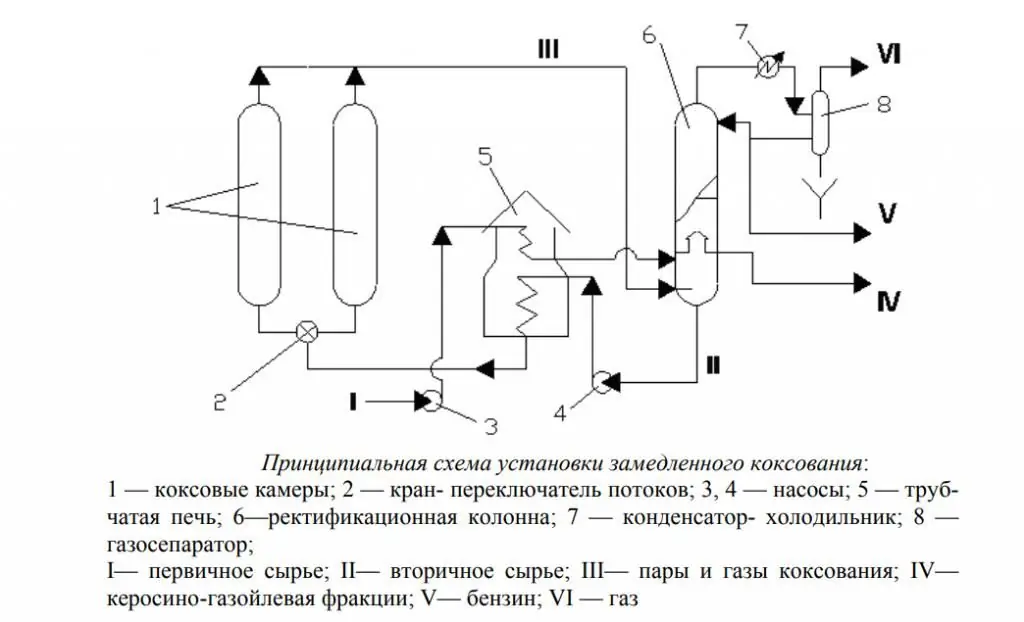
Kok odaları
Bölmeler, tüm kurulumun temeli olan bir reaktördür. Haznenin çalışma döngüsü genellikle 48 saattir, ancak son yıllarda 18 ve 36 saat modlarında çalışan ultrasonik cihazlar tasarlanmıştır.
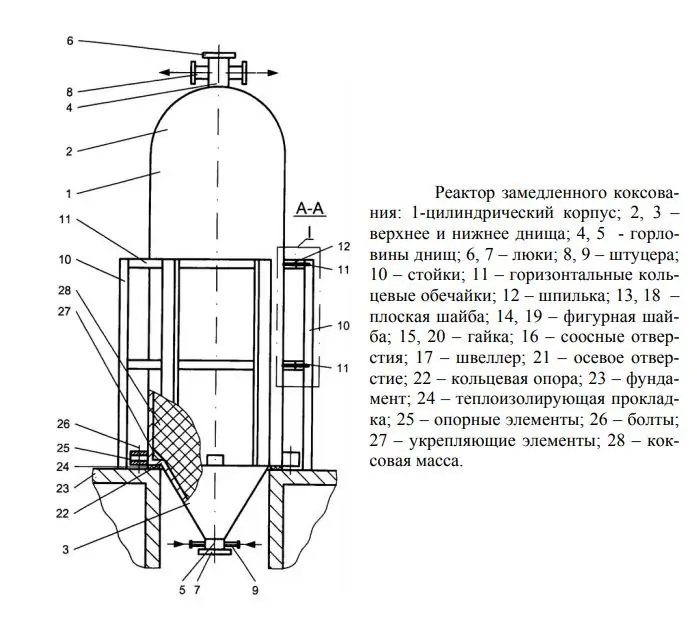
Bir reaktör çalışma döngüsü aşağıdaki işlemlerden oluşur:
- hammadde yükleme, koklaştırma işlemi (1 gün);
- kapalı (1/2 saat);
- hidrotermal arıtma (2,5 saat);
- Ürünün su ile soğutulması, suyun uzaklaştırılması (4 saat);
- Ürünü boş altın (5 saat);
- rögarların sızdırmazlığı, sıcak buharla basınç testi (2 saat);
- yağ buharları ile ısıtma, çalışma döngüsüne geçiş (3 saat).
Tasarım
Gecikmeli kok ünitesi projesi aşağıdaki sırayla geliştirilmektedir:
- gerekli üretkenliğin belirlenmesi, t/yıl;
- kaynak tabanı analizi;
- çeşitli hammadde türleri için koklaştırma işleminin teorik bir malzeme dengesinin oluşturulması;
- ana malzeme akışlarının belirlenmesi;
- kurulum konseptinin geliştirilmesi;
- reaktörlerin boyutu ve sayısı için gerekçe;
- bir odayı kokla doldurma süresinin belirlenmesi ve hidrolik hesaplaması, reaktörün çalışması için bir program hazırlanması;
- odadaki sıcaklık yükünün hesaplanması;
- konveksiyon ve radyasyon odalarının hesaplanması;
- üretim hattı düzeninin geliştirilmesi;
- diğer ana ekipmanların teknolojik hesaplamaları (damıtma kolonu, fırınlar, buzdolapları vb.);
- bir izleme ve kontrol sisteminin geliştirilmesi, otomasyon araçlarının seçimi;
- acil koruma planlarının açıklaması;
- çevresel boyutların ve güvenlik önlemlerinin geliştirilmesi;
- ekonomik göstergelerin belirlenmesi (sermaye maliyetleri, hizmet personeli sayısı, bordro,hammadde ve yardımcı malzemeler için üretim maliyetleri, yıllık ekonomik etki, ürün maliyeti.
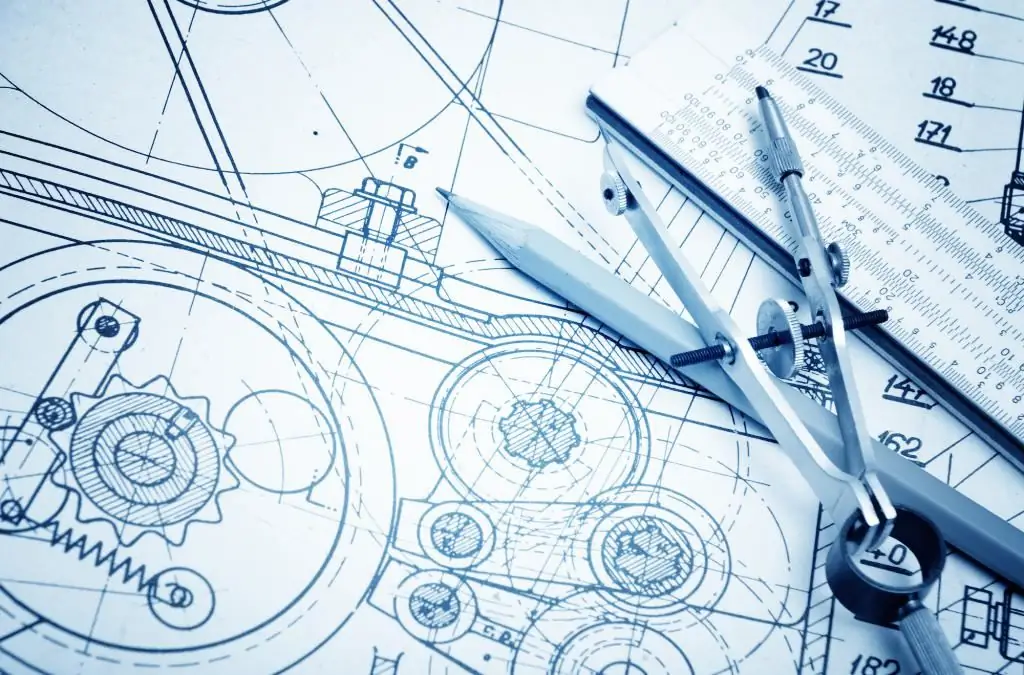
Gecikmeli koklama ünitesinin yıllık olarak kapasitesinin hesaplanması aşağıdaki formüle göre yapılır:
N=P x t, burada P, tesisin kapasitesidir, t/gün;
t, bir yıldaki çalışma günü sayısıdır.
Tesisatın malzeme dengesine göre temel ve tasarım seçeneklerine göre fiziksel olarak ürün çıktısı belirlenir.
Önerilen:
Ark çelik fırını: cihaz, çalışma prensibi, güç, kontrol sistemi
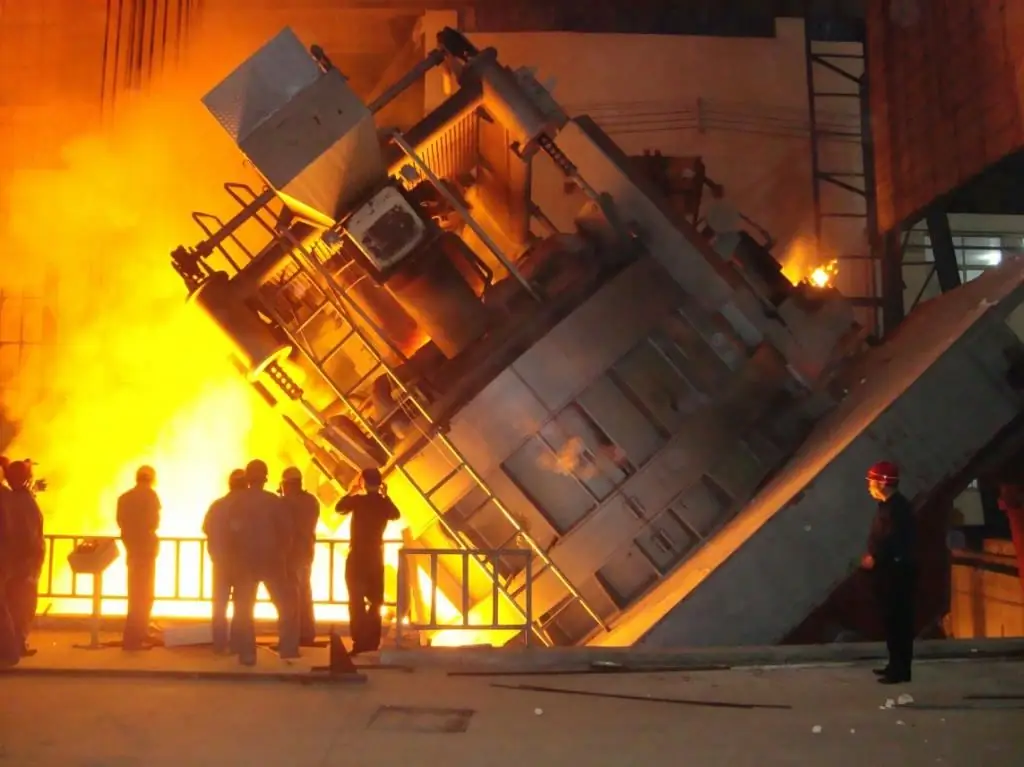
Ark çelik eritme fırınları (EAF'ler), yüklenen malzemenin doğrudan elektriksel bükülmeye maruz kalması ve terminallerdeki akımın yüklü malzemeden geçmesiyle endüksiyon fırınlarından farklıdır
Reaktif güç nedir? Reaktif güç kompanzasyonu. reaktif güç hesabı
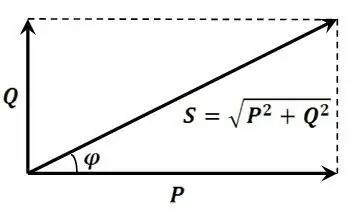
Gerçek üretim koşullarında, endüktif nitelikteki reaktif güç hakimdir. İşletmeler bir değil, biri aktif olmak üzere iki elektrik sayacı kuruyor. Ve elektrik hatları aracılığıyla boşuna “kovalanan” enerjinin aşırı tüketimi için, ilgili makamlar acımasızca para cezasına çarptırılır
Yardımcı güç ünitesi: özellikler, amaç, cihaz ve kaynak göstergeleri
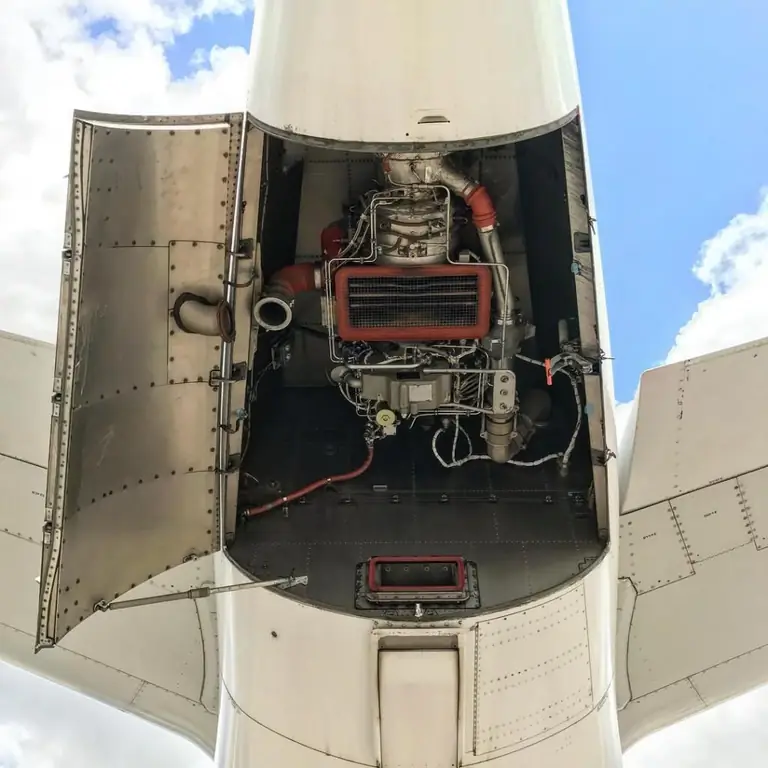
Yardımcı güç ünitesi veya APU, havacılık teknolojisinde çok sık kullanılan bir ünitedir. Kendi başına bu tesisat mekanik enerji elde etmek için gereklidir. Ancak, araçları hareket ettirmek için kullanılamaz
HPP: çalışma prensibi, şema, ekipman, güç
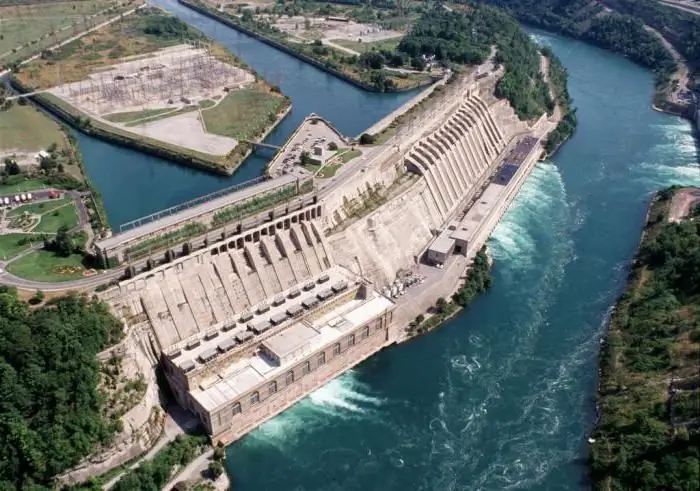
Hemen hemen herkes hidroelektrik santrallerin amacını hayal eder, ancak yalnızca birkaçı hidroelektrik santrallerin çalışma prensibini gerçekten anlar. İnsanlar için asıl gizem, bu devasa barajın hiç yakıt kullanmadan nasıl elektrik enerjisi ürettiğidir. Bunun hakkında konuşalım
Ytterbium fiber lazer: cihaz, çalışma prensibi, güç, üretim, uygulama
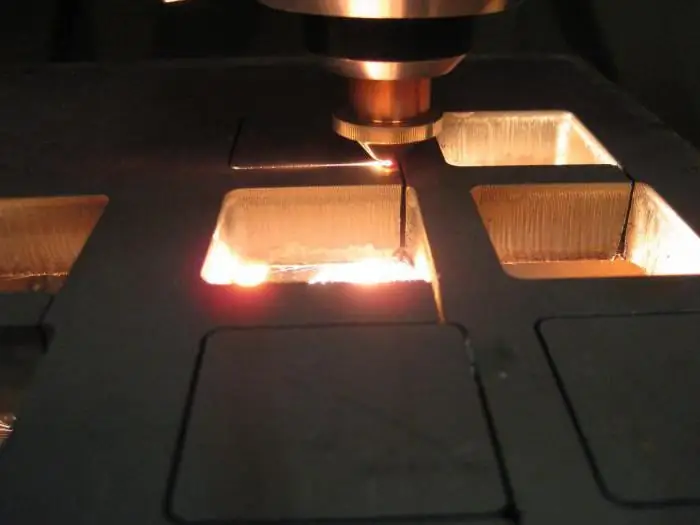
Fiber lazerler kompakt ve dayanıklıdır, hassas bir şekilde işaret eder ve termal enerjiyi kolayca dağıtır. Pek çok biçimde gelirler ve diğer optik kuantum üreteçleri türleriyle çok ortak noktaları olduğundan kendilerine özgü avantajları vardır